


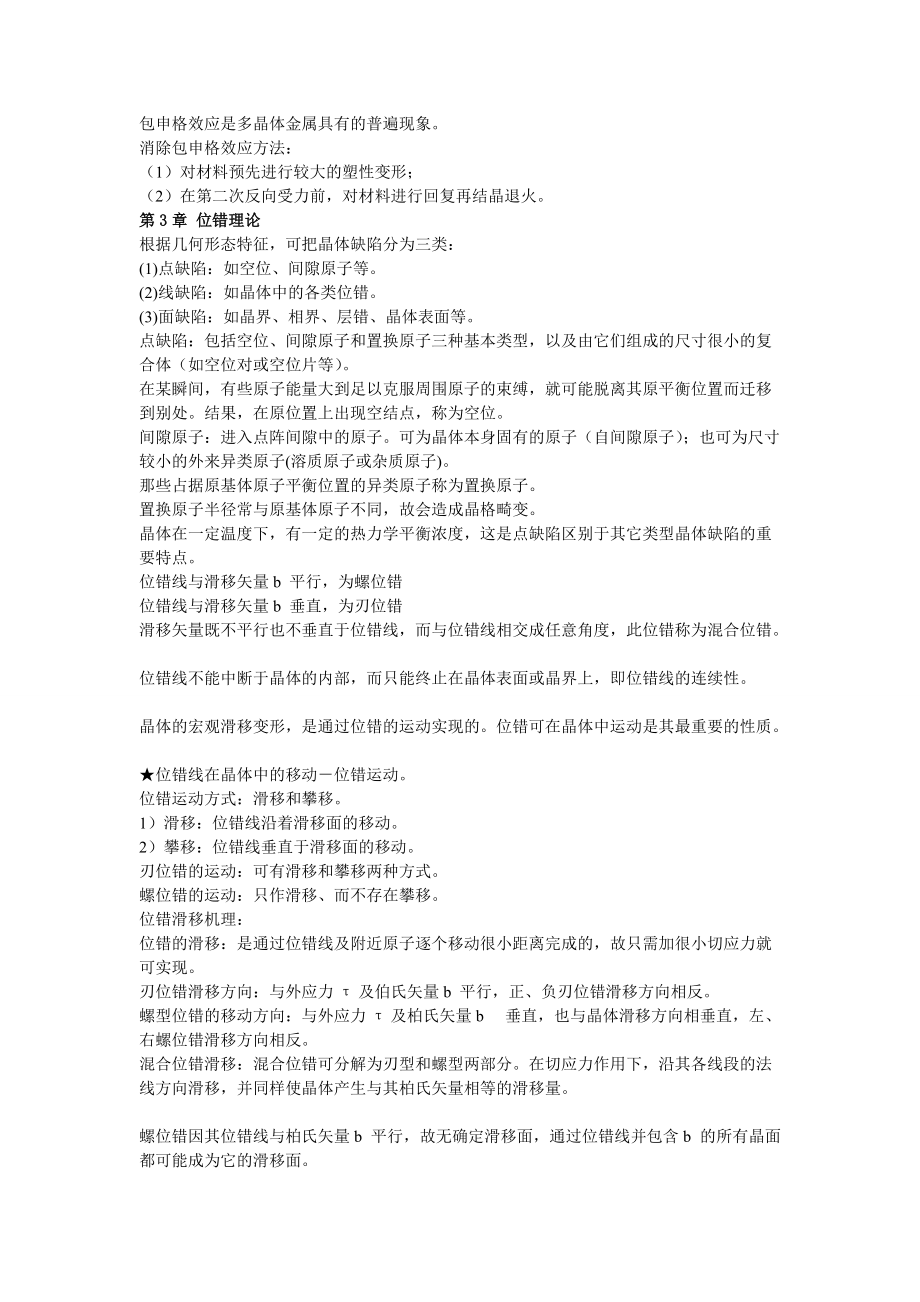

版權(quán)說明:本文檔由用戶提供并上傳,收益歸屬內(nèi)容提供方,若內(nèi)容存在侵權(quán),請進(jìn)行舉報或認(rèn)領(lǐng)
文檔簡介
1、第一章 應(yīng)力應(yīng)變曲線及彈性變形用靜拉伸應(yīng)力應(yīng)變曲線,可得出許多重要性能指標(biāo):1、彈性模量 E :主要用于零件的剛度設(shè)計。2、屈服強(qiáng)度s (ReL)和抗拉強(qiáng)度b (Rm) :主要用于零件的強(qiáng)度設(shè)計。3、抗拉強(qiáng)度b (Rm)和彎曲疲勞強(qiáng)度有一定比例關(guān)系,進(jìn)一步為零件在交變載荷下使用提供參考。4、材料的塑性,斷裂前的應(yīng)變量:主要是為材料在冷熱變形時的工藝性能作參考。工程應(yīng)力應(yīng)變曲線:不能真實反映試件拉伸過程中應(yīng)力和應(yīng)變的變化關(guān)系。實際拉伸中,隨載荷F 增加,長度 L0 伸長,截面積 A0 相應(yīng)減少。真應(yīng)力S真應(yīng)變e 曲線:(流變曲線)真實反映變形過程中,隨應(yīng)變量增大,材料性質(zhì)的變化。真應(yīng)力 S :試
2、件在某一瞬時承受的拉伸應(yīng)力。真應(yīng)變 e :試件瞬時伸長量 / 瞬時長度。真實應(yīng)力總是大于大于工程應(yīng)力,真實應(yīng)變總是小于工程應(yīng)變真應(yīng)力 S 和真應(yīng)變 e 的定義:承認(rèn)了在變形過程中試件長度和直徑間相互變化的事實。即長度L 伸長了,其實際截面積 A 就會相應(yīng)減少第種類型:完全彈性 特點:具有可逆應(yīng)力應(yīng)變曲線和不出現(xiàn)塑性變形的特征。粘彈性:是指材料在外力作用下,彈性和粘性兩種變形機(jī)理同時存在的力學(xué)行為。特征:是應(yīng)變對應(yīng)力的響應(yīng)不是瞬時完成的(應(yīng)變落后于應(yīng)力),需要通過一個弛豫過程,但卸裁后,應(yīng)變恢復(fù)到初始值,不留下殘余變形。第種類型:彈性均勻塑性若材料具有不可逆的塑性變形能力,在彈性變形后,接著有一
3、個均勻變形階段,應(yīng)力-應(yīng)變曲線呈現(xiàn)為第類型。應(yīng)力很小時,仍有彈性變形區(qū),接著一段光滑的拋物線,其相應(yīng)于均勻塑性變形過程。均勻塑性變形:表明塑性變形需要不斷增加外力才能繼續(xù)進(jìn)行,即材料有阻止繼續(xù)塑變的能力(應(yīng)變硬化性能)。第種類型:彈性不均勻塑性變形在正常彈性后,有一系列鋸齒疊加在拋物線型曲線上。此類材料特性:是由于材料內(nèi)部不均勻變形所致。第種類型:彈性不均勻塑性均勻塑性變形許多體心立方鐵基合金和有色合金,應(yīng)力應(yīng)變曲線在彈性與均勻塑性變形間有一狹窄一段屬不均勻塑變區(qū)。即從彈性向塑性變形的過渡明顯。主要表現(xiàn):在試驗中,外力不增加(保持恒定)試樣仍繼續(xù)伸長;ABC或外力增加到一定數(shù)值時突然下降,隨后
4、,在外力不增加或上下波動下,試樣繼續(xù)伸長變形。這便是“屈服現(xiàn)象”。第種類型:彈性不均勻塑性均勻塑性變形其中:OA彈性;有一個上屈服點A,接著載荷下降。 AB不均勻塑變;BC均勻塑變。以B點為界,整個塑性變形出現(xiàn)兩種不同趨勢。AB應(yīng)力隨應(yīng)變增大而下降,BC應(yīng)力隨應(yīng)變增大而上升。到達(dá) B 點后,試件出現(xiàn)“縮頸”,但并很快失效。典型的結(jié)晶高聚合物材料具有此特征,這與其結(jié)構(gòu)有關(guān)。第2章 材料彈性變形彈性變形定義:當(dāng)外力去除后,能恢復(fù)到原形狀或尺寸的變形彈性變形。彈性變形具有可逆性的特點。無論變形量大小、應(yīng)力應(yīng)變是否呈線性關(guān)系,凡彈性形變都是可逆變形。彈性變形本質(zhì):都是構(gòu)成材料的原子(離子)或分子從平衡
5、位置產(chǎn)生可逆位移的反映。雙原子模型解釋彈性變形的微觀過程:1)在無外加載荷下,晶格中原子在其平衡位置僅作微小熱振動,這是受原子間相互作用力控制的結(jié)果。(原子間相互作用力是原子間距的函數(shù)。在原子平衡位置處合力為零。)2)當(dāng)受外力作用時,原子間相互平衡力受到破壞,原子的位置產(chǎn)生位移,達(dá)到新的平衡。原子位移的總和:在宏觀上就表現(xiàn)為變形。3)當(dāng)外力去除后,原子依靠彼此間作用力又回到原來平衡位置,宏觀變形也隨之消失,表現(xiàn)出彈性變形的可逆性。上述模型導(dǎo)出的原子間相互作用力與其彈性位移關(guān)系并非虎克定律所描述的直線關(guān)系,而是拋物線關(guān)系。合力曲線有最大值 Fmax,若外力略大于Fmax ,就意味著可克服原子間引
6、力而使它們分離。Fmax 即為材料在彈性狀態(tài)下的理論斷裂抗力,實際斷裂抗力遠(yuǎn)遠(yuǎn)小于Fmax時,材料就發(fā)生斷裂或產(chǎn)生塑性變形。彈性模量E :在數(shù)值上等于當(dāng)應(yīng)變?yōu)橐粋€單位時的 彈性應(yīng)力。是表征材料對彈性變形的抗力,工程稱材料的剛度.E值越大,在相同應(yīng)力下產(chǎn)生的彈性變形就越小。彈性模數(shù):是構(gòu)成材料原子、離子間鍵合強(qiáng)度的主要標(biāo)志,因此,凡影響鍵合強(qiáng)度的因素均能影響材料的彈性模數(shù)E 。彈性模量 E 與切變模量 G 關(guān)系:其中: 泊松比。泊松比:彈性變形時,試件縱向伸長和橫向縮短保持一定比例關(guān)系。橫向應(yīng)變與縱向應(yīng)變之比的絕對值稱為泊松比 表示材料在受外力作用時側(cè)向收縮能力。比例極限p 是材料彈性變形按正比
7、關(guān)系變化的最大應(yīng)力,即拉伸應(yīng)力一應(yīng)變曲線上開始偏離直線時的應(yīng)力值。彈性極限:材料由彈性變形過渡到彈塑性變形時的應(yīng)力,當(dāng)應(yīng)力超過彈性極限e 后,便開始產(chǎn)生塑性變形。彈性比功:(彈性比能、應(yīng)變比能),用ae 表示,表示材料在彈性變形過程中吸收彈性變形功的能力。用材料開始塑性變形前單位體積吸收的最大彈性變形功表示。物理意義:吸收彈性變形功的能力。彈性可分為:理想彈性(完全彈性)和非理想彈性(彈性不完整性)兩類。理想彈性材料:在外載荷作用下,應(yīng)力-應(yīng)變服從虎克定律,即E,并同時滿足3個條件,即: 應(yīng)變對于應(yīng)力的響應(yīng)是線性的; 應(yīng)力和應(yīng)變同相位; 應(yīng)變是應(yīng)力的單值函數(shù)。純彈性體的彈性變形:只與載荷大小有
