

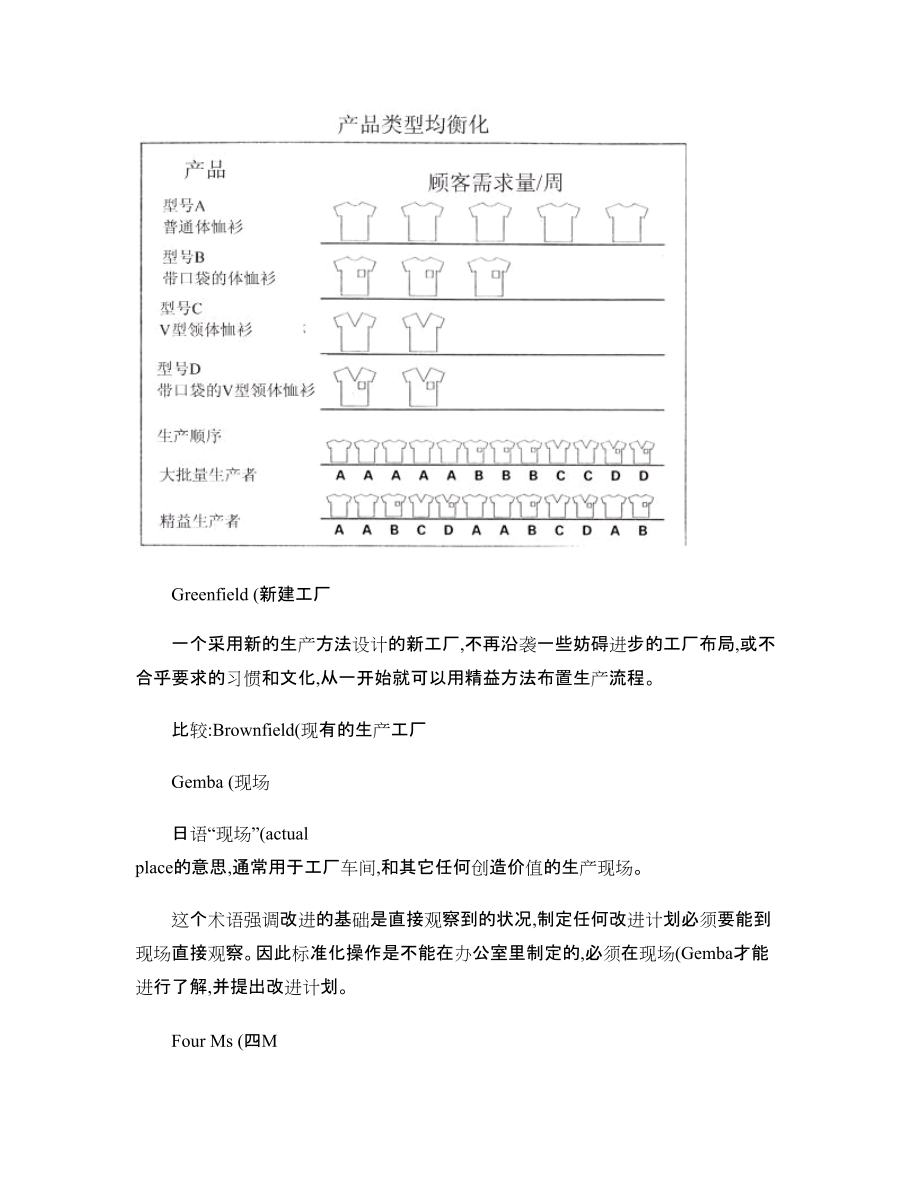


版權(quán)說明:本文檔由用戶提供并上傳,收益歸屬內(nèi)容提供方,若內(nèi)容存在侵權(quán),請進行舉報或認領(lǐng)
文檔簡介
1、精益術(shù)語(下Inspection (檢查在大批量生產(chǎn)中,專業(yè)檢驗員在制造產(chǎn)品的工序外,檢查產(chǎn)品質(zhì)量的行動。精益制造商在生產(chǎn)工序中,使用防止錯誤的設(shè)施,并且把質(zhì)量保證的任務(wù)分配給操作員。如果發(fā)現(xiàn)有質(zhì)量問題,經(jīng)由質(zhì)保小組找出問題的源頭所在。這個工序不僅要防止缺陷進入到后續(xù)工序,而且要停下來確定原因,并采取糾正措施。Heijunka Box (生產(chǎn)均衡柜在固定的時間間隔里,利用看板來平衡產(chǎn)品的型號和數(shù)量的工具,稱為生產(chǎn)均衡柜。由于看板槽代表了對材料和信息流的定時,因此看板槽內(nèi)的每塊看板,就代表了生產(chǎn)一種型號產(chǎn)品的一個批量時間(批量時間Pitch =節(jié)拍時間×每批次的產(chǎn)品數(shù)量。例如產(chǎn)品A的批
2、量時間為20分鐘,那么每個時間間隔的看板槽里就放一張看板;產(chǎn)品B的批量時間為10分鐘,那么每個看板槽里就各放兩張看板;產(chǎn)品C的批量時間為40分鐘,因此每隔一個看板槽放置一張看板。產(chǎn)品D和E共用一個生產(chǎn)工序,并且D產(chǎn)品與E產(chǎn)品的需求比例為2:1,因此把D 產(chǎn)品的兩張看板分別放在前兩個間隔里,而在第三個間隔里放入E產(chǎn)品的一張看板,以此循環(huán)下去。由上文闡述的方法可以看出,生產(chǎn)均衡柜是一個工具,能夠在一定時間內(nèi),用看板平衡多種產(chǎn)品的混合生產(chǎn)與數(shù)量,例如,確保在半小時內(nèi),以一個穩(wěn)定的產(chǎn)品比例,來制造小批量的D和E。參見:EPEx(每個產(chǎn)品每次間隔,Heijunka(均衡化,Kanban (看板,Mate
3、rial Handling(材料搬運,Paced Withdrawal(有節(jié)奏的提取,Pitch(批量時間。Heijunka (均衡化在固定的生產(chǎn)周期內(nèi),平衡產(chǎn)品的類型與數(shù)量。這樣可以在避免大量生產(chǎn)的同時,有效的滿足顧客的需求,最終帶來整條價值流中的最優(yōu)化的庫存、投資成本、人力資源以及產(chǎn)品交付期。舉例說明“按照客戶需求的產(chǎn)品數(shù)量來均衡生產(chǎn)”:假設(shè)一個制造商每周都收到500個產(chǎn)品的訂單,但是每天收到的訂單的產(chǎn)品數(shù)量卻有著顯著的差別:周一要運送200個,周二100個,周三50個,周四100個,周五再運送50個。為了平衡產(chǎn)量,制造商可能會把少量的已經(jīng)完工的產(chǎn)品儲存在裝運處,作為一種緩沖來滿足周一的高
4、需求量,并按照每天生產(chǎn)100個產(chǎn)品的產(chǎn)量,來平衡整個一周的生產(chǎn)。通過在價值流終點庫存少量成品,制造商可以平衡顧客的需求,同時,更有效地利用整條價值流的資源。舉例說明“按照產(chǎn)品類型來平衡產(chǎn)量”:請看圖示,假設(shè)一家襯衫公司為人們提供A,B,C,D四種樣式的襯衫,而顧客每周對這些襯衫的需求量為5件A型,3件B型,以及C型和D型各兩件。對于追求規(guī)模經(jīng)濟性,希望盡可能減少換模的大批量制造商而言,他們很可能會按照AAAAABBBCCDD這樣的生產(chǎn)次序來制造產(chǎn)品。然而,一個精益制造商,可能會考慮按照AABCDAABCDAB的次序來生產(chǎn)產(chǎn)品,并通過適當(dāng)?shù)南到y(tǒng)改進,減少換模時間。同時根據(jù)顧客訂單的變化,對生產(chǎn)次
