

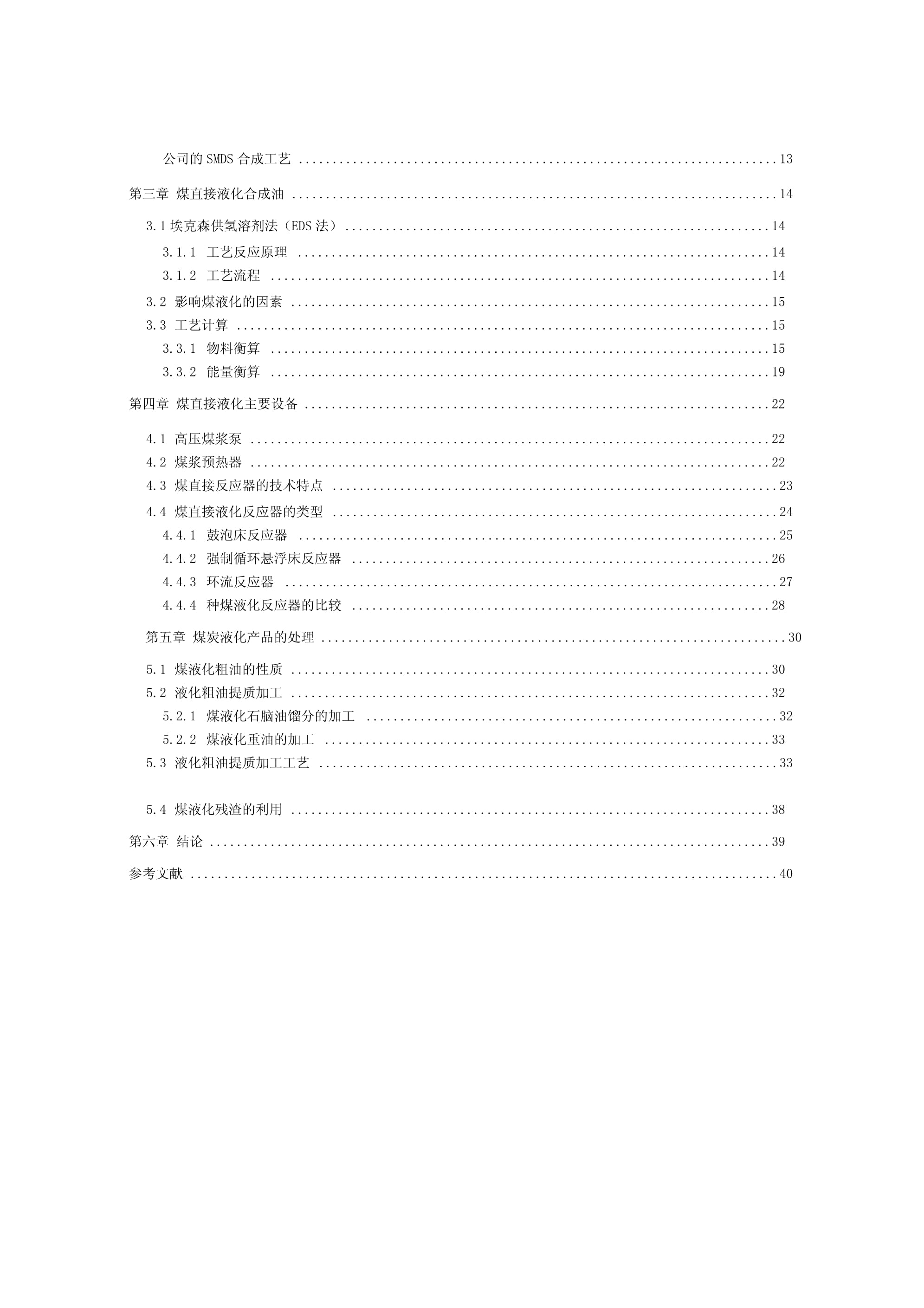
版權(quán)說明:本文檔由用戶提供并上傳,收益歸屬內(nèi)容提供方,若內(nèi)容存在侵權(quán),請進(jìn)行舉報或認(rèn)領(lǐng)
文檔簡介
煤直接液化制油的設(shè)計目錄TOC\o"1-5"\h\z摘要 1\o"CurrentDocument"第一章緒論 2\o"CurrentDocument"煤制油的發(fā)展歷程 2煤直接液化在世界的發(fā)展史 2煤炭間接液化制油在世界的發(fā)展史 3中國煤制油 4\o"CurrentDocument"煤制油的意義 4\o"CurrentDocument"第二章 煤炭液化的工藝 6\o"CurrentDocument"直接液化的基本原理 6、反應(yīng)模型 7\o"CurrentDocument"單段液化工藝 7221??松┑軇┓ǎ‥DS工藝) 7IGOR工藝流程描述 9\o"CurrentDocument"2.3、催化兩段液化工藝(CTSL工藝) 10\o"CurrentDocument"2.4煤間接液化工藝 12公司MTG工藝 12SASOL工藝 12公司的SMDS合成工藝 13\o"CurrentDocument"第三章煤直接液化合成油 14\o"CurrentDocument"3.1埃克森供氫溶劑法(EDS法) 14工藝反應(yīng)原理 14工藝流程 14影響煤液化的因素 15工藝計算 15物料衡算 15能量衡算 19\o"CurrentDocument"第四章煤直接液化主要設(shè)備 22\o"CurrentDocument"高壓煤漿泵 22\o"CurrentDocument"煤漿預(yù)熱器 22\o"CurrentDocument"煤直接反應(yīng)器的技術(shù)特點 23\o"CurrentDocument"煤直接液化反應(yīng)器的類型 24鼓泡床反應(yīng)器 25強制循環(huán)懸浮床反應(yīng)器 26環(huán)流反應(yīng)器 27種煤液化反應(yīng)器的比較 28\o"CurrentDocument"第五章煤炭液化產(chǎn)品的處理 30\o"CurrentDocument"煤液化粗油的性質(zhì) 30\o"CurrentDocument"液化粗油提質(zhì)加工 32煤液化石腦油餾分的加工 32煤液化重油的加工 33\o"CurrentDocument"液化粗油提質(zhì)加工工藝 33\o"CurrentDocument"煤液化殘渣的利用 38\o"CurrentDocument"第六章結(jié)論 39\o"CurrentDocument"參考文獻(xiàn) 40摘要石油是一種重要的戰(zhàn)略物質(zhì),有了它,船艦可以乘風(fēng)破浪,汽車可以翻山越嶺,飛機可以穿云透霧……然而,近年來國際石油價格飛漲,供需差距越來越大。以我國為例,石油年消費量約為2.5億噸,生產(chǎn)能力僅約15億噸,預(yù)計2005年和2015年消費量將超過2.6億噸和3.1億噸,尤其若干年后石油開采枯竭的時候,這些動力和交通工具又該靠什么來運行呢?不必?fù)?dān)心,聰慧的科學(xué)家們早已為我們設(shè)計了一個煤變石油的方案。許多勘探資料都表明,全世界煤的可開采資源是巨大的,其能量值相當(dāng)于石油資源的10倍。煤和石油的形態(tài)、形成歷史、地質(zhì)條件雖然不同,但是它們的化學(xué)組成卻大同小異。煤中約含碳80%~85%,含氫4%~5%,平均分子量在2000以上。石油含碳85%,含氫13%,平均分子量在600以內(nèi)。從組成上看,它們的主要差異是含氫量和分子量的不同。因此,只要人為地改變壓力和溫度,設(shè)法使煤中的氫含量不斷提高,就可以使煤的結(jié)構(gòu)發(fā)行變異,由大分子變成小分子。當(dāng)其碳?xì)浔冉档偷胶褪拖嘟鼤r,則煤就可以液化成汽油、柴油、液化石油氣、噴氣燃料等石油產(chǎn)品了。同時還可以開發(fā)出附加值很高的上百種產(chǎn)品,如乙烯、丙烯、醇、酮、化肥等,經(jīng)濟效益十分可觀。綜合我國總的能源特征是“富煤、少油、有氣”。2003年我國總能源消費量達(dá)11.783億噸油。其中,煤炭占67.86%,石油占23.35%,天然氣占2.5%,水電占5.43%,核能占0.83%。我國擁有較豐富的煤炭資源, 2000~2003年探明儲量均為1145億噸,儲采比由2000~2001年116年下降至2002年82年、2003年69年。而石油探明儲量2003年為32億噸,儲采比為19.1年。在較長一段時間內(nèi),我國原油產(chǎn)量只能保持在1.6~1.7億噸/年的水平。煤炭因其儲量大和價格相對穩(wěn)定,成為中國動力生產(chǎn)的首選燃料。在本世紀(jì)前50年內(nèi),煤炭在中國一次能源構(gòu)成中仍將占主導(dǎo)地位。預(yù)計煤炭占一次能源比例將由1999年67.8%、2000年63.8%、2003年67.8%達(dá)到2005年50%左右。我國每年燒掉的重油約3000萬噸,石油資源的短缺仍使煤代油重新提上議事日程,以煤制油己成為我國能源戰(zhàn)略的一個重要趨勢。關(guān)鍵詞:煤直接液化間接液化技術(shù)第一章緒論能源是社會、經(jīng)濟發(fā)展的基礎(chǔ)。優(yōu)化能源消費結(jié)構(gòu),安全保障能源供應(yīng)是中國經(jīng)濟建康發(fā)展、實現(xiàn)在21世紀(jì)中葉達(dá)到中等發(fā)達(dá)國家水平戰(zhàn)略目標(biāo)的重要支持和內(nèi)容。隨著中國經(jīng)濟的高速發(fā)展,如何有效地發(fā)揮煤炭資源優(yōu)勢,優(yōu)化能源結(jié)構(gòu),解決石油各短缺及由此造成的能源安全問題,已經(jīng)引起我國政府的高度重視。我國煤炭資源豐富,煤種齊全,煤炭資源占能源儲量的92%,這就決定了我國的能源生產(chǎn)和消費在相當(dāng)長的時期仍以煤炭為主,目前占70%左右。隨著能源消費總量的增加,煤炭需求總量將增加,大幅度減少煤炭消費是較難辦到的。另外,我國能源分布不均,重心偏西偏北,而經(jīng)濟發(fā)達(dá)區(qū)域偏南偏東,常規(guī)能源需要長途運輸才能滿足需求,而且煙煤型污染已經(jīng)給生態(tài)環(huán)境帶來嚴(yán)重問題。因此為了減少環(huán)境污染,提高煤炭利用效率,減少消費,降低C02排放量,生產(chǎn)便于運輸?shù)娜剂希_發(fā)出了煤炭液化技術(shù)。煤炭液化技術(shù)是指煤炭轉(zhuǎn)化為液態(tài)烴的技術(shù),可將煤轉(zhuǎn)化為汽油、柴油、 LPG等產(chǎn)品。因此,以國內(nèi)豐富的煤炭資源為基礎(chǔ),大力發(fā)展煤炭液化技術(shù),盡快實現(xiàn)商業(yè)化生產(chǎn),并最終形成新的煤炭能源轉(zhuǎn)化產(chǎn)業(yè),對于平衡我國能源結(jié)構(gòu),解決石油短缺具有重大戰(zhàn)略意義,其產(chǎn)業(yè)前景非常樂觀。從國家政策來看,以煤代油是中國長期能源政策中的重要組成部分,中央及地方政府十分支持“煤代油”技術(shù)的發(fā)展,其中煤炭液化是“煤代油”主要技術(shù)之一。我國已將發(fā)展煤炭液化列入國家“十五”發(fā)展規(guī)劃,中央高層領(lǐng)導(dǎo)對煤炭液化技術(shù)的發(fā)展也十分重視和支持。發(fā)展煤炭液化作為我國保證煤炭工業(yè)可持續(xù)展,緩解環(huán)境惡化,優(yōu)化能源結(jié)構(gòu),解決石油短缺,保證能源供應(yīng)安全的最有效途徑之一。煤制油的發(fā)展歷程煤液化技術(shù)可分為直接液化和間接液化兩大類。接近工業(yè)化的煤直接液化技術(shù)有:德國IG-OR工藝,美國HTI工藝,日本NEDOI工藝;已商業(yè)化的煤間接液化技術(shù)有:南非Sasol固定床高溫工藝石油一直是全球各國重要的戰(zhàn)略資源。煤直接液化在世界的發(fā)展史煤的直接液化:煤直接液化技術(shù)研究始于上世紀(jì)初的德國,1927年在Leuna建成世界上第一個10萬噸/年直接液化廠。1936?1943年間,德國先后建成11套直接液化裝置,1944年總生產(chǎn)能力達(dá)到400萬噸/年,為德國在第二次世界大戰(zhàn)中提供了近三分之二的航空燃料和50%的汽車及裝甲車用油。第二次世界大戰(zhàn)結(jié)束,美國、日本、法國、意大利及前蘇聯(lián)等國相繼開展了煤直接液化技術(shù)研究。