8、關(guān),而與加載方向和加載時間無關(guān)。材料的非理想彈性行為:可分為滯彈性、粘彈性、偽彈性及包申格效應(yīng)等幾種類型滯彈性(彈性后效):是指材料在彈性范圍內(nèi)快速加載或卸載后,隨時間的延長而產(chǎn)生的附加彈性應(yīng)變的現(xiàn)象。加載時,應(yīng)變落后于應(yīng)力,而與時間有關(guān)的滯彈性,稱為正彈性后效(或彈性蠕變)卸載時,應(yīng)變落后于應(yīng)力的現(xiàn)象,稱為反彈性后效。在彈性區(qū)內(nèi)單向快速加載、卸載時,加載線與卸載線會不重合(應(yīng)力和應(yīng)變不同步),形成一封閉回線,稱為彈性滯后環(huán)。交變載荷時,若最大應(yīng)力宏觀彈性極限,加載速率比較大,則也得到彈性滯后環(huán)交變載荷時,若最大應(yīng)力宏觀彈性極限,則得到塑性滯后環(huán)材料存在彈性滯后環(huán)的現(xiàn)象說明:材料加載時吸收的變
9、形功 > 卸載時釋放的變形功,有一部分加載變形功被材料所吸收。這部分在變形過程中被吸收的功,稱為材料的內(nèi)耗。內(nèi)耗的大?。嚎捎脺蟓h(huán)面積度量。滯后環(huán)中所包圍的面積:代表應(yīng)力一應(yīng)變循環(huán)一個周期所產(chǎn)生的能量損耗。滯后環(huán)面積越大,能量損耗也越大。循環(huán)韌性:指材料在塑性區(qū)內(nèi)加載時吸收不可逆變形功的能力。內(nèi)耗:指材料在彈性區(qū)內(nèi)加載時吸收不可逆變形功的能力。包申格(Bauschinger)效應(yīng):金屬材料經(jīng)預(yù)加載產(chǎn)生少量塑變 (殘余應(yīng)變約14),卸載后再同向加載,規(guī)定殘余伸長應(yīng)力(彈性極限或屈服強(qiáng)度)增加;反向加載,規(guī)定殘余伸長應(yīng)力降低(特別是彈件極限在反向加載時幾乎降低到零)的現(xiàn)象,稱為包申格效應(yīng)。包
10、申格效應(yīng)是多晶體金屬具有的普遍現(xiàn)象。消除包申格效應(yīng)方法:(1)對材料預(yù)先進(jìn)行較大的塑性變形;(2)在第二次反向受力前,對材料進(jìn)行回復(fù)再結(jié)晶退火。第3章 位錯理論根據(jù)幾何形態(tài)特征,可把晶體缺陷分為三類:(1)點缺陷:如空位、間隙原子等。 (2)線缺陷:如晶體中的各類位錯。(3)面缺陷:如晶界、相界、層錯、晶體表面等。點缺陷:包括空位、間隙原子和置換原子三種基本類型,以及由它們組成的尺寸很小的復(fù)合體(如空位對或空位片等)。在某瞬間,有些原子能量大到足以克服周圍原子的束縛,就可能脫離其原平衡位置而遷移到別處。結(jié)果,在原位置上出現(xiàn)空結(jié)點,稱為空位。間隙原子:進(jìn)入點陣間隙中的原子??蔀榫w本身固有的原子
11、(自間隙原子);也可為尺寸較小的外來異類原子(溶質(zhì)原子或雜質(zhì)原子)。那些占據(jù)原基體原子平衡位置的異類原子稱為置換原子。置換原子半徑常與原基體原子不同,故會造成晶格畸變。晶體在一定溫度下,有一定的熱力學(xué)平衡濃度,這是點缺陷區(qū)別于其它類型晶體缺陷的重要特點。位錯線與滑移矢量b 平行,為螺位錯位錯線與滑移矢量b 垂直,為刃位錯滑移矢量既不平行也不垂直于位錯線,而與位錯線相交成任意角度,此位錯稱為混合位錯。位錯線不能中斷于晶體的內(nèi)部,而只能終止在晶體表面或晶界上,即位錯線的連續(xù)性。晶體的宏觀滑移變形,是通過位錯的運(yùn)動實現(xiàn)的。位錯可在晶體中運(yùn)動是其最重要的性質(zhì)。位錯線在晶體中的移動位錯運(yùn)動。位錯運(yùn)動方式
12、:滑移和攀移。1)滑移:位錯線沿著滑移面的移動。2)攀移:位錯線垂直于滑移面的移動。刃位錯的運(yùn)動:可有滑移和攀移兩種方式。螺位錯的運(yùn)動:只作滑移、而不存在攀移。 位錯滑移機(jī)理:位錯的滑移:是通過位錯線及附近原子逐個移動很小距離完成的,故只需加很小切應(yīng)力就可實現(xiàn)。刃位錯滑移方向:與外應(yīng)力及伯氏矢量b 平行,正、負(fù)刃位錯滑移方向相反。螺型位錯的移動方向:與外應(yīng)力及柏氏矢量b 垂直,也與晶體滑移方向相垂直,左、右螺位錯滑移方向相反?;旌衔诲e滑移:混合位錯可分解為刃型和螺型兩部分。在切應(yīng)力作用下,沿其各線段的法線方向滑移,并同樣使晶體產(chǎn)生與其柏氏矢量相等的滑移量。 螺位錯因其位錯線與柏氏矢量b 平行,
13、故無確定滑移面,通過位錯線并包含b 的所有晶面都可能成為它的滑移面。若螺位錯在某一滑移面滑移后受阻,可轉(zhuǎn)移到與之相交的另一個滑移面上去,此過程叫交叉滑移,簡稱交滑移。只有螺位錯才能交滑移。位錯的攀移:指在熱缺陷或外力作用下,位錯線在垂直其滑移面方向上的運(yùn)動,結(jié)果導(dǎo)致晶體中空位或間隙質(zhì)點的增殖或減少。攀移的實質(zhì):是多余半原子面的伸長或縮短。刃位錯:可在滑移面上滑移,還可在垂直滑移面方向攀移。正攀移:多余半原子面向上移動,向下移動稱負(fù)攀移。螺位錯:沒有多余半原子面,故無攀移。攀移與滑移不同:1)攀移伴隨物質(zhì)的遷移,需要空位的擴(kuò)散,需要熱激話,比滑移需更大能量。2)低溫攀移較困難,高溫時易攀移。在許
14、多高溫過程如蠕變、回復(fù)、單晶拉制中,攀移卻起著重要作用。3)攀移通常會引起體積的變化,故屬非保守運(yùn)動。4)作用于攀移面的正應(yīng)力有助于位錯的攀移。壓應(yīng)力將促進(jìn)正攀移,拉應(yīng)力可促進(jìn)負(fù)攀移。5)晶體中過飽和空位也有利于攀移。 位錯周圍彈性應(yīng)力場的存在增加了晶體的能量,這部分能量稱為位錯的應(yīng)變能。位錯的應(yīng)變能:可根據(jù)造成這個位錯所作的功求得。刃位錯彈性應(yīng)變能比螺位錯彈性應(yīng)變能約大50%混合位錯:位錯線與其柏氏矢量b 成角的,可認(rèn)為由柏氏矢量分別為bsin的刃位錯和bcos的螺位錯。 分別算出兩位錯分量應(yīng)變能,其和即為混合位錯應(yīng)變能。即使在無任何缺陷情況下,位錯運(yùn)動也需克服滑移面兩側(cè)原子間相互作用力(最