5、序進行周期性的調(diào)整。參見:Demand Amplification(需求擴大,EPEx(生產(chǎn)批次頻率, JIT(及時生產(chǎn),Muda(浪費,Mura,Muri,SMED。 Greenfield (新建工廠一個采用新的生產(chǎn)方法設(shè)計的新工廠,不再沿襲一些妨礙進步的工廠布局,或不合乎要求的習(xí)慣和文化,從一開始就可以用精益方法布置生產(chǎn)流程。比較:Brownfield(現(xiàn)有的生產(chǎn)工廠Gemba (現(xiàn)場日語“現(xiàn)場”(actual place的意思,通常用于工廠車間,和其它任何創(chuàng)造價值的生產(chǎn)現(xiàn)場。這個術(shù)語強調(diào)改進的基礎(chǔ)是直接觀察到的狀況,制定任何改進計劃必須要能到現(xiàn)場直接觀察。因此標準化操作是不能在辦公室里制
6、定的,必須在現(xiàn)場(Gemba才能進行了解,并提出改進計劃。Four Ms (四M生產(chǎn)系統(tǒng)為顧客創(chuàng)造價值的4個M。前三個M代表資源,第四個M指使用資源的方法。在一個精益系統(tǒng)中,這四個M表示:1.材料(Material無缺陷或短缺2.機器(Machine無損壞,缺陷,或是計劃外的停機3.人(Man良好的工作習(xí)慣,必要的技能,準時,無曠工4.方法(Method標準化的工序,維護,以及管理Flow Production (流水線生產(chǎn)亨利.福特(Henry Ford于1913年在密歇根州的Highland Park,建立的生產(chǎn)系統(tǒng)。流水線生產(chǎn)通過一系列的生產(chǎn)方法,包括使用通用的設(shè)備,使生產(chǎn)線上的每項任務(wù)
7、都有穩(wěn)定的周期時間,并按照加工工序的順序,使產(chǎn)品能夠迅速、平穩(wěn)的由一個工位“流動”到下一個工位。經(jīng)由生產(chǎn)控制系統(tǒng),使產(chǎn)品的生產(chǎn)率與最終裝配線上的使用率相符合。參見:Continuous Flow(連續(xù)流對比:Mass Production(大批量生產(chǎn)Fixed-Position Stop System (固定工位來停止生產(chǎn)一種通過在某個固定的位置,停止裝配線運轉(zhuǎn)來解決問題的方法。這類問題通常是指那些已經(jīng)檢測到,但無法在生產(chǎn)周期中解決的問題。當(dāng)操作員發(fā)現(xiàn)零件、設(shè)備、材料供應(yīng)、安全等方面的問題之后,會拉動一根燈繩或是按動一個信號燈,來提醒管理人員。管理人員在評估問題之后,決定是否在生產(chǎn)周期結(jié)束之前