50年代后期,中東地區(qū)廉價石油的大量開發(fā),使煤直接液化技術(shù)的發(fā)展處于停滯狀態(tài)。1973年,爆發(fā)石油危機,煤炭液化技術(shù)重新活躍起來。德國、美國及日本在原有技術(shù)基礎(chǔ)上開發(fā)出一些煤直接液化新工藝,其中研究工作重點是降低反應(yīng)條件的苛刻度,從而達(dá)到降低液化油生產(chǎn)成本的目的。目前不少國家已經(jīng)完成了中間放大試驗,為建立商業(yè)化示范廠奠定了基礎(chǔ)。世界上有代表性的煤直接液化工藝是德國的新液化( IGOR)工藝,美國的HTI工藝和日本的NEDO工藝。這些新液化工藝的共同特點是煤炭液化的反應(yīng)條件比老液化工藝大為緩和,生產(chǎn)成本有所降低,中間放大試驗已經(jīng)完成。目前還未出現(xiàn)工業(yè)化生產(chǎn)廠,主要原因是生產(chǎn)成本仍競爭不過廉價石油。今后的發(fā)展趨勢是通過開發(fā)活性更高的催化劑和對煤進(jìn)行頂處理以降低煤的灰分和惰性組分,進(jìn)一步降低生產(chǎn)成本。煤炭間接液化制油在世界的發(fā)展史煤炭間接液化技術(shù)主要有三種,即的南非的薩索爾( Sasol)費托合成法、美國的莫比爾法(Mobil)和正在開發(fā)的直接合成法。目前,煤間接液化技術(shù)在國外已實現(xiàn)商業(yè)化生產(chǎn),全世界共有3家商業(yè)生產(chǎn)廠正在運行,它們分別是南非的薩索爾公司和新西蘭、馬來西亞的煤炭間接液化廠。新西蘭煤炭間接液化廠采用的是Mobil液化工藝,但只進(jìn)行間接液化的第一步反應(yīng),即利用天然氣或煤氣化合成氣生產(chǎn)甲醇,而沒有進(jìn)一步以甲醇為原料生產(chǎn)燃料油和其它化工產(chǎn)品,生產(chǎn)能力1.25萬桶/天。馬來西亞煤炭間接液化廠所采用的液化工藝和南非薩索爾公司相似,但不同的是它以天然氣為原料來生產(chǎn)優(yōu)質(zhì)柴油和煤油,生產(chǎn)能力為50萬t/年。因此,從嚴(yán)格意義上說,南非薩索爾公司是世界上唯一的煤炭間接液化商業(yè)化生產(chǎn)企業(yè)。南非薩索爾公司成立于50年代初,1955年公司建成第一座由煤生產(chǎn)燃料油的Sasol-1廠。70年代石油危機后,1980年和1982年又相繼建成Sasol-2廠和Sasol-3廠。3個煤炭間接液化廠年加工原煤約4600萬t,產(chǎn)品總量達(dá)768萬t,主要生產(chǎn)汽油、柴油、蠟、氨、乙烯、丙烯、聚合物、醇、醛等 113種產(chǎn)品,其中油品占60%,化工產(chǎn)品占40%。該公司生產(chǎn)的汽油和柴油可滿足南非28%的需求量,其煤炭間接液化技術(shù)處于世界領(lǐng)先地位。此外,美國SGI公司于80年代末開發(fā)出了一種新的煤炭液化技術(shù),即LFC(煤提油)技術(shù)。該技術(shù)是利用低溫干餾技術(shù),從次煙煤或褐煤等非煉焦煤中提取固態(tài)的高品質(zhì)潔凈煤和液態(tài)可燃油。美國SGI公司于1992年建成了一座日處理能力為1000t的次煙煤商業(yè)示范廠。中國煤制油我國從70年代末開始進(jìn)行煤炭直接液化技術(shù)的研究和攻關(guān),其目的是用煤生產(chǎn)汽油、柴油等運輸燃料和芳香烴等化工原料。煤炭科學(xué)研究總院通過“六五”到“九五”的科技攻關(guān)和國際合作,先后從日本、德國引進(jìn)2套直接液化小型連續(xù)試驗裝置,從美國引進(jìn)一套液化油提質(zhì)加工試驗裝置,規(guī)模均為0.1t/天,并建有先進(jìn)的原料及產(chǎn)品分析檢驗裝備。經(jīng)過近20年的試驗研究,找出了14種適于直接液化的中國煤種;選出了5種活性較高的、具有世界先進(jìn)水平的催化劑;完成了4種煤的工藝條件試驗,為開發(fā)適于中國煤種的煤直接液化工藝奠定了基礎(chǔ);成功地將煤液化粗油加工成合格的汽油、柴油和航空煤油。目前,從煤一直到合格產(chǎn)品的全流程已經(jīng)打通,煤炭直接液化技術(shù)在中國已完成基礎(chǔ)性研究,為進(jìn)一步工藝放大和建設(shè)工業(yè)化生產(chǎn)廠打下了堅實的基礎(chǔ)。我國從50年代初即開始進(jìn)行煤炭間接液化技術(shù)的研究,曾在錦州進(jìn)行過4500t/年的煤間接液化試驗,后因發(fā)現(xiàn)大慶油田而中止。由于70年代的兩次石油危機,以及“富煤少油”的能源結(jié)構(gòu)帶來的一系列問題,我國自80年代初又恢復(fù)對煤間接液化合成汽油技術(shù)的研究,由中科院山西煤化所組織實施?!捌呶濉逼陂g,山西煤化所開的煤基合成汽油技術(shù)被列為國家重點科技攻關(guān)項目。1989年在代縣化肥廠完成了小型實驗?!鞍宋濉逼陂g,國家和山西省政府投資2000多萬元,在晉城化肥廠建立了年產(chǎn)2000噸汽油的工業(yè)試驗裝置,生產(chǎn)出了90號汽油。在此基礎(chǔ)上,提出了年產(chǎn)10萬噸合成汽油裝置的技術(shù)方案。目前,萬噸級煤基合成汽油工藝技術(shù)軟件開發(fā)和集成的研究正在進(jìn)行,從90年代初開始研究用于合成柴油的鈷基催化劑技術(shù)也正處在試驗階段。經(jīng)過20年的開發(fā)和研究,目前我國已經(jīng)具備建設(shè)萬噸級規(guī)模生產(chǎn)裝置的技術(shù)儲備,在關(guān)鍵技術(shù)、催化劑的研究開發(fā)方面已擁有了自主知識產(chǎn)權(quán)??梢赃@樣講,我國自己研發(fā)的煤炭液化技術(shù)已達(dá)到世界先進(jìn)水平。1.2煤制油的意義我國煤炭資源豐富,煤種齊全,發(fā)展煤炭液化、氣化等技術(shù),對發(fā)揮資源優(yōu)勢,優(yōu)化終端能源結(jié)構(gòu),大規(guī)模補充國內(nèi)石油供需缺口有著現(xiàn)實和長遠(yuǎn)意義。主要體現(xiàn)在:第一,產(chǎn)品為清潔能源,減少污染;第二,煤炭—能源化工一體化,發(fā)展新興產(chǎn)業(yè);第三,高新技術(shù)優(yōu)化集成,推動現(xiàn)代煤化工技術(shù)發(fā)展和產(chǎn)業(yè)化建設(shè);第四,建設(shè)大型企業(yè)和產(chǎn)業(yè)基地;第五,有效利用煤炭資源,高效利用,使各種煤種煤質(zhì)物盡其用,減少資源浪費;第六,經(jīng)濟效益最大化,通過建設(shè)大型工廠,提高綜合經(jīng)濟效益;第七,人力資源得到發(fā)揮。通過產(chǎn)業(yè)化建設(shè),帶動其他運輸、建筑、服務(wù)等行業(yè)發(fā)展,擴大就業(yè),充分利用人力資源。第二章煤炭液化的工藝煤的液化是先進(jìn)的潔凈煤技術(shù)和煤轉(zhuǎn)化技術(shù)之一,是用煤為原料以制取液體烴類為主要產(chǎn)品的技術(shù)。煤掖化分為“煤的直接液化”和“煤的間接液化”兩大類。煤直接液化煤在氫氣和催化劑作用下,通過加氫裂化轉(zhuǎn)變?yōu)橐后w燃料的過程稱為直接液化。裂化是一種使烴類分子分裂為幾個較小分子的反應(yīng)過程。因煤直接液化過程主要采用加氫手段,故又稱煤的加氫液化法。煤的間接液化是以煤基合成氣(CO+H2)為原料,在一定的溫度和壓力下,定向催化合成烴類燃料油和化工原料的工藝,包括煤氣化制取合成氣及其凈化、變換、催化合成以及產(chǎn)品分離和改質(zhì)加工等過程。通過煤炭液化,不僅可以生產(chǎn)汽油、柴油、LPG液化石油氣)、噴氣燃料,還可以提取BTX苯、甲苯、二甲苯),也可以生產(chǎn)制造各種烯烴及含氧有機化合物。煤炭液化可以加工高硫煤,硫是煤直接液化的助催化劑,煤中硫在氣化和液化過程中轉(zhuǎn)化成H2S再經(jīng)分解可以得到元素硫產(chǎn)品。直接液化的基本原理反應(yīng)機理大量研究證明,煤在一定溫度、壓力下的加氫液化過程基本分為三大步驟,首先,當(dāng)溫度升至300C以上時,煤受熱分解,即煤的大分子結(jié)構(gòu)中較弱的橋鍵開始斷裂,打碎了煤的分子結(jié)構(gòu),從而產(chǎn)生大量的以結(jié)構(gòu)單元分子為基體的自由基碎片,自由基的相對分子質(zhì)量在數(shù)百范圍。第二步,在具有供氫能力的溶劑環(huán)境和較高氫氣壓力的條件下,自由基被加氫得到穩(wěn)定,成為瀝青烯及液化油的分子。