15、基本阻力),稱為點陣阻力(派-納力)。滑移面間距 a 值越大,位錯強(qiáng)度b值越小,則派-納力越小,故越容易滑移。晶體中,原子最密排面,間距a 最大,最密排方向,原子間距b最小,故位于密排面上,且柏氏矢量b方向與密排方向一致的位錯最易滑移。晶體滑移面和滑移方向一般為晶體原子密排面與密排方向。因位錯的能量與其長度成正比,因此它有盡量縮短其長度的趨勢。位錯為縮短其長度會產(chǎn)生線張力。以單位長度位錯線的能量來表示。線張力是位錯的一種彈性性質(zhì)。因位錯能量與長度成正比,當(dāng)位錯受力彎曲,位錯線增長,其能量相應(yīng)增高,而線張力則會使位錯線盡量縮短和變直。兩平行螺型位錯相互作用特點:同號相斥,異號相吸。在同一滑移面上
16、,同號刃型位錯總是相互排斥,距離越小,排斥力越大。同號刃位錯在平行滑移面上,將力圖沿與其 b 垂直的方向排列。此位錯組態(tài)稱位錯墻。異號刃位錯力圖排在和滑移面成45°的平面上,且異號刃位錯間相互吸引。 當(dāng)一個純螺型位錯與另一個純?nèi)行臀诲e互相平行時,兩位錯間無相互作用。晶體塑性形變,往往會在一個滑移面上有許多位錯在某種障礙物前被迫堆積,形成位錯群的塞積。晶界易成為位錯運(yùn)動的障礙物,位錯間的相互作用力也可產(chǎn)生障礙。位錯塞積群的重要效應(yīng):使在它前端引起應(yīng)力集中。當(dāng)n 個位錯被切應(yīng)力 推向障礙物時,在塞積群前端將產(chǎn)生n 倍于外力的應(yīng)力集中。晶界前位錯塞積:引起應(yīng)力集中,能使相鄰晶粒屈服;當(dāng)數(shù)量
17、n 足夠大,也可在晶界處引起裂縫,出現(xiàn)微裂紋。位錯在滑移面上運(yùn)動,必與穿過此滑移面上的其它位錯(稱為“位錯林”)相交截,該過程即為“位錯交截”。位錯相互切割后,將使位錯產(chǎn)生彎折,生成位錯折線,這種折線有兩種:1)割階:位錯折線垂直(或不在)其所屬滑移面上。 2)扭折:位錯折線在其所屬滑移面上。柏氏矢量b 相互平行的兩刃位錯的交割:形成扭折。初始狀態(tài)為螺位錯,均在原位錯滑移面上,在原位錯向前運(yùn)動中,都因位錯線伸直而消失,故為扭折(在其滑移面上)。柏氏矢量b 相互垂直的兩刃位錯交割,不位于滑移面上的位錯臺階成為割階,產(chǎn)生割價需供給能量,故交割過程對位錯運(yùn)動是一種阻礙。1)運(yùn)動位錯交割后,各位錯線都
18、可產(chǎn)生一扭折或割階,其大小和方向取決于另一位錯的柏氏矢量。2)所有割階都是刃位錯,而扭折可刃型、也可螺型。3)扭折:與原位錯線在同一滑移面上,可隨主位錯線一道運(yùn)動,幾乎不產(chǎn)生阻力,且扭折在線張力下易于消失。4)割階:則與原位錯線不在同一滑移面上,除非割階產(chǎn)生攀移,否則,割階就不能隨主位錯線一道運(yùn)動,成為位錯運(yùn)動的障礙,常稱此為割階硬化。帶割階位錯的運(yùn)動,按割階高度不同,又可分為三種情況:1) 割階高度只有12個原子間距,若外力足夠大,螺位錯可把割階拖著走,在割階后留下一排點缺陷。2) 割階高度很大,約在20nm以上,此時割階兩端位錯相隔太遠(yuǎn),相互間作用小,均可獨立在各自滑移面上滑移,并以割階為
19、軸,在滑移面上旋轉(zhuǎn)。3) 割階高度在上述兩種之間,位錯不能拖著割階運(yùn)動。在外力作用下,割階間位錯線彎曲,位錯前進(jìn)就會在其身后留下一對拉長了的異號刃位錯線段(位錯偶)。為降低應(yīng)變能,此位錯偶常會斷開而留下一個長位錯環(huán),而位錯線仍回復(fù)原來帶割階的狀態(tài),而長的位錯環(huán)又常會再進(jìn)一步分裂成小的位錯環(huán),這是形成位錯環(huán)的機(jī)理之一。能使位錯增值的地方稱為位錯源。弗蘭克-瑞德(Frank-Rend)源:(a)設(shè)晶體中某滑移面上有一段刃型位錯AB,其兩端被位錯網(wǎng)節(jié)點釘住。(b)當(dāng)外切應(yīng)力滿足條件時,位錯DD'受力作用發(fā)生滑移。位錯線本應(yīng)平行向前滑移,但因其兩端被固定住,勢必發(fā)生彎曲,位錯變成曲線形狀。(c
20、)位錯受力總是與位錯線垂直,即使位錯彎曲也如此,在應(yīng)力作用下,位錯每一線段都沿其法線向外運(yùn)動,(d)當(dāng)位錯向前走出一段距離,到p、q兩點就碰到一起了。(e)因p、q為·一對左、右旋螺位錯,相遇便互相抵消,則原位錯線被分成兩部分。(f)外面位錯環(huán):在力作用下不斷擴(kuò)大,直到晶體表面,而內(nèi)部另一段位錯:在線張力和外力作用下回到原狀態(tài)。上述F-R源,實質(zhì)上是一段兩端被釘扎的可滑動位錯,所以稱之為雙邊(或雙軸) F-R源,又稱為U型平面源。雙交滑移增殖機(jī)制:螺位錯由原滑移面轉(zhuǎn)至相交的滑移面,后又轉(zhuǎn)到與原始滑移面平行的滑移面上的運(yùn)動,稱為雙交滑移運(yùn)動。雙交滑移是一種更有效的增殖機(jī)制。 位錯反應(yīng)(
21、dislocation reaction)位錯在一定條件下發(fā)生分解或合并的過程。已知,位錯的能量與其伯格斯(Burgers)矢量(簡稱伯氏矢量)的平方成比例。因此具有高能量的位錯,無論在力學(xué)上或者熱力學(xué)上都是不穩(wěn)定的,在一定的條件下,將自動地分解為兩個或更多的伯氏矢量較小的位錯,以不斷地降低其本身的能量。同樣,兩個或兩個以上的位錯,也可以合并成一個位錯。這種反應(yīng)不是任意的,它必須滿足一定的條件。例如,全位錯分解為兩個不全位錯的充分和必要的條件是:(1)幾何條件。反應(yīng)前位錯的伯氏矢量b和反應(yīng)后諸位錯的伯氏矢量b之和應(yīng)相等,即b=b(2)能量條件。按熱力學(xué)的一般要求,作為一個自動進(jìn)行的位錯反應(yīng)過程
22、,必須是一個伴隨著能量降低的過程,即要求反應(yīng)之后整個系統(tǒng)的能量低于反應(yīng)前整個系統(tǒng)的能量。一個位錯反應(yīng)能否進(jìn)行的能量判據(jù)是b2 >b2。第4章 塑性變形單晶體受力后,外力在任何晶面上都可分解為正應(yīng)力和切應(yīng)力。正應(yīng)力:只能引起彈性變形及解理斷裂。只有在切應(yīng)力的作用下,金屬晶體才能產(chǎn)生塑性變形。金屬材料常見的塑性變形方式:滑移和孿生兩種滑移:指晶體的一部分沿一定的晶面(滑移面)和晶向(滑移方向)相對于另一部分發(fā)生滑動的現(xiàn)象。滑移面:面間距最大原子最密排晶面?;品较颍涸幼蠲芘诺姆较?。一個滑移面與其上的一個滑移方向組成一個滑移系。1) 面心立方(fcc)金屬:滑移面為111,共有 4 組;滑移