8、解決問題。如果問題可以在生產(chǎn)周期內(nèi)解決,管理人員就會停止信號系統(tǒng),以保證生產(chǎn)線繼續(xù)運轉(zhuǎn),同時進行解決方案;如果不能解決,那么生產(chǎn)線就必須在生產(chǎn)周期完成后來解決問題。豐田公司率先開創(chuàng)這套固定工位停止生產(chǎn)線的方法,其目的在于解決三個問題:(1生產(chǎn)現(xiàn)場管理員通常不太情愿拉動信號燈繩;(2在生產(chǎn)周期內(nèi),處理可以解決的小問題,消除不必要的生產(chǎn)中斷;以及(3在生產(chǎn)周期的終點,而不是在中間停止生產(chǎn)線運轉(zhuǎn),以避免重新啟動生產(chǎn)線時,所導(dǎo)致的混亂,以及質(zhì)量及安全等方面的問題。固定工位停止生產(chǎn)線是一種自動化(Jidoka的方法,或者說是一種沿著裝配線的質(zhì)量控制(building in quality。參見:Ando
9、n(信號燈,Automatic Line Stop(自動停止生產(chǎn)線, Jidoka(自動化Five Whys (五個“為什么”當(dāng)遇到問題的時候,不斷重復(fù)問“為什么”,目的要發(fā)現(xiàn)隱藏在表面下的問題根源。例如,Taichi Ohno 曾舉過這樣一個關(guān)于機器故障停機的例子(Ohno 1988, p.17:1.為什么機器停止工作?機器超負荷運轉(zhuǎn)導(dǎo)致保險絲燒斷了。2.為什么機器會超負荷運轉(zhuǎn)?沒有能夠?qū)S承進行充分的潤滑3.為什么沒有給軸承充分的潤滑?潤滑油泵泵送不足4.為什么泵送不足?潤滑泵的轉(zhuǎn)軸過于陳舊,甚至受損發(fā)出了“卡嗒卡嗒”的響聲。5.為什么轉(zhuǎn)軸會破舊受損?由于沒有安裝附加濾網(wǎng),導(dǎo)致金屬碎屑進入
10、了油泵。如果沒有反復(fù)的追問“為什么”,操作員可能只會簡單的更換保險絲或者油泵,而機器失效的情況仍會再次發(fā)生?!拔濉辈⒉皇顷P(guān)鍵所在,可以是四,也可以是六、七、八關(guān)鍵是要不斷的追問,直到發(fā)現(xiàn)并消除掉問題的根源。參見:Kaizen(改進;Plan(計劃,Do(實施,Check(檢查, Act(行動。5S五個都以“S”開頭的相關(guān)術(shù)語,用來描述可視化控制,及精益生產(chǎn)的現(xiàn)場操作。在日語里這五個術(shù)語是:1.整理(Seiri:從必要的項目¬工具,零件,材料,文件中分離,并丟棄那些不必要的東西2.整頓(Seiton:整潔地布置工作區(qū)域,把所有東西放到它們應(yīng)該在的位置上3.清掃(Seiso:打掃與清洗4
11、.清潔(Seitetsu:常規(guī)性的執(zhí)行前三個S所導(dǎo)致的清潔5.紀律(Shitsuke:執(zhí)行前四個S的紀律5S通常被英譯為分類,清理,光亮,標準化,以及持久。一些精益思想的實踐者另外添加了第六個S安全,在車間和辦公室內(nèi)建立并實施安全程序。但是豐田公司傳統(tǒng)上只提前4個S:1.整理(Seiri:詳細檢查工作區(qū)域內(nèi)的所有物品,挑出并清除不需要的物品2.整頓(Seiton:按照整齊的,便于使用的方式布置需要的物品3.清掃(Seiso:清理干凈工作區(qū)域,設(shè)備,以及工具4.清潔(Seitetsu:由嚴格執(zhí)行前三個S所導(dǎo)致的全面的清潔和秩序放棄第五個S,是因為在豐田公司,每天、每周、每個月審核標準化操作的系統(tǒng)
12、下,再強調(diào)紀律顯得多余。無論是使用4S,5S,還是6S,關(guān)鍵在于整個企業(yè)所有員工的全面切換,而不是臨時的、孤立的一個個項目。參見:Standardized Work(標準化操作First In, First Out (FIFO (先進先出一種維持生產(chǎn)和運輸順序的實踐方法。先進入加工工序或是存放地點的零件,也是先加工完畢或是被取出的產(chǎn)品。這保證了庫存的零件不會放置太久,從而減少質(zhì)量問題。FIFO是實施拉動系統(tǒng)的一個必要條件。先進先出最好的例子,是一個能承放固定數(shù)量產(chǎn)品的斜槽,供應(yīng)未制成品從槽的入口處開始,而下游工序取貨安排在槽的出口處。如果先進先出排列已經(jīng)滿了,那么供應(yīng)就必須停止,直到下游工序開