能與自由基結(jié)合的氫并非是分子氫(H2),而應(yīng)是氫自由基,即氫原子,或者是活化氫分子,氫原子或活化氫分子的來源有:①煤分子中碳?xì)滏I斷裂產(chǎn)生的氫自由基;②供氫溶劑碳?xì)滏I斷裂產(chǎn)生的氫自由基;③氫氣中的氫分子被催化劑活化;④化學(xué)反應(yīng)放出的氫,如系統(tǒng)中供給(C0+H2。),可發(fā)生變換反應(yīng)(COH2。CO2H2)放出氫。當(dāng)外界提供的活性氫不足時,自由基碎片可發(fā)生縮聚反應(yīng)和高溫下的脫氫反應(yīng),最后生成固半焦或焦炭。第三步,瀝青烯及液化油分子被繼續(xù)加氫裂化生成更小的分子。所以,煤液化過程中,溶劑及催化劑起著非常重要的作用。、反應(yīng)模型為了能利用計算機模擬計算煤液化反應(yīng)的結(jié)果,根據(jù)以上反應(yīng)機理的分析,許多研究者假設(shè)了煤加氫液化的各種反應(yīng)模型。最有代表性的是日本研究者的模型,見圖2-1-12-1-1煤液化反應(yīng)模型該模型假設(shè)原料煤分成三種類型。CI是不反應(yīng)的惰性煤。CB熱解只產(chǎn)生瀝青烯類物質(zhì)。CA熱解產(chǎn)生氣體、重質(zhì)油和瀝青烯三種物質(zhì)。瀝青烯加氫產(chǎn)生氣體、水、輕質(zhì)油,CA產(chǎn)生的重質(zhì)油加氫產(chǎn)生中油。通過積累大量試驗數(shù)據(jù),可算出模型中的各反應(yīng)的級數(shù)及速度常數(shù)冷, 再通過不同溫度下求出的k值,可求出各反應(yīng)的活化能。以上反應(yīng)機理實際上并不是真正的墓元反應(yīng), 由此得出的動力學(xué)模型僅僅是一種表觀的形式,但被應(yīng)用于反應(yīng)器模擬計算時已足夠了。也可以劃到這兩種工藝中去。同樣,兩種液化工藝都可改進(jìn)用來做煤油共處理。2.2單段液化工藝??松┑軇┓ǎ‥DS工藝)EDS是美國公司開發(fā)的一種煤炭直接液化工藝。公司從1966年開始研究煤炭直接液化技術(shù),對EDS工藝進(jìn)行開發(fā),并在0.5t/d的連續(xù)試驗裝置上確認(rèn)了EDS工藝的技術(shù)可行性。1975年6月,1.0t/d規(guī)模的ETA工藝全流程中試裝置投人運行,進(jìn)一步肯定了ELF工藝的可靠性。1980年在德克薩斯的建了250t/d的工業(yè)性試驗廠,完成了EDS工藝的研究開發(fā)工作。EDS工藝的基本原理是利用間接催化加氫液化技術(shù)使煤轉(zhuǎn)化為液體產(chǎn)品, 即通過對產(chǎn)自工藝本身的作為循環(huán)溶劑的餾分,在特別控制的條件下采用類似于普通催化加氫的方法進(jìn)行加氫,向反應(yīng)系統(tǒng)提供氫的“載體”。加氫后的循環(huán)溶劑在反應(yīng)過程中釋放出活性氫提供給煤的熱解自由基碎片。釋放出活性氫的循環(huán)溶劑餾分通過再加氫恢復(fù)供氫能力,制成煤漿后又進(jìn)人反應(yīng)系統(tǒng),向系統(tǒng)提供活性氫。通過對循環(huán)溶劑的加氫提高溶劑的供氫能力,是EDS工藝的關(guān)鍵特征,工藝名稱也由此得來。烝曲>圖2-1-1 工藝流程圖EDS工藝流程描述煤與加氫后的溶劑制成煤漿后,與氫氣混合,預(yù)熱后進(jìn)人上流式管式液化反應(yīng)器,反應(yīng)溫度425~450C和液體產(chǎn)物,反應(yīng)壓力17.5MPa不需另加催化劑。反應(yīng)產(chǎn)物進(jìn)入氣液分離器,分出氣體產(chǎn)物。氣體產(chǎn)物通過分離后,富氫氣與新鮮氫混合使用。液體產(chǎn)物進(jìn)入常、減壓蒸餾系統(tǒng),分離成氣體燃料、石腦油、循環(huán)溶劑餾分、和其他液體產(chǎn)品及含固體的減壓塔釜底殘渣。循環(huán)溶劑餾分(中、重餾分)進(jìn)入溶劑加氫單元,通過催化加氫恢復(fù)循環(huán)溶劑的供氫能力。循環(huán)溶劑的加氫在固定床催化反應(yīng)器中進(jìn)行, 使用的催化劑是石油工業(yè)傳統(tǒng)的鎳一鉬或鉆一鉑鋁載體加氫催化劑。反應(yīng)器操作溫度 370r,操作壓力11MPa改變條件可以控制溶劑的加氫深度和質(zhì)量。溶劑加氫裝置可在普通的石油加氫裝置上進(jìn)行。加氫后的循環(huán)溶劑用于煤漿制備。含固體的減壓塔釜底殘渣在流化焦化裝置進(jìn)行焦化,以獲得更多的液體產(chǎn)物。流化焦化產(chǎn)生的焦在氣化裝置中氣化制取燃料氣。流化焦化和氣化被組合在一套裝置中聯(lián)合操作,被稱為靈活焦化法。靈活焦化法的焦化部分反應(yīng)溫度為 485~650C,氣化部分的反應(yīng)溫度為800~900C。整個停留時間為0.5—lh。EDS工藝的產(chǎn)油率較低,有大量的前瀝青烯和瀝青烯未轉(zhuǎn)化為油,可以通過增加
煤漿中減壓蒸餾的塔底物的循環(huán)量來提高液體收率。 EDS工藝典型的總液體收率(包括靈活焦化產(chǎn)生的液體)為:褐煤36%,次煙煤38%,煙煤39%~46%全(部以干基無灰煤為計算基準(zhǔn))。EDS工藝采用供氫溶劑來制備煤漿,所以液化反應(yīng)條件溫和,但由于液化反應(yīng)為非催化反應(yīng),液化油收率低,這是非催化反應(yīng)的特征。加重質(zhì)餾分的停留時間可以改善液化油收率,雖然將減壓蒸餾的塔底物部分循環(huán)送回反應(yīng)器但同時帶來煤中礦物質(zhì)在反應(yīng)器中的積聚問題,增加重質(zhì)餾分的停留時間可以改善液化油收率 ,但同時帶來煤中礦物質(zhì)在反應(yīng)器中的積聚時間問題。IGOR工藝流程描述煤與循環(huán)溶劑及“赤泥”可棄鐵系催化劑配成煤漿,與氫氣混合后預(yù)熱。預(yù)熱后的混合物一起進(jìn)人液化反應(yīng)器,典型操作溫度470C,壓力30.0MPa,反應(yīng)空速0.5"(m3-h}反應(yīng)器產(chǎn)物進(jìn)入高溫分離器。高溫分離器底部液化粗油進(jìn)人減壓閃蒸塔,減壓閃蒸塔底部產(chǎn)物為液化殘渣,頂部閃蒸油與高溫分離器的頂部產(chǎn)物一起進(jìn)人第一固定床反應(yīng)器,反應(yīng)條件:溫度350一420C,壓力與液化反應(yīng)器相同, 第一固定床反應(yīng)器產(chǎn)物進(jìn)人中溫分離器。中溫分離器底部重油為循環(huán)溶劑,去用于煤漿制備。中溫分離器頂部產(chǎn)物進(jìn)人第二固定床反應(yīng)器,反應(yīng)條件:溫度350~420C,壓力與液化反應(yīng)器相同,第二固定床反應(yīng)器產(chǎn)物進(jìn)人低溫分離器,低溫分離器頂部副產(chǎn)氫氣循環(huán)使用。低溫分離器底部產(chǎn)物進(jìn)人常壓蒸餾塔,在常壓蒸餾塔中分餾為汽油和柴油。IGOR工藝的操作條件在現(xiàn)代液化工藝中最為苛刻,所以適合于煙煤的液化。在處理煙煤時,可得到大于90%的轉(zhuǎn)化率,液收率以無水無灰煤計算為50%~60%液化油在IGOR工藝中經(jīng)過十分苛刻條件的加氫精制后,產(chǎn)品中的S、N含量降到10數(shù)量級(幾十個ppm數(shù)量級)。表2-2-1為德國煙煤在IGOR工藝中的產(chǎn)率結(jié)果和產(chǎn)品性質(zhì)表。表2-2-1為云南先鋒揭煤在IGOR工藝中的液化結(jié)果。