23、方向為<110>,每個滑移面上包含 3 個滑移方向。共有4×3=12個滑移系2)體心立方(bcc)金屬:滑移面:為110晶面族,共有 6 個面;滑移方向:為<111>晶向族(立方體對角線);每個滑移面上有2個滑移方向,共有6×2=12個滑移系。bcc金屬的滑移系:除110晶面族外,也可為112和123晶面族,此三種滑移面及其共同的滑移方向<111>的組合,總共有48個可能的滑移系。bcc金屬滑移系雖較多(為fcc 4 倍多),但其滑移面原子密排程度不如 fcc ,滑移方向數(shù)目也較少,故其塑性不如fcc金屬好。此外,fcc晶體派-納力要低的
24、多,從而其內(nèi)位錯較易滑移。3) 密排六方(hcp)金屬:情況較為復(fù)雜 通常,只有一個滑移面(0001)和三個滑移方向,共有1×3 = 3個滑移系,密排六方金屬滑移系少,滑移過程中,可能采取的空間位向少,故塑性差?;浦荒茉谇袘?yīng)力的作用下發(fā)生。產(chǎn)生滑移的最小切應(yīng)力稱臨界切應(yīng)力。滑移常沿晶體中原子密度最大的晶面和晶向發(fā)生。因原子密度最大的晶面和晶向之間原子間距最大,結(jié)合力最弱,產(chǎn)生滑移所需切應(yīng)力最小?;茣r,晶體兩部分的相對位移量是原子間距的整數(shù)倍?;平Y(jié)果在晶體表面形成臺階,稱滑移線,若干條滑移線組成一個滑移帶當(dāng)滑移面、滑移方向與外力都呈45°角時(= 45°),滑
25、移方向上分切應(yīng)力最大(軟位向),最容易發(fā)生滑移?;频耐瑫r伴隨著晶體的轉(zhuǎn)動轉(zhuǎn)動原因:晶體滑移后使正應(yīng)力和切應(yīng)力分量組成了力偶。轉(zhuǎn)動結(jié)果:使滑移面法線與外力軸夾角增大,使外力與滑移方向夾角變小。實際上,滑移是通過滑移面上位錯的運(yùn)動來實現(xiàn)的。當(dāng)位錯移動到晶體表面時,便產(chǎn)生大小為 b 的滑移臺階,若有大量位錯沿滑移面上運(yùn)動到表面,宏觀上,晶體的一部分相對另一部份沿滑移面發(fā)生了相對位移,這便是滑移。單滑移:對有多組滑移系的晶體,當(dāng)其與外力軸取向不同時,處于軟位向的一組滑移系首先開動,這便是單滑移。多滑移:若兩組或幾組滑移系處在同等有利的位向,在滑移時,各滑移系同時開動,或因滑移中晶體的轉(zhuǎn)動使兩個或多個
26、滑移系交替滑移稱為多滑移。若發(fā)生雙滑移或多系滑移,在表面上所見到的滑移線就不再是一組平行線,會出現(xiàn)二組或多組的交叉形的滑移帶。交滑移:是指兩個或多個滑移面沿同一個滑移方向滑移。交滑移實質(zhì):是螺位錯在不改變滑移方向的情況下,從一個滑移面滑到交線處,轉(zhuǎn)到另一個滑移面的過程。交滑移:表面滑移線是彎曲的折線,而不再是平直的。金屬晶體在發(fā)生滑移時,1)單滑移:金屬晶體先發(fā)生單滑移,因只有一個滑移系起作用,加工硬化效果很小。2)多滑移:隨著晶體發(fā)生轉(zhuǎn)動,會使數(shù)個滑移系同時處于有利位向,而發(fā)生多滑移,這時因不同滑移系間的位錯相互交割,加工硬化效果上升。3)交滑移:隨后又可能轉(zhuǎn)變?yōu)榻换?,這時加工硬化效果下降
27、,在表面出現(xiàn)曲折或波紋狀的滑移帶。 滑移的表面痕跡 :單滑移:單一方向的滑移帶;多滑移:相互交叉的滑移帶;交滑移:波紋狀的滑移帶。孿生:在切應(yīng)力作用下,晶體的一部分沿一定晶面和晶向相對于另一部分所發(fā)生的均勻切變。孿生變形:發(fā)生切變的部分稱孿生帶或?qū)\晶,均勻切變區(qū)與未切變區(qū)的分界面稱為孿晶界。發(fā)生均勻切變的那組晶面稱為孿晶面;孿生面的移動方向稱為孿生方向。孿生使晶體變形與未變形部分以孿晶面為界構(gòu)成了鏡面對稱關(guān)系。1孿生也是在切應(yīng)力作用下發(fā)生的,常出現(xiàn)于滑移受阻而引起的應(yīng)力集中區(qū),其臨界分切應(yīng)力要比滑移大得多。孿生變形速度極快, 接近聲速。2孿生使一部分晶體發(fā)生均勻切變,而滑移只集中在一些滑移面上
28、進(jìn)行(不均勻變形)。3孿生使晶體變形部分位向發(fā)生改變,孿晶面兩側(cè)晶體位向呈鏡面對稱,而滑移后晶體各部分位向均未改變。4孿生時相鄰原子面的相對位移量小于一個原子間距5孿生對塑變的直接貢獻(xiàn)比滑移小很多6孿生變形的拉伸應(yīng)力-應(yīng)變曲線呈鋸齒狀。光滑階段是與滑移塑變對應(yīng);鋸齒狀階段即孿生變形所致。孿晶形核所需應(yīng)力遠(yuǎn)高于擴(kuò)展所需要應(yīng)力,故孿晶形成后載荷就會急劇下降。7孿生變形與晶體結(jié)構(gòu):一些密排六方金屬(如Cd,Zn,Mg 等)常發(fā)生孿生變形。體心及面心立方金屬:在形變溫度很低,形變速率極快時,也會通過孿生方式進(jìn)行塑變。在面心立方金屬中常發(fā)現(xiàn)有孿晶,這是因相變過程中原子重新排列時發(fā)生錯排而產(chǎn)生的,稱退火孿
29、晶。8孿生使表面出現(xiàn)浮凸,因?qū)\晶與基體的取向不同,表面重新拋光后并浸蝕后仍能看到。多晶雙晶在室溫下拉伸變形后,呈現(xiàn)竹節(jié)狀。晶界處晶體變形較小,而晶內(nèi)變形量則大得多,整個晶粒的變形不均勻。這表明:晶界強(qiáng)度高于晶內(nèi)。晶界對塑性變形的影響:晶體在外力作用下變形,當(dāng)滑移的位錯運(yùn)動到晶界附近時,受到阻礙而堆積,稱位錯塞積。要使變形繼續(xù)進(jìn)行, 須增加外力, 而使金屬變形抗力提高。各晶粒變形不同時性:當(dāng)多晶體受外力作用時,因各晶粒取向不同,軟取向晶粒先滑移變形,而硬取向晶??赡苋蕴幱趶椥宰冃螤顟B(tài)。只有外力繼續(xù)增大,才能使滑移從某些晶粒傳播到相鄰晶粒,并不斷傳播下去,從而產(chǎn)生宏觀可見的塑性變形。各晶粒的變形不
30、均勻:多晶體各晶粒變形不同時性,也反映了各晶粒變形不均勻。變形不均勻性:不僅存在于各晶粒間、基體與第二相間,也存在于同一晶粒內(nèi)部。因晶界對滑移的阻礙作用,使得靠近晶界區(qū)域的滑移變形量明顯小于晶粒中心區(qū)域。晶粒大小對塑性變形(強(qiáng)度)的影響:實驗表明:多晶體的強(qiáng)度隨其晶粒的細(xì)化而增加。晶粒越細(xì),單位體積所包含晶界越多,位錯障礙越多,需要協(xié)調(diào)的不同位向的晶粒越多,使金屬塑性變形的抗力越高。晶粒大小對金屬的塑性和韌性的影響。因晶粒越細(xì),單位體積內(nèi)晶粒數(shù)及參與變形晶粒數(shù)目越多,變形越均勻,斷裂前塑性變形越大,塑性越好。強(qiáng)度和塑性均增加, 斷裂前消耗功也大,故韌性也越高細(xì)晶化是唯一的在增加材料強(qiáng)度的同時也