13、始使用槽中庫存。FIFO可以防止上游工序過量生產(chǎn),甚至適用于那些不是連續(xù)流或庫存超市的生產(chǎn)工序。對于兩個生產(chǎn)工序中間不適用庫存超市的情況,FIFO是一種很好的拉動系統(tǒng)。因為某些零件可能非常特別(one of a kind,或是有著很短的“貨架壽命”(shelf lives,或是非常昂貴,但又經(jīng)常需要的。運用這種方法,從FIFO斜槽里取走一個零件,會自動引發(fā)上游工序生產(chǎn)一個補充的零件。參見:Kanban(看板,Pull System(拉動系統(tǒng),Supermarket(庫存超市Fill-Up System (填補系統(tǒng)在一個拉動生產(chǎn)系統(tǒng)中,前面的工序只生產(chǎn)“夠用”的產(chǎn)品,來取代或是填補后續(xù)工序提取的
14、產(chǎn)品。參見:Kanban(看板,Pull Production(拉動系統(tǒng),Supermarket (庫存超市Every Product Every Interval (EPEx (生產(chǎn)批次頻率在同一條生產(chǎn)線中,生產(chǎn)不同型號產(chǎn)品的頻率。如果工序中的一臺機器,每三天換模一次,來生產(chǎn)不同的產(chǎn)品,那么生產(chǎn)批次間隔EPEx就是三天。一般而言,EPEx應(yīng)當(dāng)越小越好,這樣就可以按照小批量,來生產(chǎn)不同型號的產(chǎn)品,從而把庫存量減到最小。然而,一臺機器的生產(chǎn)批次間隔,通常取決于換模時間,以及零件種類的多少。用一臺換模時間很長的機器,來生產(chǎn)多樣產(chǎn)品,就不可避免的會產(chǎn)生較長的生產(chǎn)批次間隔時間,除非能夠減縮短換模時間,
15、或是減少零件的種類數(shù)目。參見:Heijunka(均衡化Error-Proofing (預(yù)防差錯防止操作員在工作中出現(xiàn)由于選錯、遺漏,或是裝反零件等操作,而導(dǎo)致質(zhì)量缺陷的方法。也稱為錯誤預(yù)防(mistake-proofing, Poka-yoke(差錯預(yù)防,以及Baka-yoke(fool-proofing 傻子都犯不了錯誤常見的例子包括:為產(chǎn)品設(shè)計特殊的物理形狀,使得操作員只能按正確的位置,而不可能從其它方向裝配。零件箱上方的光電控制設(shè)備,防止操作員在拿到正確的零件前,進行下一個工序。一個較復(fù)雜的產(chǎn)品監(jiān)視系統(tǒng),使用光電控制設(shè)備,但增加了邏輯控制,以保證操作員在進行裝配時,選用正確的零件組合。參
16、見:Inspection(檢查,Jidoka(自動化Efficiency (效率用最少的資源,最準確的達到顧客的要求。Apparent Efficiency(表面效率與True Efficiency(真實效率 Taiichi Ohno用一個“10人每天生產(chǎn)100件產(chǎn)品”的例子闡述了人們經(jīng)?;煜摹氨砻嫘省焙汀罢鎸嵭省钡暮x。如果通過改進,使每天的產(chǎn)量達到120個零件,效率表面看起來有了20%的提高。如果需求也增加20%,這表示真實效率提高了。如果需求還保持在100,那么提高真實效率的唯一途徑,就是如何以更少的投入,生產(chǎn)出相同數(shù)量的零件用8個人每天生產(chǎn)100件產(chǎn)品。Total Efficie