圖2-2-1德國煙煤IGORX藝產(chǎn)率和產(chǎn)品性質(zhì)產(chǎn)物產(chǎn)率(質(zhì)量分?jǐn)?shù))烴類氣體(C1~C4)19.0輕油(C5?200C)25.3中油(200?325C)32.6未反應(yīng)的煤和瀝冃22.1產(chǎn)品性質(zhì)輕油 中油氫%(質(zhì)量分?jǐn)?shù))13.611.9氮106(質(zhì)量分?jǐn)?shù))391746氧10(質(zhì)量分?jǐn)?shù))15384硫106(質(zhì)量分?jǐn)?shù))12<5密度/(kg/m\7729122.3、催化兩段液化工藝(CTSL工藝)催化兩段液化工藝是H-Coal單段工藝的發(fā)展。在美國的液化試驗裝置上,對該工藝進(jìn)行了 15年的研究。該工藝現(xiàn)在已演化成在20世紀(jì)80年代和20世紀(jì)卯年代美國能源部資助的許多液化工藝的組合。采用了緊密串聯(lián)結(jié)構(gòu),每段都使用活性載體催化劑。此工藝現(xiàn)稱作催化兩段液化工藝。由美國能源部資助,美國碳?xì)浠衔镅芯抗荆℉RI)開發(fā),包括PDU規(guī)模試驗。催化兩段液化工藝工藝流程見圖Iftifl分隔瞎Iftifl分隔瞎圖2-3-1 催化劑兩段液化工藝(CTSL)流程圖催化兩段液化工藝(CTSL)工藝流程描述煤與循環(huán)溶劑配成煤漿,預(yù)熱后,與氫氣混合加入到沸騰床反應(yīng)器的底部。反應(yīng)器內(nèi)填裝載體催化劑,通常為鎳一銘鋁載體催化劑(有些工藝使用分散可棄催化劑),催化劑被反應(yīng)器內(nèi)部循環(huán)流流態(tài)化。因此反應(yīng)器具有連續(xù)攪抨釜式反應(yīng)器的均一溫度特征。溶劑具有供氫能力,在第一反應(yīng)器中,通過將煤的結(jié)構(gòu)打碎到一定程度而將煤溶解。第一反應(yīng)器也對溶荊進(jìn)行再加氮。操作壓力是17.0MPa,操作溫度在400~420C。反應(yīng)產(chǎn)物直接進(jìn)人第二段沸騰床反應(yīng)器中,操作壓力與第一段相同但溫度要高。反應(yīng)器也裝有載體催化劑。操作溫度通常達(dá)至 420~440C。 第二反應(yīng)器的產(chǎn)物經(jīng)分離和減壓后,進(jìn)入常壓蒸餾塔,蒸餾切割出沸點小于400C餾分,常壓蒸餾塔塔底含有溶劑、未反應(yīng)的煤和礦物質(zhì)。常壓蒸餾塔塔底物進(jìn)行固液分離,脫除固體,溶劑循環(huán)至煤漿段。在有些工藝中只有部分常壓蒸餾塔底進(jìn)行固體分離, 這樣,循環(huán)溶劑中含有礦物質(zhì)和可能使用的分散催化劑。固液分離方法采用 Kerr-McGeeCSD/ROS工藝表2-3-1列出CTSLX藝液化煙煤時產(chǎn)品的典型性質(zhì)和產(chǎn)率。圖2-3-1催化兩段液化方法產(chǎn)品性質(zhì)產(chǎn)率/%(質(zhì)量分?jǐn)?shù))產(chǎn)率/%(質(zhì)量分?jǐn)?shù))產(chǎn)率/%(質(zhì)量分?jǐn)?shù))G~C48.6氫耗/%質(zhì)量分?jǐn)?shù)7.9H/%(質(zhì)量分?jǐn)?shù))11.73C4~272C19.7煤轉(zhuǎn)化率/%質(zhì)量分?jǐn)?shù)96.8272~346C36.0>C4餾分油質(zhì)量N/%(質(zhì)量分?jǐn)?shù))0.25346~402C22.2API 27.62.4煤間接液化工藝公司MTGT藝甲醇轉(zhuǎn)化成汽油MTG技術(shù)是由Mobil研究與開發(fā)公司開發(fā)成功,該技術(shù)間接克服了煤基合成甲醇直接作燃料的缺點。成為煤轉(zhuǎn)化成汽油的重要途徑。這一技術(shù)的核心是選擇沸石分子篩催化劑ZSM-5,其優(yōu)點是較F-T合成的成本低、合成汽油的芳烴含量高,特別是均四甲苯的含量達(dá)3.6%,在性能上又與無鉛汽油相當(dāng)。MTG反應(yīng)為強放熱反應(yīng),在絕熱條件下,體系溫度可達(dá)到610C左右。遠(yuǎn)超過反應(yīng)允許的反應(yīng)溫度范圍,因此反應(yīng)生成熱量必須移出,為此Mobile公司開發(fā)出兩種類型的反應(yīng)器。一是絕熱固定床反應(yīng)器,另二一個是流化床反應(yīng)器, 1979年以來美國化學(xué)系統(tǒng)公司又成功地開發(fā)出漿態(tài)床甲醇合成技術(shù)并完成了中試研究,漿態(tài)床比其他反應(yīng)器有獨特優(yōu)點。絕熱固定床反應(yīng)器把反應(yīng)分為兩段,第一階段反應(yīng)器為脫水反應(yīng)器,在其中完成二甲醚合成反應(yīng),在第二階段反應(yīng)器中完成甲醇、二甲醚和水平衡混合物轉(zhuǎn)化成烴的反應(yīng)。第一、第二反應(yīng)器中反應(yīng)熱分別占總反應(yīng)熱的百分?jǐn)?shù)為 20%和80%。工藝流程如圖2-2-1。甲醇轉(zhuǎn)化反應(yīng)是在催化劑上一狹窄帶狀區(qū)域進(jìn)行,隨反應(yīng)時間延長,這一催化劑帶失活,催化反應(yīng)逐步沿反應(yīng)器向下移動,最終整個反應(yīng)器中的催化劑活化需要再生,圖2-2-1有四個反應(yīng)器,在實際生產(chǎn)中正常操作條件下,至少有一個反應(yīng)器在再生。MTG反應(yīng)器由于積炭而失活,需要周期性再生,再生周期一般為 20天,可通過通入熱空氣進(jìn)行再生。二甲醚反應(yīng)器不積炭。正常情況下無需再生。流化床反應(yīng)器與固定床反應(yīng)器完全不同,流化床反應(yīng)器中,用一個反應(yīng)器代替兩段固定床反應(yīng)器。甲醉與水混合后加人反應(yīng)器,加料為液態(tài)或氣態(tài)。在反應(yīng)器上部氣態(tài)反應(yīng)產(chǎn)物與催化劑分。SASOL工藝薩索爾(Sasol)是南非煤炭、石油和天然氣股份有限公司(SouthAfricanCoal,OilandGasCorp.)的簡稱。南非缺乏石油資源但卻蘊藏有大量煤炭資源。為了解決當(dāng)?shù)厥偷男枨髥栴},于1951年籌建了SASOL公司。1955年建成了第一座由煤生產(chǎn)液體運輸燃料的SASOL-I廠。建設(shè)由美國凱洛格公司及原西德的阿奇公司(Arge即ArbeitGemeinshaftLurgiundRuhrchemie) 承包。阿奇建造的五臺固定床反應(yīng)器作為第一段,年產(chǎn)量為53,000t初級產(chǎn)品,開洛格建造了兩套流化床反應(yīng)器(Synthol),設(shè)計年產(chǎn)液體燃料166000t,在SASOL-I廠成功的經(jīng)驗上,1974年開始,南非在賽昆達(dá)地區(qū)開工建設(shè)了SASOL-II廠,并于1980年建成投產(chǎn)。1979年又在賽昆達(dá)地區(qū)建設(shè)了SASOL-III廠,規(guī)模與II廠相同,造氣能力大約是SASOL-I廠的8倍。隨著時代的變遷和技術(shù)的進(jìn)步,SASOL三個廠的生產(chǎn)設(shè)備、生產(chǎn)能力和產(chǎn)品結(jié)構(gòu)都發(fā)生了很大的變化。目前三個廠年用煤 4590萬t,其中I廠650萬t/年,II廠和III廠3940萬t/年。主要產(chǎn)品是汽油、柴油、蠟、氨、烯烴、聚合物、醇、醛等113種,總產(chǎn)量達(dá)760萬t,其中油品大約占60%公司的SMDS^成工藝值高的條件下,可以高選擇性和高收率地合成高分子長鏈烷烴,同時也大大降低了低碳?xì)鈶B(tài)烴的生成。在1985年第五次合成燃料研討會上,該公司宣布已開發(fā)成功F-T合成兩段法的新技術(shù)—SMDS(Shell多年來,荷蘭皇家Shell石油公司一直在進(jìn)行從煤或天然氣基合成氣制取發(fā)動機燃料的研究開發(fā)工作。尤其對一氧化碳加氫反應(yīng)的Schulz-Flory聚合動力學(xué)的規(guī)律性進(jìn)行了深入的研究,認(rèn)為在鏈增長的MiddleDistillateSynthesis)工藝,并通過中試裝置的長期運轉(zhuǎn)。SMDS合成工藝由一氧化碳加氫合成高分子石蠟烴一HPS(HeavyParaffinSynthesis)過程和石蠟烴加氫裂化或加氫異構(gòu)化—HPC(HeavyParaffinCoversion)制取發(fā)動機燃料兩段構(gòu)成。Shell公司的報告指出,若利用廉價的天然氣制取的合成氣(H2/CO=2.0)為原料,采用SMD工藝制取汽油、煤油和柴油產(chǎn)品,其熱效率可達(dá)60%,而且經(jīng)濟上優(yōu)于其他F-T合成技術(shù)。值可控制在0.80?0.94之間。HPS技術(shù)采用管式固定床反應(yīng)器。為了提高轉(zhuǎn)化率,合成過程分兩段進(jìn)行。第一段安排了3個反應(yīng)器。第二段只設(shè)一個反應(yīng)器。每一段設(shè)有單獨的循環(huán)氣體壓縮機。大約總產(chǎn)量的 85%在第一段生成,其余15%在第二段生成。反應(yīng)系統(tǒng)操作參數(shù)如下:合成氣組成H2/CO=2.0,反應(yīng)壓力2.0 Shell公司采用自己開發(fā)的熱穩(wěn)定性較好的鈷系催化劑高選擇性地合成了長鏈?zhǔn)灍N (?C50),其鏈增長MPa?4.0MPa,反應(yīng)溫度200E?240E,全過程CO轉(zhuǎn)化率:95%單程單段CO轉(zhuǎn)化率40%第三章煤直接液化合成油3.1??