31、增加材料塑性的強(qiáng)化方式。通過細(xì)化晶粒來同時提高金屬的強(qiáng)度、塑性和韌性的方法稱細(xì)晶強(qiáng)韌化。 細(xì)晶強(qiáng)化前提條件:是晶界阻礙位錯滑移,這在溫度較低的情況下是存在的。晶界本質(zhì)是缺陷,當(dāng)溫度升高時,隨原子活動加強(qiáng),晶界也變得不穩(wěn)定,其強(qiáng)化效果減弱,甚至出現(xiàn)晶界弱化現(xiàn)象。屈服現(xiàn)象:金屬材料在拉伸時,當(dāng)應(yīng)力超過彈性極限,即使外力不再增加,甚至下降情況下,而變形繼續(xù)進(jìn)行的現(xiàn)象,稱為屈服。在屈服伸長變形是不均勻的,當(dāng)應(yīng)力達(dá)到上屈服點下降到下屈服點時,在試樣局部開始塑性變形,表面形成與拉伸軸成45°的應(yīng)變痕跡,稱為呂德斯(Lüders)帶。若將低碳鋼經(jīng)少量預(yù)變形,去載后立即加載,則暫不出現(xiàn)屈服
32、現(xiàn)象。但若預(yù)變形后,將試樣放置一段時間或稍微加熱(200)后再加載拉伸,則又出現(xiàn)屈服現(xiàn)象,且屈服強(qiáng)度會有所提高,這即應(yīng)變時效現(xiàn)象。屈服強(qiáng)度的提升:位錯強(qiáng)化、細(xì)晶強(qiáng)化、彌散強(qiáng)化、固溶強(qiáng)化位錯間交互產(chǎn)生阻力包括:a)平行位錯間交互作用產(chǎn)生的阻力;b)運(yùn)動位錯與林位錯交互作用產(chǎn)生的阻力。位錯密度增加,也增加,屈服強(qiáng)度也提高劇烈冷變形位錯密度增加4-5個數(shù)量級-形變強(qiáng)化單相固溶體合金中隨溶質(zhì)含量增加,固溶體強(qiáng)度、硬度提高,塑性、韌性下降,稱固溶強(qiáng)化。當(dāng)?shù)诙嘣诰?nèi)呈顆粒狀彌散分布時,顆粒越細(xì),分布越均勻,合金的強(qiáng)度、硬度越高,塑性、韌性略有下降,這種強(qiáng)化方法稱彌散強(qiáng)化。晶粒越細(xì),單位體積所包含晶界越多
33、,位錯障礙越多,需要協(xié)調(diào)的不同位向的晶粒越多,使金屬塑性變形的抗力越高,通過細(xì)化晶粒來同時提高金屬的強(qiáng)度、塑性和韌性的方法稱細(xì)晶強(qiáng)韌化。 第5章 材料的斷裂金屬的斷裂機(jī)件的三種主要失效形式:磨損、腐蝕、斷裂。斷裂:又可分為完全斷裂和不完全斷裂。完全斷裂:在應(yīng)力(或兼有熱或介質(zhì))作用下,金屬材料被分成兩個或幾個部分。不完全斷裂:只是內(nèi)部存在裂紋。光滑拉伸試樣斷面收縮率 <5%為脆斷;> 5%為韌斷。韌性與脆性隨條件改變,韌性與脆性行為也將隨之變化。1)韌性斷裂:材料斷裂前及斷裂過程中產(chǎn)生明顯宏觀塑性變形的斷裂。特點:1)斷裂有一個緩慢撕裂過程,且消耗大量塑性變形能。 2)斷裂面一般平
34、行于最大切應(yīng)力并與主應(yīng)力成45°角。 3)斷口呈纖維狀,灰暗色。 4)典型宏觀斷口特征呈杯錐狀。杯錐狀斷口:有纖維區(qū)、放射區(qū)、剪切唇(斷口三要素)。影響這三個區(qū)比例的主要因素是材料強(qiáng)度和試驗溫度。一般地,材料強(qiáng)度提高,塑性降低,則放射區(qū)增大;1)纖維區(qū):拉伸斷口的裂紋源區(qū),裂紋擴(kuò)展速率很慢,當(dāng)裂紋達(dá)到臨界尺寸后就快速擴(kuò)展面形成放射區(qū)。2)放射區(qū):裂紋快速、低能撕裂形成,有放射線花樣特征。放射線平行于裂紋擴(kuò)展方向,并收斂于裂紋源。撕裂時塑性變形量越大,則放射線越粗。3)剪切唇:拉伸斷裂的最后階段形成錐杯狀的剪切唇剪切唇表面光滑,與拉伸軸呈45度,是典型的切斷型斷裂2)脆性斷裂:材料斷裂
35、前基本無明顯宏觀塑性變形,無明顯預(yù)兆,表現(xiàn)為突然發(fā)生的快速斷裂,故危險性很大。特點:脆性斷裂斷裂面一般與正應(yīng)力垂直,斷口平齊而光亮,常呈放射狀或結(jié)晶狀。放射狀條紋的收斂于裂紋源。矩形截面板狀試樣脆性斷口:可見“人字紋花樣”。人字紋尖頂指向裂紋源。(二)穿晶斷裂與沿晶斷裂:穿晶斷裂:裂紋穿過晶內(nèi),可韌性斷裂、也可脆性斷裂。沿晶斷裂:裂紋沿晶界擴(kuò)展,多為脆斷,斷口呈冰糖狀。沿晶斷裂原因:晶界上一薄層連續(xù)或斷續(xù)脆性第二相、夾雜物,破壞了晶界的連續(xù)性;或雜質(zhì)元素向晶界偏聚等引起。沿晶斷口形貌:當(dāng)晶粒粗大時呈冰糖狀;當(dāng)晶粒細(xì)小時,斷口呈細(xì)小顆粒狀,斷口顏色較灰暗。(三)正斷與切斷(按斷裂面取向或作用力方
36、式)正斷:斷裂面垂直于最大正應(yīng)力max ;切斷:沿最大切應(yīng)力max 方向斷開、與正應(yīng)力約呈450。(四)純剪切與微孔聚集型斷裂、解理斷裂:1)剪切斷裂:金屬材料在切應(yīng)力作用下,沿滑移面滑移分離而造成斷裂。分為純剪切斷裂和微孔聚集型斷裂。純剪切斷裂:(滑斷)完全由滑移流變造成斷裂,某些純金屬尤其是單晶體金屬可產(chǎn)生。斷口呈鋒利的楔形(單晶體)或刀尖型(多晶體)。2)微孔聚集型斷裂:(純剪切斷裂另一種形式)通過微孔形核、長大聚合而導(dǎo)致材料分離,是韌性斷裂的普遍方式。宏觀斷口:常呈現(xiàn)暗灰色、纖維狀,微觀斷口特征:則是斷口上分布大量“韌窩”。(1)微孔形核和長大微孔聚集斷裂過程:微孔成核、長大、聚合、斷
37、裂。微孔成核:大多通過第二相或夾雜物質(zhì)點破裂,或第二相或夾雜物與基體界面脫離。是在斷裂前塑性變形到一定程度時產(chǎn)生的。第二相質(zhì)點處微孔成核原因:位錯引起的應(yīng)力集中;在高應(yīng)變條件下,第二相與基體塑性變形不協(xié)調(diào)而產(chǎn)生分離(2)微孔成核的位錯模型:位錯在外加應(yīng)力作用下運(yùn)動遇到第二相,將繞過形成位錯環(huán),并在第二相質(zhì)點處堆積。位錯環(huán)移向質(zhì)點與基體界面,即沿滑移面分離而成微孔。微孔成核,后面位錯所受排斥力下降,陸續(xù)被推向微孔,并使位錯源重新被激活,不斷放出新位錯,連續(xù)進(jìn)入微孔,使微孔長大。位錯也可在多個滑移面上運(yùn)動,堆積而形成微孔,并借位錯不斷向微孔運(yùn)動而長大。微孔長大同時,相鄰微孔間基體橫截面積減小,產(chǎn)生
38、縮頸(內(nèi)縮頸)而斷裂,微孔連接(聚合)形成微裂紋。裂紋不斷擴(kuò)展,直至最終斷裂。微孔聚集韌性斷裂裂紋形成所需拉應(yīng)力:與第二相質(zhì)點尺寸d 的平方根呈反比關(guān)系。抗拉強(qiáng)度新概念:相當(dāng)于微孔開始形成時的應(yīng)力。韌窩形狀:有等軸韌窩、拉長韌窩和撕裂韌窩,因應(yīng)力狀態(tài)不同而異。1)等軸韌窩:微孔在垂直于正應(yīng)力的平面上各方向長大傾向相同。2)拉長韌窩:在扭轉(zhuǎn)載荷或雙向不等拉伸條件下,因切應(yīng)力作用而形成。在匹配斷口上韌窩拉長方向相反;(如拉伸斷口剪切唇部)3) 撕裂韌窩:在拉、彎應(yīng)力作用下,微孔在拉長、長大時同時被彎曲,形成兩匹配斷口上方向相同的撕裂韌窩。(三點彎曲、沖擊)韌窩的大小(直徑和深度)決定于:1)第二相