17、ncy(總效率與Local Efficiency(局部效率豐田公司通常把總效率(整個生產(chǎn)過程或是價值流和局部效率(對一個生產(chǎn)工序,或是價值流中的某一點,或某一個步驟的操作區(qū)別開來。他們往往更注重于前者,而不是后者。參見:Overproduction(過量生產(chǎn),Seven Wastes(七種浪費。Downtime (停工期計劃的或是未計劃的停工而損失的生產(chǎn)時間。計劃的停工時間,包括預(yù)定的的生產(chǎn)會議,換模,以及計劃中的維護工作所花費的時間。非計劃的中斷時間包括故障導(dǎo)致的中斷、機器調(diào)整、材料短缺、以及曠工所導(dǎo)致的時間損耗。參見:Overall Equipment Effectiveness(整體設(shè)備
18、效率,Total Productive Maintenance(總生產(chǎn)維護。Design-In (共同設(shè)計顧客與供應(yīng)商共同合作設(shè)計產(chǎn)品,及其制造工藝的方法。典型的方法是顧客提供成本與性能指標(有時稱為一個“信封套”,而供應(yīng)商迅速的進行產(chǎn)品的詳細工程和制造工藝設(shè)計(加工,布局,質(zhì)量等。供應(yīng)商通常會派遣一名“常駐工程師”在顧客的工廠或設(shè)計工程中心,以確保產(chǎn)品能夠在整個系統(tǒng)中良好的運轉(zhuǎn),將總成本降到最小。Demand Amplification (需求擴大在多級生產(chǎn)過程中,當(dāng)上游收到的訂單數(shù)量,遠比下游的生產(chǎn),或銷售數(shù)量多的現(xiàn)象,這也稱為Forrester效應(yīng)(二十世紀五十年代MIT的Jay For
19、rester 首次用數(shù)學(xué)方法定義了這種現(xiàn)象的特征或是牛鞭效應(yīng)(Bullwhip Effect。導(dǎo)致需求擴大的兩個主要原因是:(a太多可以調(diào)整訂單的決策點;(b在等待訂單處理期間以及傳遞訂單過程中的延誤(例如等待每周運行一次的材料需求計劃的程序。延誤的時間越長,需求擴大就越嚴重,因為預(yù)測的數(shù)量越不準確。為了盡可能的減少需求擴大,精益思想者會通過在價值流的每個階段,經(jīng)常性的提取裝運指令,來平衡拉動系統(tǒng)。需求變化圖表是一個非常好的方法,可以提高大家對生產(chǎn)系統(tǒng)需求擴大的認識。如果能夠完全消除需求擴大,那么這個價值流上每一點的訂單變化都將是±3%,從而真實的反映了顧客需求的變化。參見:Buil
20、d-to-order(按訂單制造,Heijunka(均衡化,Level Selling (均衡銷售Value-Creating Time (增值時間在生產(chǎn)的過程中,能實際為顧客增加價值的工序時間。通常增值時間要短于周期時間,周期時間又要短于產(chǎn)品交付時間參見:Value(價值Production Lead Time (產(chǎn)品交付期Production Lead Time(產(chǎn)品交付期,也稱為產(chǎn)出時間throughput time或Total Product Cycle Time總產(chǎn)品周期時間生產(chǎn)一件產(chǎn)品,從開始直至結(jié)束所需要的時間。在車間里通常稱之為“大門到大門”時間。這個概念還可以應(yīng)用于產(chǎn)品從開始