松淙軇┓ǎ‥DS法)工藝反應(yīng)原理EDS工藝的基本原理是利用間接催化加氫液化技術(shù)使煤轉(zhuǎn)化為液體產(chǎn)品, 即通過對產(chǎn)自工藝本身的作為循環(huán)溶劑的餾分,在特別控制的條件下采用類似于普通催化加氫的方法進(jìn)行加氫,向反應(yīng)系統(tǒng)提供氫的“載體”。加氫后的循環(huán)溶劑在反應(yīng)過程中釋放出活性氫提供給煤的熱解自由基碎片。釋放出活性氫的循環(huán)溶劑餾分通過再加氫恢復(fù)供氫能力,制成煤漿后又進(jìn)人反應(yīng)系統(tǒng),向系統(tǒng)提供活性氫。通過對循環(huán)溶劑的加氫提高溶劑的供氫能力,是EDS工藝的關(guān)鍵特征,工藝名稱也由此得來。工藝流程煤與加氫后的溶劑制成煤漿后,與氫氣混合,預(yù)熱后進(jìn)人上流式管式液化反應(yīng)器,反應(yīng)溫度425~450C,反應(yīng)壓力17.5MP&不需另加催化劑。反應(yīng)產(chǎn)物進(jìn)入氣液分離器,分出氣體產(chǎn)物和液體產(chǎn)物。氣體產(chǎn)物通過分離后,富氫氣與新鮮氫混合使用。液體產(chǎn)物進(jìn)人常、減壓蒸餾系統(tǒng),分離成氣體燃料、石腦油、循環(huán)溶劑餾分、和其他液體產(chǎn)品及含固體的減壓塔釜底殘渣。循環(huán)溶劑餾分(中、重餾分)進(jìn)人溶劑加氫單元,通過催化加氫恢復(fù)循環(huán)溶劑的供氫能力。循環(huán)溶劑的加氫在固定床催化反應(yīng)器中進(jìn)行,使用的催化劑是石油工業(yè)傳統(tǒng)的鎳一鉬或鉆一鉬鋁載體加氫催化劑。反應(yīng)器操作溫度370C,操作壓力11MPa改變條件可以控制溶劑的加氫深度和質(zhì)量。溶劑加氫裝置可在普通的石油加氫裝置上進(jìn)行。加氫后的循環(huán)溶劑用于煤漿制備。EDS的特點:EDS工藝的產(chǎn)油率較低,有大量的前瀝青烯和瀝青烯未轉(zhuǎn)化為油,減壓蒸餾的塔底物的循環(huán)量來提高液體收率。3.2影響煤液化的因素3.3工藝計算物料衡算1、基礎(chǔ)數(shù)據(jù)年生產(chǎn)力:1600000t/a年開工時數(shù):8000h原料采用義馬褐煤,元素質(zhì)量組成如表 3-3-1-1所示表3-3-1-1元素質(zhì)量組成元素組分質(zhì)量%元素組分質(zhì)量%C70.62N2.48H6.28S1.16O18.92[P0.54(4)產(chǎn)品組成如表3-3-1-2所示產(chǎn)品組成質(zhì)量%產(chǎn)品組成質(zhì)量%氣體ACH415.725.46液體AC4H10 輕質(zhì)油32.8021.46C2H647.88C5?C11汽油78.54C2H426.66氣體BC3H67.618.52液體BC11?C18柴油43.90C3H835.70C4H845.78(5)基準(zhǔn)年工作為8000h,以1h為基準(zhǔn)416010 8000=200t/h以100t/h為基準(zhǔn)進(jìn)行計算2、計算范圍全裝置如圖3-3-2所示3、物料衡算(1)產(chǎn)品的計算生產(chǎn)出液體的量戰(zhàn)總產(chǎn)品的比例:32.80%+43.90%=71.70%總產(chǎn)品的質(zhì)量:200 76.70%=260.7562t/h混合氣體A的質(zhì)量:260.756215.70%=40.9837t/h混合氣體B的質(zhì)量:260.75627.60%=19.8175t/h混合液體A的質(zhì)量:260.756232.80%=85.5280t/h混合液體B的質(zhì)量:260.756243.90%=114.4732t/h甲烷的質(zhì)量:40.983725.46%=10.4344t/h乙烷的質(zhì)量:40.983747.88%=19.6016t/h乙烯的質(zhì)量:40.983726.66%=10.9142t/h丙烯的質(zhì)量:19.817518.52%=3.6702t/h丙烷的質(zhì)量:19.817535.70%=7.7048t/h丁烯的質(zhì)量:19.817545.78%=9.0724t/h輕質(zhì)油的質(zhì)量:85.528021.46%=18.3554t/h汽油的質(zhì)量:85.528078.54%=67.1736t/h柴油的質(zhì)量:260.756243.90%=114.4732t/h(2)原料的計算設(shè)制取100t/h的產(chǎn)品油所需的原料為At/h。則所用催化劑為:4%At/h全過程的氫耗量為:5.80%At/h其中,加氫反應(yīng)器I中的氫耗量占總量的 68.00%加氫反應(yīng)器U中的氫耗量占總量的32.00%另殘渣內(nèi)含油8.00%,全工藝流程如裝置圖所示:進(jìn)入反應(yīng)器的量:A+4%A=104.00%At/h高溫分離器分離出的氣體及輕油量:82.00%At/h高溫分離器分離出的重質(zhì)物料量:18.00%At/h減壓塔分離出的油量:18.00%A76.00%t/h減壓塔分離出的殘渣量:18.00%A24.00%t/h殘渣內(nèi)含油量:18.00%A24.00%8.00%t/h實際的殘渣量:18.00%A24.00%(1-8.00)t/h進(jìn)入氫反應(yīng)器I的氣體及輕油量: 82.00%A+18.00%A76.00%t/h加氫反應(yīng)器I的氫耗量:5.80%A68.00%t/h進(jìn)入中溫分離器分離的總量:82.00%A+18.00%A76.00%+5.80%A68.00%t/h中溫分離器分離出的氣體及輕質(zhì)油量:(82.00%A+18.00%A76.00%+5.80%A68.00%)94.00%t/h中溫分離器分離出的重質(zhì)油量:(82.00%A+18.00%A76.00%+5.80%A68.00%)6.00%t/h循環(huán)溶劑的量:18.00%A24.00%+(82.00%A+18.00%A76.00%+5.80%A68.00%)6.00%t/h加氫反應(yīng)器U的氫耗量:5.80%A32.00%t/h進(jìn)入低溫分離器的產(chǎn)品總量:(82.00%A+18.00%A76.00%+5.80%A68.00%)94.00%t+5.80%A32.00%t/h由a過程知總產(chǎn)品的質(zhì)量:130.3781t/h則進(jìn)入低溫分離器的產(chǎn)品總量:( 82.00%A+18.00%A 76.00%+5.80%A 68.00% )94.00%t+5.80%A32.00%t/h=260.7562A=273.0432tt/h故得出:催化劑的加入量:4%136.5216t/h=5.4609t/h全過程氫的消耗量:5.80%136.5216t/h=7.9138t/h進(jìn)入反應(yīng)器的量:A+4%A=104.00136.5216t/h=141.9825t/h高溫分離器分離出的氣體及輕油量: 82.00%136.5216t/h=111.9477t/h高溫分離器分離出的重質(zhì)油量: 18.00%136.5216t/h=24.5739t/h減壓塔分離出的油量:18.00%136.5216t/h76.00%t/h=18.6761t/h減壓塔分離出的殘渣量:18.00%136.5216t/h24.00%t/h=5.8977t/h殘渣內(nèi)含油量:18.00%136.5216t/h 24.00%8.00%=0.4718t/h實際的殘渣量:18.00%A24.00% (1-8.00)=5.4259t/h進(jìn)入氫反應(yīng)器I的氣體及清油量:82%136.5216t/h+136.5216t/h 76%=130.6239t/h進(jìn)入反應(yīng)器I的氫耗量:5.80%136.5216t/h68.00%=5.3846t/h進(jìn)入中溫分離器分離出的氣體及輕質(zhì)油量:(82%136.5216t/h+136.5216t/h 76%+5.80%136.5216t/h 68.00%)94.00%=130.5682t/h中溫分離器分離的重質(zhì)油量:(82%136.5216t/h+136.5216t/h 76%+5.80%136.5216t/h 68.00%)6.00%=8.1605t/h循環(huán)溶劑的量:18.00%136.5216t/h 24.00%+(82.00%136.5216+18.00%136.5216t/h 76.00%+5.80135.5216t/h 68.00%)6.00%=14.0582t/h加氫反應(yīng)器U的氫耗量:5.80%135.5216t/h32.00%=2.5339t/h125136.5216= 170.6250由此知實際需煤量: 100煤液化物料衡算如表3-3-3所示表3-3-3煤液化物料衡算組分組成輸入輸出原料質(zhì)量t產(chǎn)品質(zhì)量t煤136.5216總產(chǎn)品130.3781C96.4116ch45.2115