39、質(zhì)點的大小和密度。第二相密度增大或其間距減小,則韌窩尺寸減小。2)基體材料塑變能力和應(yīng)變硬化指數(shù)。應(yīng)變硬化指數(shù)越大,越難于發(fā)生內(nèi)縮頸,故韌窩尺寸變小。3)外加應(yīng)力的大小和狀態(tài)。通過影響材料塑性變形能力,而間接影響韌窩深度。微孔聚集斷裂一定有韌窩存在,但微觀上出現(xiàn)韌窩,其宏觀上不一定就是韌性斷裂。因脆性斷裂在局部區(qū)域內(nèi)也能有塑性變形,也存在韌窩。只有微觀斷口存在大量韌窩時,宏觀上才表現(xiàn)為韌性斷裂。 3)解理斷裂:金屬材料在一定條件(如低溫、高應(yīng)變速率,或有三向拉應(yīng)力狀態(tài))下,當(dāng)外加正應(yīng)力達(dá)到一定數(shù)值后,以極快速率沿一定晶體學(xué)平面(解理面)產(chǎn)生的穿晶斷裂。解理常見于:體心立方(bcc)和密排六方(
40、hcp)金屬中。解理面:一般是低指數(shù)面或表面能最低的晶面。一)解理裂紋的形成和擴(kuò)展:在滑移面上切應(yīng)力作用下,刃位錯互相靠近,當(dāng)切應(yīng)力達(dá)到某一臨界值時,塞積處的位錯互相擠緊、聚合而成為高nb、長為 r 的楔形裂紋(或空洞形位錯)。若塞積處應(yīng)力集中不能為塑性變形所松弛,則塞積處最大拉應(yīng)力fmax能達(dá)到理論斷裂強(qiáng)度m,而形成裂紋。以上所述解理裂紋形成,但并不意味會迅速擴(kuò)展而斷裂。解理斷裂過程三階段:1) 塑性變形形成裂紋;2)裂紋在同一晶粒內(nèi)長大,3)裂紋越過晶界向相鄰晶粒擴(kuò)展。1)位錯塞積理論晶粒大小對斷裂應(yīng)力影響已為許多試驗結(jié)果所證實。細(xì)化晶粒(d 越小),斷裂應(yīng)力提高,材料脆性降低。當(dāng)晶粒尺寸
41、d 小于某臨界值時,屈服應(yīng)力低于斷裂應(yīng)力,先屈服后產(chǎn)生斷裂;但當(dāng)d 大于臨界值時,先發(fā)生脆性斷裂。裂紋成核:位錯反應(yīng)形成不動位錯位錯群塞積產(chǎn)生裂紋在bcc晶體中,有兩相交滑移面(10-1)和(101),與解理面(001)相交,三面之交線為010。則(10-1)面上刃位錯b1和沿(101)面的刃位錯b2,于010軸相遇,并產(chǎn)生下列反應(yīng):新形成位錯在(001)面上,而不在bcc晶體固有滑移面族110,故為不動位錯。結(jié)果兩相交滑移面上的位錯群就在該不動位錯附近產(chǎn)生塞積。當(dāng)塞積位錯較多時,產(chǎn)生裂紋nb。何垂耳位錯反應(yīng)理論是降低能量過程,故裂紋成核是自動進(jìn)行的。位錯反應(yīng)形成解理裂紋擴(kuò)展力學(xué)條件:與位錯塞
42、積形成裂紋相同。即:上述位錯塞積和位錯反應(yīng)兩種解理裂紋形成模型的共同點:1)裂紋形核前均需有塑性變形;2)位借運(yùn)動受阻,在一定條件下便會形成裂紋。實驗證實:裂紋常在晶界、亞晶界、孿晶交叉處出現(xiàn)。通過孿生形成解理裂紋只有在晶粒較大時才產(chǎn)生 (二)解理斷裂的微觀斷口特征1、 解理斷裂:基本微觀特征:解理臺階、河流花樣、舌狀花樣。解理斷裂:是沿晶體特定界面發(fā)生的脆性穿晶斷裂。微觀斷口:由許多大致相當(dāng)于晶粒大小的解理(刻)面集合而成的。1) 解理臺階和河流花樣:在解理刻面內(nèi)部,解理裂紋一般要跨越若干相互平行且位于不同高度的解理面,而出現(xiàn)解理臺階和河流花樣。河流花樣:實際上是解理臺階的一種標(biāo)志。解理臺階
43、、河流花樣、舌狀花樣是解理斷裂基本微觀特征。解理臺階形成方式(1)解理裂紋與螺型位錯相交:當(dāng)解理裂紋(設(shè)想為一刃位錯)與晶體內(nèi)一螺位錯CD相遇時,便形成一個高度為b 的臺階。臺階向前滑動而相互匯合,同號臺階相互匯合長大。當(dāng)匯合臺階高度足夠大時,便成為河流花樣。(2) 由解理裂紋與次生解理 (二次解理)或撕裂形成。河流花樣:是判斷是否為解理斷裂的重要微觀依據(jù)。“河流”的流向:與裂紋擴(kuò)展方向一致,根據(jù)“河流”流向確定在微觀范圍內(nèi)解理裂紋擴(kuò)展方向;而按“河流”反方向去尋找斷裂源。2)舌狀花樣解理斷裂的另一微觀特征。舌狀花樣:因在電鏡下類似于“人舌”而得名。它是因解理裂紋沿孿晶界擴(kuò)展留下的舌頭狀凹坑或
44、凸臺。在匹配斷口上“舌頭”為黑白對應(yīng)的。2、準(zhǔn)解理斷裂:因彌散細(xì)小碳化物質(zhì)點影響了裂紋形成與擴(kuò)展,當(dāng)裂紋在晶粒內(nèi)擴(kuò)展時,難于嚴(yán)格沿一定晶體學(xué)平面擴(kuò)展。斷裂路徑:不再與晶粒位向有關(guān),而主要與細(xì)小碳化物有關(guān)。微觀特征:似解理河流但又非真正解理,故稱準(zhǔn)解理。準(zhǔn)解理與解理的共同點:都是穿晶斷裂,有小解理刻面;臺階或撕裂棱及河流花樣。不同點:準(zhǔn)解理小刻面非晶體學(xué)特征。裂紋常源于晶內(nèi)硬質(zhì)點,形成從晶內(nèi)某點發(fā)源的放射狀河流花樣。而解理裂紋常源于晶界,準(zhǔn)解理:不是一種獨立的斷裂機(jī)理,而是解理斷裂的變種。二、斷裂強(qiáng)度的裂紋理論(格雷菲斯裂紋理論)實際材料中已存在裂紋,當(dāng)平均應(yīng)力還很低時,局部應(yīng)力集中可達(dá)到很高值
45、m,從而使裂紋快速擴(kuò)展并導(dǎo)致脆斷。能量平衡原理指出:由于存在裂紋,系統(tǒng)彈性能降低,勢必與因存在裂紋而增加的表面能相平衡。若彈性能降低足以滿足表面能增加之需要時,裂紋就會失穩(wěn)擴(kuò)展,引起脆性破壞。系統(tǒng)總能量變化及各項能量均與裂紋半長 a 有關(guān)。脆斷判據(jù)-1:可得裂紋失穩(wěn)擴(kuò)展的臨界應(yīng)力為:當(dāng)外加應(yīng)力c 時,裂紋就失穩(wěn)擴(kuò)展。脆斷判據(jù)-2:當(dāng)外加應(yīng)力不變,裂紋在服役時不斷擴(kuò)展長大,則當(dāng)長到臨界尺寸(aac) 時,就失穩(wěn)擴(kuò)展。ac為在一定應(yīng)力水平下的裂紋失穩(wěn)擴(kuò)展臨界尺寸。格雷菲斯裂紋具有臨界尺寸ac的裂紋。格雷菲斯理論:由熱力學(xué)原理得出斷裂發(fā)生的必要條件,但這并不意味著事實上一定要斷裂。裂紋自動擴(kuò)展的充分