21、設(shè)計到結(jié)束的過程;或是把原材料,經(jīng)過一系列工序加工成產(chǎn)品的時間。與時間相關(guān)的術(shù)語Effective Machine Cycle Time(有效機器周期時間機器周期時間(Machine Cycle Time加上裝載與卸載的時間,再加上單個產(chǎn)品的平均換模時間。例如,如果一臺機器的節(jié)拍時間為20s,加上裝載與卸載所需的30s,以及換模時間30s除以最小批量零件數(shù)30,那么有效機器周期時間就等于20+30+1=51秒。Machine Cycle Time(機器周期時間用機器加工,完成一件產(chǎn)品總共需要的時間。Non Value-Creating Time(非增值時間從顧客的觀點來看,花費在那些增加成本,
22、但不增加產(chǎn)品價值的活動上的時間。典型的例子包括庫存,檢查,以及返工。 Operator Cycle Time(操作員周期時間在重復(fù)同樣工作之前,操作員在工位上,完成所有工作所需要的時間。這個時間通常直接由實際觀察測量得到。Order Lead Time(訂單交付期產(chǎn)品交付期加上將產(chǎn)品運輸?shù)娇蛻舻臅r間。包括處理訂單的延誤、將訂單輸入生產(chǎn)系統(tǒng)的時間,或由于顧客訂單超過生產(chǎn)能力而導(dǎo)致的等待時間等等。簡而言之,就是顧客要為產(chǎn)品等待的總時間。Order to Cash Time(訂單到現(xiàn)金時間從收到顧客訂單到收到貨款,所經(jīng)過的時間。這個時間可能比訂單交付時間長,也可能會短,主要取決于產(chǎn)品是按訂單生產(chǎn),還
23、是從庫存裝運,以及支付方式等等。Processing Time(加工時間真正用于設(shè)計或是生產(chǎn)一個產(chǎn)品的時間。通常情況下,加工時間只是產(chǎn)品交付期的一小部分。Cycle Time (周期時間指的是制造一件產(chǎn)品需要的時間,通常由觀察得出。這個時間等于操作時間加上必要的準備、裝載,及卸載的時間之和。周期時間的計算往往與所選擇的對象相關(guān)。例如,某個噴漆工序完成一個共22個零件需要五分鐘,那么對于這一個批量而言,周期時間就是五分鐘。然而,對于這個批量里的每個零件而言,周期時間則為13.6秒(5分鐘x 60秒= 300秒, 300秒/ 22= 13.6秒Cross-Dock (交叉貨倉一個用來分類和重新組合
24、眾多供應(yīng)商所提供的不同產(chǎn)品的庫房,繼而再將完成分類或裝配的產(chǎn)品運發(fā)至不同的顧客。例如裝配廠,批發(fā)商或是零售商等。常見的例子是那些擁有多個工廠的制造商,他們通常會為了能夠高效率的接收眾多供應(yīng)商所發(fā)來的貨物,而專門設(shè)立的一間貨倉。當(dāng)一輛裝滿了不同產(chǎn)品的卡車到達貨倉的時候,貨物立即被卸下,并被放置到多條傳輸通道上,以便裝載到開往不同工廠的卡車上。由于交叉貨倉不用來存放貨物,因此它不一定是一個倉庫。取而代之的是,通常貨物從入倉的汽車上卸下,再被運送到傳輸通道,并傳送至出倉的汽車上,是一步完成的。只要汽車的出倉頻率夠高,就有可能保持交叉貨倉的地上24小時沒有囤積。Continuous Flow (連續(xù)流