H8.5736C2H69.8008O25.8299C2H45.4751N3.3857C3H61.8351S1.5837C3H83.5374P0.7372C4H84.5362H27.91836已。輕質(zhì)油9.1772C5~C11汽油33.5868C11~C18柴油57.2360殘油渣5.8977循環(huán)溶劑容量3.1605合計144.4399合計144.4399332能量衡算1.基礎(chǔ)數(shù)據(jù)(1)各產(chǎn)物的比熱容如表3-3-2-1所示表3-3-2-1產(chǎn)物的比熱容產(chǎn)品比熱容kJ/kgC產(chǎn)品比熱容kJ/kgC甲烷1.70丁烯2.314乙烷1.44輕質(zhì)油1.730乙烯1.222汽油2.200丙烷1.65柴油2.100丙烯2.436(2)已知能量公式Q=CM,進(jìn)口溫度350C,出口溫度25C,由物料衡算知各物料的質(zhì)量。計算范圍對液體在低溫分離器分離過程進(jìn)行能量衡算能量衡算對低溫分離器進(jìn)口處各物料進(jìn)行能量計算
對低溫分離器進(jìn)口處各物料進(jìn)行能量計算36甲烷的能量:10.4344103170350=6.2016106kJ乙烷的能量:19.60161031.44350=9.8792106kJ乙烯的能量:10.91421031.222350=4.6680106kJ丙烷的能量:7.70481031.65350=4.0856106kJ丙烯的能量:3.67021032.436350=3.130106kJ丁烯的能量:9.07243102.314350=7.3478106kJ輕質(zhì)油的能量:18.35541031.7350=11.1136106kJ汽油的能量:67.17361032.200350=5.1722107kJ37柴油的能量:114.47321032.100350=8.4136107kJ低溫分離器進(jìn)口處各物料的總能量:6666663.100810+9.879210+4.668010+4.085610+3.13010+7.347810+11.1167773635101.7325=7.938210kJ10+5.172210+8.4136103635101.7325=7.938210kJ甲烷的能量:10.43441031.70025=4.429810乙烷的能量:319.60161031.44525=7.056610kJ乙烯的能量:10.91421031.22225=3.3342105kJ丙烷的能量:7.70481031.6525=2.9184105kJ丙烯的能量:3.67021032.43625=2.2352105kJ丁烯的能量:39.0724102.314525=4.852410kJ輕質(zhì)油的能量:18.35545kJ36汽油的能量:67.17361032.20025=3.6946106kJ36柴油的能量:114.4732102.10025=6.009810kJ
低溫分離器出口處各物料的總能量:TOC\o"1-5"\h\z5 5 5 5 5 54.429810+7.056610+3.334210+2.918410+2.235210+4.852410+7.9385 6 6 6210+3.694610+6.009810=12.300410kJ7 6 7出的熱量:Q放=Q進(jìn)-Q出=18.284410—12.300410=16.984410kJ煤液化能量衡算如表3-3-2-2所示表3-3-2-2煤液化能量衡算各組分組成產(chǎn)品6輸入能量Q(10kJ)輸出能量Q(10kJ)ch46.20164.4298C2H69.87927.0566C2H44.66803.3342C3H63.1302.3553C3H84.08562.9184C4H87.34784.8524C4H10輕質(zhì)油11.11367.9382C5~C11汽油51.72236.9460C11?C18柴油84.13660.09852.1749(熱損失)合計182.1038182.1038第四章煤直接液化主要設(shè)備煤直接液化是在高壓和比較高的溫度下的加氫過程,所以工藝設(shè)備及材料必須具有耐高壓、以及臨氫條件下耐氫腐蝕等性能。另外,直接液化處理的物料含有煤及催化劑等固體顆粒,因此,還要解決由于處理固體顆粒所帶來的沉積、磨損、密封等技術(shù)問題。在此對一些關(guān)鍵設(shè)備作以簡要介紹。4.1高壓煤漿泵高壓煤漿泵的作用是把煤漿從常壓送人高壓系統(tǒng)內(nèi),除了有壓力要求外,還必須達(dá)到所要求的流量。煤漿泵一般選用的往復(fù)式高壓柱塞泵,小流量可用單柱塞或雙柱塞,大流量情況下要用多柱塞并聯(lián)。柱塞材料必須選用高硬度的耐磨材料。柱塞泵的進(jìn)出口煤漿止逆閥的結(jié)構(gòu)形式必須適應(yīng)煤漿中固體顆粒的沉積和磨損,這是必須解決的技術(shù)問題。由于柱塞在往復(fù)運動時內(nèi)部為高壓而外部為常壓,因此密封問題也要得以解決,一般采用中間有油壓保護(hù)的填料密封。荷蘭生產(chǎn)的隔膜柱塞泵應(yīng)用于煤漿輸送是成功的。4.2煤漿預(yù)熱器煤漿預(yù)熱器的作用是在煤漿進(jìn)人反應(yīng)器前,把煤漿加熱到接近反應(yīng)溫度。采用的加熱方式小型裝置采用電加熱,大型裝置采用加熱爐。由于煤漿在升溫過程中的翁度變化很大(尤其是煙煤煤漿),在300~400C范圍內(nèi),煤漿鉆度隨溫度的升高而明顯上升。在加熱爐管內(nèi),煤漿貓度升高后,一方面爐管內(nèi)阻力增大,另一方面流動型式成為層流,即靠近爐管管壁的煤漿流動十分緩慢。這時如果爐管外壁熱強度較大,溫度過高,則管內(nèi)煤漿很容易局部過熱而結(jié)焦,導(dǎo)致爐管堵塞。解決上述間題的措施是一方面使循環(huán)氫與煤漿合并進(jìn)人頂熱器,由于循環(huán)氣體的擾動作用,使煤漿在爐管內(nèi)始終處于湍流狀態(tài)。另一方面是在不同溫度段選用不同的傳熱強度,在低溫段可選擇較高的傳熱強度,即可利用輻射傳熱,而在煤漿溫度達(dá)到300C以上的高溫段,必須降低傳熱強度,使?fàn)t管的外壁溫度不致過高,建議利用對流傳熱。另外選擇合適的爐管材料也能減少煤漿在爐管內(nèi)的結(jié)焦。對于大規(guī)模生產(chǎn)裝置,煤漿加熱爐的爐管需要并聯(lián),此時,為了保證每一支路中的流量一致,最好每一路爐管配一臺高壓煤漿泵。還有一種解決預(yù)熱器結(jié)焦堵塞的辦法是取消單獨的預(yù)熱器,煤漿僅通過高壓換熱器升溫至300C以下就進(jìn)人反應(yīng)器,靠加氫反應(yīng)放熱和對循環(huán)氣體加熱使煤漿在反應(yīng)器內(nèi)升至反應(yīng)所需的溫度。煤漿加熱爐的設(shè)計參數(shù)選擇可參照石油煉制加熱爐的設(shè)計經(jīng)驗。煤漿加熱爐的熱負(fù)荷計算可以將熱效應(yīng)分解成以下幾部分。煤粉升溫所需的顯熱。煤粉受熱分解所需的反應(yīng)熱(吸熱,參考值:550~580kJ/kg)溶劑升溫所需的顯熱。溶劑中輕組分蒸發(fā)所需的潛熱。與煤漿一起進(jìn)入的氫氣升溫所需的顯熱。有關(guān)數(shù)據(jù)可查閱有關(guān)手冊。還有煤的自由基碎片有少部分加氫放出的反應(yīng)熱,反應(yīng)熱數(shù)值參見下一節(jié)。煤直接反應(yīng)器的技術(shù)特點反應(yīng)器是煤直接液化工藝的核心設(shè)備,其處理的物料包括氣相氫、液相溶劑、少量的催化劑和固體煤粉,物料固體含量高,煤漿濃度為 40%-50%屬于高固含量的漿態(tài)物料;而在反應(yīng)條件下,氣、液體積流量之比為8?13[2]。這種高固含率和高氣液操作比使得煤直接液化反應(yīng)體系成為一個復(fù)雜的多相流動體系。一般來說,煤液化反應(yīng)器的操作條件都是高溫、高壓。煤液化工藝不同,相應(yīng)的操作條件也不同,一般煤直接液化反應(yīng)器的操作條件如下[3]:壓力/MPa15?30溫度/r440?465氣液比(標(biāo)態(tài)V/V)700?1000停留時間/h1?2氣含率/%0.1?0.5進(jìn)出料方式下部進(jìn)料、上部出料在煤液化反應(yīng)器內(nèi)進(jìn)行著復(fù)雜的化學(xué)反應(yīng)過程,主要有煤的熱解反應(yīng)和熱解產(chǎn)物的加氫反應(yīng),前者是吸熱反應(yīng),后者是強放熱反應(yīng),而總的熱效應(yīng)是放熱反應(yīng)[a}。