46、條件是:裂紋尖端應(yīng)力要等于或大于理論斷裂強(qiáng)度m 。滿足了格雷菲斯能量條件,同時也就滿足了應(yīng)力判據(jù)規(guī)定的充分條件。格雷菲斯公式:只適用于脆性固體,如玻璃、金剛石、超高強(qiáng)度鋼等,即那些裂紋尖端無塑性變形情況。第6章 疲勞斷裂1、變動載荷變動載荷:是引起疲勞破壞的外力,其載荷大小或方向均隨時間變化,其單位面積上平均值稱變動應(yīng)力。變動應(yīng)力類型:規(guī)則周期變動應(yīng)力(也稱循環(huán)應(yīng)力)和無規(guī)則隨機(jī)變動應(yīng)力兩種??捎脩?yīng)力時間曲線表示。2、循環(huán)應(yīng)力:波形有正弦波、矩形波和三角形波等,常見者為正弦波。可用下列幾個參量來表示:最大應(yīng)力:max、最小應(yīng)力:min;平均應(yīng)力m ;應(yīng)力幅a ;應(yīng)力比r 金屬機(jī)件或構(gòu)件在變動應(yīng)
47、力和應(yīng)變長期作用下由于累積損傷而引起的斷裂現(xiàn)象稱為疲勞。1、疲勞的分類疲勞分類:1)按應(yīng)力狀態(tài):彎曲疲勞、扭轉(zhuǎn)疲勞、拉壓疲勞及復(fù)合疲勞;2)按環(huán)境和接觸:大氣疲勞、腐蝕疲勞、高溫疲勞、熱疲勞、接觸疲勞等;3)按斷裂壽命和應(yīng)力高低:高周疲勞和低周疲勞,這是最基本的分類方法。高周疲勞:斷裂應(yīng)力水平較低,s ,斷裂壽命較長,Nf 105周次。也稱低應(yīng)力疲勞,一般疲勞多屬這類。低周疲勞:斷裂應(yīng)力水平較高,s,斷裂壽命較短,Nf (102105)用次,往往有塑性應(yīng)變,也稱高應(yīng)力疲勞或應(yīng)變疲勞。斷裂壽命隨應(yīng)力不同而變化:應(yīng)力高壽命短,應(yīng)力低壽命長。當(dāng)應(yīng)力低于某臨界值(疲勞極限)時,壽命可無限長。(2)疲勞
48、是脆性斷裂疲勞應(yīng)力比屈服強(qiáng)度低,故不論韌性材料還是脆性材料,在疲勞斷裂前均不會發(fā)生塑性變形及有形變預(yù)兆,它是在長期累積損傷過程中,經(jīng)裂紋萌生和緩慢亞穩(wěn)擴(kuò)展到臨界尺寸ac 時才突然發(fā)生的。(3)疲勞對缺陷(缺口、裂紋及組織缺陷)十分敏感 疲勞破壞是從局部開始的,故對缺陷具有高度的選擇性。缺口和裂紋因應(yīng)力集中,增大對材料的損傷作用,組織缺陷(夾雜、疏松、白點、脫碳等)降低材料的局部強(qiáng)度,都加快疲勞破壞的產(chǎn)生和發(fā)展。 3、 疲勞宏觀斷口特征疲勞斷口:保留了斷裂過程的很多信息,有明顯形貌特征。并受材料性質(zhì)、應(yīng)力狀態(tài)、大小及環(huán)境等因素的影響,疲勞斷口分析是研究疲勞斷裂過程和原因的重要方法之一。典型疲勞斷
49、口:有三個不同區(qū)域疲勞源、疲勞區(qū)及瞬斷區(qū)(1) 疲勞源: 是疲勞裂紋萌生的策源地。一般在機(jī)件表面,表面缺口、裂紋、刀痕、蝕坑等缺陷等,常因應(yīng)力集中,而引發(fā)的疲勞裂紋。材料內(nèi)部存在嚴(yán)重冶金缺陷(夾雜、縮孔、偏析、白點等)時,因局部強(qiáng)度降低,也會產(chǎn)生疲勞源。疲勞源區(qū)的最為光亮;(2)疲勞區(qū):疲勞裂紋亞穩(wěn)擴(kuò)展區(qū),是判斷疲勞斷裂的重要證據(jù)。宏觀特征:斷口較光滑,并有貝紋線(或海灘花樣)。(3) 瞬斷區(qū):裂紋最后失穩(wěn)快速擴(kuò)展區(qū)。瞬斷區(qū):斷口粗糙,同靜載斷裂斷口,隨材料性質(zhì)而變。脆性材料:為解理或結(jié)晶狀斷口;韌性材料:在中間平面應(yīng)變區(qū)為放射狀或人字紋斷口;在邊緣平面應(yīng)力區(qū)為剪切唇。扭轉(zhuǎn)循環(huán)載荷:因最大正應(yīng)
50、力和軸向呈45°角,最大切應(yīng)力垂直軸向或平行軸向分布。正斷型扭轉(zhuǎn)疲勞斷口:與軸向呈45°角,且易出現(xiàn)鋸齒狀或星形狀花樣,如花鍵軸的斷口。切應(yīng)力引起的切斷型扭轉(zhuǎn)疲勞斷口:斷面垂直或平行于軸線,在疲勞斷口上一般看不到貝紋線。扭轉(zhuǎn)疲勞裂紋:還可沿最大剪應(yīng)力方向擴(kuò)展。疲勞過程:包括疲勞裂紋萌生、裂紋亞穩(wěn)擴(kuò)展及最后失穩(wěn)擴(kuò)展三個階段。疲勞壽命Nf :包括疲勞裂紋萌生期 N0 和裂紋亞穩(wěn)擴(kuò)展期 Np 所組成。一、疲勞裂紋萌生過程及機(jī)理宏觀疲勞裂紋是由微觀裂紋的形成、長大從連接而成的。疲勞裂紋萌生期:目前尚無統(tǒng)的尺度標(biāo)準(zhǔn),常將長約0.050.1mm的裂紋定為疲勞裂紋核,并由此確定疲勞裂紋萌
51、生期。主要方式:(1)表面滑移帶開裂;(2)第二相、夾雜物或其界面開裂;(3)晶界或亞晶界開裂等。(1) 滑移帶開裂產(chǎn)生裂紋 駐留滑移帶:大量試驗表明金屬在循環(huán)應(yīng)力(-1)長期作用下,即使其應(yīng)力低于屈服應(yīng)力,也會發(fā)生循環(huán)滑移,表面并形成循環(huán)滑移帶。(與靜載荷的均勻滑移帶不同)循環(huán)滑移:是極不均勻,集中分布于某些局部薄弱區(qū)域。駐留滑移帶:一般只在材料表面某些薄弱地區(qū)產(chǎn)生,具有持久駐留性。其深度較淺,隨著加載循環(huán)次數(shù)增加,會不斷地加寬,加寬至一定程度,因位錯塞積和交割作用,便在駐留滑移帶處形成微裂紋。 擠出脊和侵入溝:隨著加載循環(huán)次數(shù)增加,駐留滑移帶會不斷地加寬,在加寬過程中,還會出現(xiàn)擠出脊和侵入
52、溝,于是此處就產(chǎn)生應(yīng)力集中和空洞,經(jīng)過一定循環(huán)后也會產(chǎn)生微裂紋。擠出和侵入的現(xiàn)象:在很多實驗中曾經(jīng)觀察到,而且看到了由它所形成的裂紋。 擠出脊和侵入溝形成機(jī)理:柯垂?fàn)?A.H.Cottrell)和赫爾(D.Hu11)提出了交叉滑移模型。1)在拉應(yīng)力作用下,在取向最有利的滑移面上位錯源S1被激活,不斷增殖,滑移到表面便在P處留下一臺階。隨拉應(yīng)力增大,另一滑移面上位錯源S2也被激活,不斷增殖,滑移到表面,在 Q 處留下一臺階;與此同時,后一個滑移面上位錯運(yùn)動使第一個滑移面錯開,造成位借源S1與臺階P不再處于同一個平面內(nèi)2)進(jìn)入壓應(yīng)力的半周期,位錯源S1又被激活,向反方向滑動,在表面留下一反向滑移臺