25、通過一系列的工序,在生產(chǎn)和運輸產(chǎn)品的時候,盡可能的使工序連續(xù)化,即每個步驟只執(zhí)行下一步驟所必需的工作。連續(xù)流可以通過很多種方法來實現(xiàn),包括將裝配線改造成手工生產(chǎn)單元(manual cell等。它也被稱為一件流(one-piece flow,單件流(single-piece flow,以及制造一件,移動一件。參見:Batch and Queue(批量生產(chǎn),flow production(連續(xù)流生產(chǎn), One-Piece Flow(單件流。Changeover (換模通過更換模具(也稱為安裝set-up,用同樣的機器或裝配線,生產(chǎn)不同的產(chǎn)品。換模時間的計算,從換模前加工完最后一個零件算起,到換模后
26、加工完第一個合格的零件結(jié)束。參見:Single Minute Exchange of Die(一分鐘更換模具Chaku-Chaku (一步接一步是一種實施單件流的方法。在一個生產(chǎn)單元里,機器可以自動的卸載產(chǎn)品,從而使操作員(也可能多名操作員可以不用停機,就能夠直接把工件,從一臺機器運送到另一臺機器上。這樣可以達到節(jié)省時間,減少操作員做非增值的工作。例如,在一個生產(chǎn)單元里,第一臺機器在它的生產(chǎn)周期結(jié)束后,自動將工件送出,操作員把這個工件放到第二臺機器上。而此時,第二臺機器也恰好結(jié)束其上一個周期,并送出加工完的工件。操作員裝載新的工件之后,啟動機器,并接著把這臺機器完成的工件,運送到它后面的那臺機
27、器上,以此類推在這個單元里進行下去。這個術(shù)語在日語中的字面意思是“一步接一步”。參見:Cell(生產(chǎn)單元,Continuous Flow(連續(xù)流Cell (生產(chǎn)單元制造產(chǎn)品的各個工位之間,緊密連接近似于連續(xù)流。在生產(chǎn)單元里,無論是一次生產(chǎn)一件還是一小批,都通過完整的加工步驟來保持連續(xù)流。U型(如下圖所示單元非常普遍,因為它把走動距離減小到最少,而且操作員可以對工作任務(wù)進行不同的組合。這是精益生產(chǎn)中一個非常重要的概念,因為U型單元里的操作員人數(shù)可以隨著需求而改變。在某些情況下,U型單元還可能安排第一個和最后一個工序,都由同一個操作員完成,這對于保持工作節(jié)奏與平順流動是非常有幫助的。很多公司都交換
28、使用“Cell”和“Line”這兩個術(shù)語。參見:Continuous Flow(連續(xù)流,Operator Balance Chart(操作員平衡表,Standardized Work(標準化操作。 Capital Linearity (線性化的設(shè)備投資一種設(shè)計生產(chǎn)或采購設(shè)備的方法,能夠以最少的資金投入,滿足客戶的需求變化。例如,投資一套年產(chǎn)力為100,000件產(chǎn)品的設(shè)備,或是采購十套較小的設(shè)備,分裝到十個年產(chǎn)力為10,000件的生產(chǎn)單元中。如果100,000件產(chǎn)品的需求是正確的話,那么這條具備100,000件生產(chǎn)能力的單一生產(chǎn)線就很可能是最經(jīng)濟的投資方式。然而,如果需求是105,000個部件的
29、話,情況就不相同了:廠商要么需要再購買一整條生產(chǎn)線(再添加100,000件的生產(chǎn)力,要么就得拒絕訂單。如果廠商采取的是安裝十個單元的計劃,那么當(dāng)需求為105,000個部件時,廠商可以再采購一個單元的設(shè)備。這種情況下,由需求變化所引起的,每件產(chǎn)品的平均投資變化將會非常微小。參見:Labor Linearity(勞動力線性化,Monument(紀念碑, Right-sized Tools(適度裝備。