因此反應(yīng)器的溫度一般要求嚴(yán)格控制,低于正常溫度則反應(yīng)不完全,其未反應(yīng)的生煤將進(jìn)入后續(xù)單元,給后續(xù)單元造成更大的操作負(fù)荷和難度;而反應(yīng)溫度過高,則容易使液化油氣化,導(dǎo)致操作不穩(wěn)定,油收率降低,也容易導(dǎo)致反應(yīng)器結(jié)焦,減少了反應(yīng)器的有效體積和物料在反應(yīng)器內(nèi)的停留時間,甚至導(dǎo)致反應(yīng)中斷。煤直接液化反應(yīng)器在實踐中應(yīng)用時,必須考慮以下4個因素:保證足夠的反應(yīng)時間,主要是液相停留時間,為此,反應(yīng)器內(nèi)氣含率不能太高。有足夠的液相上升速度,目的是防!卜煤粉顆粒的沉降。保證足夠的傳質(zhì)速率,需要有足夠和均勻的氣含率及氣、液湍流程度。有合理的反應(yīng)熱移出手段,這樣可以靈敏地控制反應(yīng)溫度,防!卜反應(yīng)器飛溫。在煤液化反應(yīng)器的操作過程中,經(jīng)常出現(xiàn)如下問題:①飛溫,當(dāng)反應(yīng)器溫度控制不好時,反應(yīng)器內(nèi)溫度就會急劇上升,失去控制,這就是飛溫現(xiàn)象,應(yīng)當(dāng)盡量避免該現(xiàn)象的發(fā)生;②固體顆粒沉積,當(dāng)反應(yīng)器內(nèi)液相上升速度低時,就會產(chǎn)生煤粉及無機顆粒的沉積,沉積不僅能導(dǎo)致反應(yīng)器內(nèi)部物料的堵塞,還會因局部反應(yīng)劇烈而產(chǎn)生飛溫現(xiàn)象;③結(jié)焦,當(dāng)反應(yīng)器內(nèi)液體流動有死區(qū)、煤漿濺上氣體空腔壁或飛溫超過470C時縮聚反應(yīng)成為主要反應(yīng)時,反應(yīng)器內(nèi)就會產(chǎn)生結(jié)焦,結(jié)焦嚴(yán)重時會導(dǎo)致反應(yīng)器正常操作無法進(jìn)行[2]。為了盡量減少以上異常情況的發(fā)生,除嚴(yán)格遵守操作規(guī)程外,增加反應(yīng)器的操作彈性也是很有必要的。為了盡量減少以上異常情況的發(fā)生,除嚴(yán)格遵守操作規(guī)程外,增加反應(yīng)器的操作彈性也是很有必要的。煤直接液化反應(yīng)器的類型自從1913年德國的Bergius發(fā)明煤直接液化技術(shù)以來,德國、美國、日本、前蘇聯(lián)等國家已經(jīng)相繼開發(fā)了幾十種煤液化工藝,所采用的反應(yīng)器的結(jié)構(gòu)也各不一樣。總的來說,迄今為止,經(jīng)過中試和小規(guī)模工業(yè)化的反應(yīng)器主要有 3種類型:鼓泡床反應(yīng)器,懸浮床反應(yīng)器,環(huán)流反應(yīng)器。
441鼓泡床反應(yīng)器氣液鼓泡床反應(yīng)器以其良好的傳熱、傳質(zhì)、相間充分接觸與高效率的可連續(xù)操作特性,而廣泛應(yīng)用于有機化工、煤化工、生物化工、環(huán)境工程等生產(chǎn)過程 ⑸。鼓泡床反應(yīng)器結(jié)構(gòu)簡單,其外形為細(xì)長的圓筒,其長徑比一般為 18?3Q里面除必要的管道進(jìn)出口外,無其他多余的構(gòu)件。為達(dá)到足夠的停留時間,同時有利于物料的混合和反應(yīng)器的制造,通常用幾個反應(yīng)器串聯(lián)。氫氣和煤漿從反應(yīng)器底部進(jìn)入,反應(yīng)后的物料從上部排出。由于反應(yīng)器內(nèi)物料的流動形式為平推流(即活塞流),理論上完全排除了返混現(xiàn)象,實際應(yīng)用中大直徑的鼓泡床反應(yīng)器液相有輕微的返混, 因此也有稱該種反應(yīng)器為活塞流反應(yīng)器的管道進(jìn)出口外,無其他多余的構(gòu)件。為達(dá)到足夠的停留時間,同時有利于物料的混合和反應(yīng)器的制造,通常用幾個反應(yīng)器串聯(lián)。氫氣和煤漿從反應(yīng)器底部進(jìn)入,反應(yīng)后的物料從上部排出。由于反應(yīng)器內(nèi)物料的流動形式為平推流(即活塞流),理論上完全排除了返混現(xiàn)象,實際應(yīng)用中大直徑的鼓泡床反應(yīng)器液相有輕微的返混,因此也有稱該種反應(yīng)器為活塞流反應(yīng)器⑹。日本液化工藝和德國液化工德國在二戰(zhàn)前的工藝(IG)和新工藝(IGOR)、日本的藝鼓泡床反應(yīng)器是典型的液化鼓泡床反應(yīng)器,其結(jié)構(gòu)如圖 德國在二戰(zhàn)前的工藝(IG)和新工藝(IGOR)、日本的NEDOL工藝、美國的SRC和相對而言它是3種反應(yīng)器中相對而言它是3種反應(yīng)器中最為成熟的一種日本新能源開發(fā)機構(gòu)組織了10家公司合作,開發(fā)了NEDO液化工藝,在日本鹿日本新能源開發(fā)機構(gòu)組織了島建成了150t/<1d成了1個印尼煤種和1個日本煤種的連續(xù)運行試驗。NEDOIX藝反應(yīng)器底部為半球形,由于長期運轉(zhuǎn)后,反應(yīng)器底部有大顆粒的沉積現(xiàn)象,因此反應(yīng)器底部設(shè)有定期排渣口,定期排除沉積物。德國IG公司二戰(zhàn)前通過工業(yè)試驗發(fā)現(xiàn),用某些褐煤做液化試驗時,第一反應(yīng)器運行幾個星期后,反應(yīng)器就會因為堵塞而停下來,里面積聚了大量的2?4mm勺固體。經(jīng)過分析,發(fā)現(xiàn)固體主要是礦物質(zhì),而沒有新鮮煤,后來他們在反應(yīng)器的圓錐底部進(jìn)料口的旁邊安裝了排渣口,才解決了堵塞問題。另外他們也發(fā)現(xiàn),鼓泡床反應(yīng)器內(nèi)影響流體流動的內(nèi)構(gòu)件,特別是其形狀易截留固體的構(gòu)件越少,反應(yīng)器操作就越平穩(wěn)。因此,工業(yè)化鼓泡床反應(yīng)器實際上是空筒。德國煤炭研究公司于1981年在魯爾區(qū)建成200t/d的中試裝置。試驗從1981年開始至1987年初結(jié)束,加煤運轉(zhuǎn)時間21700h,平均可達(dá)4000h/a以上,對反應(yīng)器的研究取得了重大突破。強制循環(huán)懸浮床反應(yīng)器該種反應(yīng)器因內(nèi)部有循環(huán)杯,并帶有循環(huán)泵,因此稱為強制循環(huán)懸浮床反應(yīng)器。應(yīng)用該種反應(yīng)器的煤液化工藝主要有美國的 H-Coal工藝、HTI液化工藝、中國神華煤液化工藝等[10]。因H-Coal工藝反應(yīng)器內(nèi)催化劑呈沸騰狀態(tài),因此也稱之為沸騰床反應(yīng)器。H-Coal工藝反應(yīng)器結(jié)構(gòu)如圖3所示,中國神華煤液化工藝反應(yīng)器結(jié)構(gòu)如圖4所示。美國HRI公司借用H-Oil重油加氫反應(yīng)器的經(jīng)驗將其用于H-Coal煤液化工藝,使用Co/Mo催化劑,只要催化劑不粉化,就呈沸騰狀態(tài)保持在床層內(nèi),不會隨煤漿流出,解決了煤炭液化過去只能用一次性鐵催化劑,不能用高活性催化劑的難題。為了保證固體顆粒處于流化狀態(tài),底部可用機械攪拌或循環(huán)泵協(xié)助。另外,為保證催化劑的數(shù)量和質(zhì)量,一方面要排出部分催化劑再生,另一方面要補充一定量的新催化劑[10]。HRI公司采用圖3所示的強制懸浮床反應(yīng)器建立了220t/d的中試裝置,反應(yīng)器直徑1.5m,高約10m該裝置第一次投煤試驗是1980年5月,用的是Kentucky11號煤,由于其他設(shè)備出了故障,只運行19h便停了下來。經(jīng)過改造后該裝置于1981年和1982年間又進(jìn)行了幾次試驗,采用的煤種是Illinois6號煤,最長運行時間是132天,成效顯著[11]。中試反應(yīng)器的試驗條件為:工藝條件。溫度450C,壓力16?19MPa循環(huán)油:煤為1.5?2.0物料空速0.5?2kg/(kg.h)。反應(yīng)器內(nèi)物料性質(zhì)。煤漿中含煤質(zhì)量分?jǐn)?shù) 9%?22%;煤漿流速為(2.1?5.5)3310mW/A氣體流速為((1.2?4.9) 10m人物料的密度為0.6?0.7g/<m;;物2料的黏度為(0.2 ?0.5) 10g/(cm?s)。在中試試驗的同時,HRI公司與Bechtel工程公司等合作進(jìn)行了2500t/d工業(yè)示范裝置的設(shè)計。