53、階P,P處形成一個侵入溝;同時,也造成位錯源 S2 與臺階 Q 不處于一個平面。隨壓應(yīng)力增加,位錯源S2又被激活,沿反方向運(yùn)動,滑出表面留下一反向臺階Q,便在此處形成一擠出脊;同時又將位錯源 S1帶回原位置。與臺階P處于一個平面內(nèi)。如此不斷循環(huán),擠出脊高度和浸人溝深度將不斷增加,而寬度不變。 (二)相界面開裂產(chǎn)生裂紋在疲勞失效分析中,常發(fā)現(xiàn)很多疲勞源都由材料中第二相或夾雜物引起的,因此提出了第二相、夾雜物和基體界面開裂,或第二相、夾雜物本身開裂的疲勞裂紋萌生機(jī)理。(三)晶界開裂產(chǎn)生裂紋多晶材料:晶界作用,且相鄰晶粒不同取向性,位錯在某一晶粒內(nèi)運(yùn)動會受晶界阻礙,產(chǎn)生位錯塞積和應(yīng)力集中。在應(yīng)力循環(huán)
54、作用下,晶界處應(yīng)力集中不能松弛,應(yīng)力越來越大,當(dāng)超過晶界強(qiáng)度時會在晶界處產(chǎn)生裂紋二、疲勞裂紋擴(kuò)展過程及機(jī)理疲勞微裂紋萌生后即進(jìn)入擴(kuò)展階段,分為兩個階段1) 從表面?zhèn)€別侵入溝(擠出脊)先形成微裂紋,隨后,主要沿主滑移系方向(最大切應(yīng)力),以純剪切方式向內(nèi)擴(kuò)展第一階段:裂紋擴(kuò)展速率很低,且擴(kuò)展總量也很小,在斷口常看不到什么形貌特征,只有一些擦傷的痕跡。2) 第二階段:第一階段裂紋擴(kuò)展,因晶界不斷阻礙作用,會逐漸轉(zhuǎn)向垂直于拉應(yīng)力的方向,進(jìn)入第二階段擴(kuò)展。電鏡斷口分析表明:第二階段斷口特征是具有略呈彎曲并相互平行的溝槽花樣,稱為疲勞條帶(條紋)。它是裂紋擴(kuò)展時留下的微觀痕跡,每一條帶可視作一次應(yīng)力循環(huán)
55、的擴(kuò)展痕跡,裂紋擴(kuò)展方向與條帶垂直,疲勞條帶是疲勞斷口最典型微觀特征。疲勞條帶是疲勞斷口微觀特征,貝紋線是斷口的宏觀特征。疲勞裂紋擴(kuò)展的塑性鈍化模型為說明第二階段疲勞裂紋擴(kuò)展的物理過程,解釋疲勞條帶的形成原因,曾提出不少裂紋擴(kuò)展模型,其中比較公認(rèn)的是塑性鈍化模型。 在交變循環(huán)應(yīng)力作用下,因裂紋尖端的塑性張開鈍化和閉合銳化,會使裂紋向前延續(xù)擴(kuò)展。這種因塑性變形使裂紋尖端的應(yīng)力集中減小,滑移停止,裂紋不再擴(kuò)展的過程稱為“塑件鈍化”。每一應(yīng)力循環(huán),裂紋張開、鈍化、銳化、擴(kuò)展,在斷口上留下一條疲勞條帶,裂紋向前擴(kuò)展一條帶距離。如此反復(fù),不斷形成新條帶,裂紋也不斷向前擴(kuò)展。因此,疲勞裂紋擴(kuò)展第二階段是在
56、應(yīng)力循環(huán)下,裂紋尖端鈍銳反復(fù)交替變化的過程。第三節(jié) 影響疲勞強(qiáng)度的主要因素一、表面狀態(tài)的影響(一)應(yīng)力集中 機(jī)件表面缺口應(yīng)力集中,常是引起疲勞破壞的主要原因。(二)表面粗糙度在循環(huán)載荷作用下,金屬不均勻滑移集中在表面,疲勞裂紋也常在表面產(chǎn)生,故機(jī)件表面粗糙度對疲勞強(qiáng)度影響很大。材料強(qiáng)度越高,表面粗糙度對疲勞極限影響越顯著。二、殘余應(yīng)力及表面強(qiáng)化的影響殘余應(yīng)力狀態(tài)對疲勞強(qiáng)度(高周疲勞)有顯著影響:殘余壓應(yīng)力提高疲勞強(qiáng)度;殘余拉應(yīng)力則降低疲勞強(qiáng)度。殘余壓應(yīng)力:可有效降低缺口根部的拉應(yīng)力峰值,顯著提高機(jī)件的疲勞強(qiáng)度。三、材料成分及組織的影響 疲勞強(qiáng)度也是對材料組織結(jié)構(gòu)敏感的力學(xué)性能。(一)合金成分:是決定材料組織結(jié)構(gòu)的基本要
溫馨提示
- 1. 本站所有資源如無特殊說明,都需要本地電腦安裝OFFICE2007和PDF閱讀器。圖紙軟件為CAD,CAXA,PROE,UG,SolidWorks等.壓縮文件請下載最新的WinRAR軟件解壓。
- 2. 本站的文檔不包含任何第三方提供的附件圖紙等,如果需要附件,請聯(lián)系上傳者。文件的所有權(quán)益歸上傳用戶所有。
- 3. 本站RAR壓縮包中若帶圖紙,網(wǎng)頁內(nèi)容里面會有圖紙預(yù)覽,若沒有圖紙預(yù)覽就沒有圖紙。
- 4. 未經(jīng)權(quán)益所有人同意不得將文件中的內(nèi)容挪作商業(yè)或盈利用途。
- 5. 人人文庫網(wǎng)僅提供信息存儲空間,僅對用戶上傳內(nèi)容的表現(xiàn)方式做保護(hù)處理,對用戶上傳分享的文檔內(nèi)容本身不做任何修改或編輯,并不能對任何下載內(nèi)容負(fù)責(zé)。
- 6. 下載文件中如有侵權(quán)或不適當(dāng)內(nèi)容,請與我們聯(lián)系,我們立即糾正。
- 7. 本站不保證下載資源的準(zhǔn)確性、安全性和完整性, 同時也不承擔(dān)用戶因使用這些下載資源對自己和他人造成任何形式的傷害或損失。
最新文檔
- 2025年度智能家居加盟品牌授權(quán)合同3篇
- 二零二五年度新能源儲能系統(tǒng)購買合同3篇
- 二零二五年度林業(yè)人才培養(yǎng)合作造林協(xié)議3篇
- 2025年度老舊房屋漏水檢測與賠償專項協(xié)議3篇
- 2025年度股東退出與公司知識產(chǎn)權(quán)保護(hù)合同3篇
- 二零二五年度模特服裝租賃拍攝合同3篇
- 2025年度房地產(chǎn)公司合伙人項目合作協(xié)議3篇
- 二零二五年度循環(huán)水養(yǎng)殖養(yǎng)魚合作合同3篇
- 2025年度體育場館物業(yè)用房移交及賽事運(yùn)營服務(wù)合同3篇
- 2025年度企業(yè)年會活動宣傳片制作服務(wù)合同模板3篇
- 普通高校本科招生專業(yè)選考科目要求指引(通用版)
- 基坑工程監(jiān)控方案
- 中考生物試驗操作評分參考標(biāo)準(zhǔn)
- 國家開放大學(xué)電大本科《國際私法》期末試題及答案(n試卷號:1020)
- 四川省德陽市中學(xué)2023年高一物理上學(xué)期期末試卷含解析
- 舉高消防車基礎(chǔ)知識
- 空氣、物表地面消毒登記記錄
- 急性腦梗死診治指南
- 檢察院分級保護(hù)項目技術(shù)方案
- 土木工程建筑中混凝土裂縫的施工處理技術(shù)畢業(yè)論文
- 水電站工程地質(zhì)勘察報告
評論
0/150
提交評論