Build-to-Order (按訂單制造生產(chǎn)者完全按照訂單的數(shù)量,而不是根據(jù)市場需要預(yù)測生產(chǎn),使產(chǎn)品交付期盡可能的滿足客戶的要求。這是精益思想家們所力求實現(xiàn)的目標,因為它避免了根據(jù)預(yù)測生產(chǎn)所必然導(dǎo)致的浪費。參見:Demand Amplification(需求擴大,Heijunka(均衡化, Level Selling(均衡銷售Batch and Queue (批量生產(chǎn)一種生產(chǎn)方法,指不考慮實際的需求,而大批量的生產(chǎn),導(dǎo)致半產(chǎn)品堆積在下一個生產(chǎn)工序,造成大量庫存(包括在制品與成品。參見:Continuous Flow(連續(xù)流,Lean Product
溫馨提示
- 1. 本站所有資源如無特殊說明,都需要本地電腦安裝OFFICE2007和PDF閱讀器。圖紙軟件為CAD,CAXA,PROE,UG,SolidWorks等.壓縮文件請下載最新的WinRAR軟件解壓。
- 2. 本站的文檔不包含任何第三方提供的附件圖紙等,如果需要附件,請聯(lián)系上傳者。文件的所有權(quán)益歸上傳用戶所有。
- 3. 本站RAR壓縮包中若帶圖紙,網(wǎng)頁內(nèi)容里面會有圖紙預(yù)覽,若沒有圖紙預(yù)覽就沒有圖紙。
- 4. 未經(jīng)權(quán)益所有人同意不得將文件中的內(nèi)容挪作商業(yè)或盈利用途。
- 5. 人人文庫網(wǎng)僅提供信息存儲空間,僅對用戶上傳內(nèi)容的表現(xiàn)方式做保護處理,對用戶上傳分享的文檔內(nèi)容本身不做任何修改或編輯,并不能對任何下載內(nèi)容負責(zé)。
- 6. 下載文件中如有侵權(quán)或不適當(dāng)內(nèi)容,請與我們聯(lián)系,我們立即糾正。
- 7. 本站不保證下載資源的準確性、安全性和完整性, 同時也不承擔(dān)用戶因使用這些下載資源對自己和他人造成任何形式的傷害或損失。
最新文檔
- 2025年五股東共同投資協(xié)議文本
- 2025年新型可控氣氛爐項目申請報告模稿
- 2025年醫(yī)療行業(yè)信息共享合同樣式
- 2025年創(chuàng)意企業(yè)合作協(xié)議標準文本
- 2025年分期付款合同服務(wù)全方位指南
- 2025年供應(yīng)商與采購商海鮮交易合同
- 2025年酸堿平衡調(diào)節(jié)藥項目規(guī)劃申請報告
- 2025年廢棄土地資源化合同
- 2025年專利申請買賣雙方協(xié)議
- 2025年人才選拔與委托合作協(xié)議標準文本
- 2024年徐州工業(yè)職業(yè)技術(shù)學(xué)院高職單招職業(yè)適應(yīng)性測試歷年參考題庫含答案解析
- 2025年春新人教版語文一年級下冊全冊課件
- 2025年春新北師大版數(shù)學(xué)七年級下冊全冊教案
- 第七章老年人泌尿系統(tǒng)疾病
- 2025年枝江金潤源建設(shè)集團招聘筆試參考題庫含答案解析
- 危險化學(xué)品安全監(jiān)管培訓(xùn)
- 病原生物學(xué)-人體寄生蟲學(xué)知到智慧樹章節(jié)測試課后答案2024年秋浙江大學(xué)
- 校園安全案例解析
- 2024-2030年中國醫(yī)療建筑工程行業(yè)發(fā)展?jié)摿巴顿Y戰(zhàn)略規(guī)劃分析報告
- 人工智能導(dǎo)論知到智慧樹章節(jié)測試課后答案2024年秋天津大學(xué)
- 校史館裝修工程施工方案
評論
0/150
提交評論