我國神華集團(tuán)借鑒美國HTI液化工藝反應(yīng)器,開發(fā)了神華煤液化反應(yīng)器,也有人稱這種反應(yīng)器為外循環(huán)全返混反應(yīng)器。采用循環(huán)泵外循環(huán)方式增加循環(huán)比,以保證在一定的反應(yīng)器容積下,達(dá)到一個滿意的生產(chǎn)能力和液化效果。該種反應(yīng)器采用北京煤炭科學(xué)研究總院開發(fā)的“863”高效催化劑,催化劑與煤漿一起從反應(yīng)器底部加入,然后和反應(yīng)后的物料一起從反應(yīng)器上部排出。神華集團(tuán)采用該反應(yīng)器于2004年在上海建立6t/d規(guī)模的液化中試裝置,反應(yīng)器為2個串聯(lián)。該裝置進(jìn)行了4次投煤運轉(zhuǎn)試驗,累計投煤時間為4375h消耗原煤量1319.61t在反應(yīng)器的穩(wěn)定運轉(zhuǎn)與優(yōu)化操作方面取得了豐富的經(jīng)驗。神華集團(tuán)在內(nèi)蒙古建設(shè)的煤直接液化工業(yè)示范裝置采用的該種反應(yīng)器,規(guī)模達(dá)到了6000t/d。2個反應(yīng)器的直徑均為4.34m,高度分別為41和43m該種反應(yīng)器生產(chǎn)能力大,氣體滯留少,不容易形成大顆粒沉積物,不足的是尚未經(jīng)過長周期運行的證實[1]。環(huán)流反應(yīng)器環(huán)流反應(yīng)器是在鼓泡床反應(yīng)器的基礎(chǔ)上發(fā)展起來的一種高效多相反應(yīng)器,具有結(jié)構(gòu)簡單、傳質(zhì)性能好、易于工程放大的特點,在化學(xué)工程和其他相關(guān)領(lǐng)域中有廣泛的應(yīng)用[12]。環(huán)流反應(yīng)器型式多樣,種類繁多,其中氣升式內(nèi)環(huán)流反應(yīng)器是常用的一種。這種反應(yīng)器利用進(jìn)料氣體在液體中的相對上升運動,產(chǎn)生對液體的曳力,使液體也向上運動,或者說利用導(dǎo)流筒內(nèi)外的氣含率不同而引起的壓強差,使液體產(chǎn)生循環(huán)運動[13]。氣升式內(nèi)環(huán)流有2種類型,中心進(jìn)料環(huán)流反應(yīng)器結(jié)構(gòu)如圖5所示,環(huán)隙進(jìn)料環(huán)流反應(yīng)器結(jié)構(gòu)如圖6所示。是完全可行的。的煤液化裝置進(jìn)行改2007年12月,煤炭科學(xué)研究總院聯(lián)合神華集團(tuán)對6t/<d的煤液化裝置進(jìn)行改造,將2個串聯(lián)的反應(yīng)器中的第1個反應(yīng)器改造成大概結(jié)構(gòu)如圖5所示的環(huán)流反應(yīng)器,第2個反應(yīng)器仍然是強制循環(huán)懸浮床反應(yīng)器。在和2個反應(yīng)器都是懸浮床相同的試驗條件下進(jìn)行了將近1個月的投煤試驗,環(huán)流反應(yīng)器試驗結(jié)果與強制循環(huán)懸浮床反應(yīng)器的試驗結(jié)果對比見表2。表1環(huán)流與強制循環(huán)試驗結(jié)果對比(干燥無灰基) [2]%第一反應(yīng)器操作模式強制循環(huán)環(huán)流實際油收率(含CH4+49.0848.37水10.8311.65GC36.676.96COx2.572.08H2S0.150.17氣產(chǎn)率9.399.21H2耗4.214.26轉(zhuǎn)化率85.1987.95從表1可看出環(huán)流反應(yīng)器煤轉(zhuǎn)化率略高一些,但油收率略低于強制循環(huán)反應(yīng)器,而總的來說差別不大。試驗從工業(yè)實踐上證明了環(huán)流反應(yīng)器應(yīng)用于煤炭直接液化體系的可行性,但在放大設(shè)計、優(yōu)化設(shè)計及理論研究方而仍需要做進(jìn)一步的深入研究。444種煤液化反應(yīng)器的比較鼓泡床反應(yīng)器內(nèi)部構(gòu)件少,氣含率高,有足夠的氣液傳質(zhì)速度,而目—比較成熟,風(fēng)險小。缺點主要有2個:①液相速度偏低,接近或低于顆粒沉降速度,使反應(yīng)器內(nèi)固體濃度較高,長時間運轉(zhuǎn)會出現(xiàn)固體沉降問題,需要定期排渣 ;②由于流體動力的限制,生產(chǎn)規(guī)模不能太大,一般認(rèn)為,最大處理量為 2500t/d。強制循環(huán)懸浮床反應(yīng)器優(yōu)點是液相速度高,克服了顆粒沉降問題。氣含率低于鼓泡床,達(dá)到比較適中的數(shù)值,既保證了傳質(zhì)速度,又增加了液相停留時間。另外,由于有大量高溫循環(huán)物料與新鮮進(jìn)料的混合,使反應(yīng)熱可以通過降低進(jìn)料溫度的辦法移出。該反應(yīng)器的缺點是必須配備能在高溫高壓條件下運行的循環(huán)泵,以及反應(yīng)器頂部必須有提供氣液分離的空間及構(gòu)件。這就不僅使反應(yīng)器內(nèi)部構(gòu)件復(fù)雜化,而目 _反應(yīng)器的氣液比不能過高,否則氣液分離不完全,易引起循環(huán)泵抽空等一系列問題。環(huán)流反應(yīng)器的主要優(yōu)點是反應(yīng)器內(nèi)流體定向流動,環(huán)流液速較快,實現(xiàn)了全返混模式,而目_不會發(fā)生固體顆粒的沉積;氣體在其停留時間內(nèi)所通過的路徑長,氣體分布更均勻,單位反應(yīng)器體積的氣泡比表面積大,因此相間接觸好,傳質(zhì)系數(shù)也較大。與強制循環(huán)懸浮床反應(yīng)器比,省去了循環(huán)泵和復(fù)雜的內(nèi)構(gòu)件,減少了操作費用和因循環(huán)泵故障而引起的運轉(zhuǎn)風(fēng)險。因此環(huán)流反應(yīng)器在煤液化領(lǐng)域具有廣泛的應(yīng)用前景,應(yīng)得到足夠的重視。以上3種反應(yīng)器雖有一些區(qū)別,但本質(zhì)上有許多共同點,如化學(xué)反應(yīng)過程相同,漿體都處于流動狀態(tài),溫度、壓力和停留時間等也十分接近,主要區(qū)別是返混程度不同和循環(huán)比不同,有的單靠高壓泵和氫氣的推動,有的除此外還需要借助循環(huán)泵或?qū)Я魍?。第五章煤炭液化產(chǎn)品的處理煤炭直接液化工藝所生產(chǎn)的液化粗油, 保留了液化原料煤的一些性質(zhì)特點,芳烴含量高,氮、氧雜原子含量高,色相與儲藏穩(wěn)定性差等,如要得到與石油制品一樣的品質(zhì),必須要進(jìn)行提質(zhì)加工。但是,由于液化油的性質(zhì)與石油有很大的差異,因此液化油的提質(zhì)加工與石油相比,需要更苛刻的提質(zhì)加工條件,也需要開發(fā)針對液化油特性的催化劑和加工工藝。表5-1為液化油汽油餾分與石油汽油餾分性質(zhì)的比較,表5-2為液化油柴油餾分與石油柴油餾分性質(zhì)的比較。表5-1液化油汽油餾分與石油汽油餾分性質(zhì)的比較項目液化油石油GBO/%質(zhì)量分?jǐn)?shù))2.20<1504S/10(質(zhì)量分?jǐn)?shù))5603006N/10(質(zhì)量分?jǐn)?shù))300010膠質(zhì)/(啞/100ml)1500<5辛烷值(RON5665?70>90表5-2液化油柴油餾分與石油柴油餾分性質(zhì)的比較項目液化油石油GBO/%質(zhì)量分?jǐn)?shù))1.30<5004S/10(質(zhì)量分?jǐn)?shù))100130006N/10(質(zhì)量分?jǐn)?shù))650040>45十六烷值14565.1煤液化粗油的性質(zhì)表5-1-1為中國的依蘭煤在NEDO工藝上的液化油性質(zhì)表。表5-1-1NEDOL依蘭煤液化油性質(zhì)
項目餾分分析/C相對密度40C元素分析/%(質(zhì)量分?jǐn)?shù))IBP10%50%70%90%EPCHN1 O) S輕質(zhì)石51741391631791900.78582.4212.870.524.130.06重質(zhì)石1992042062082122490.91884.8510.010.774.340.03常壓輕2162252262282312460.91786.5610.460.852.110.02常壓重2552662883143713800.96688.849.780.700.650.03從以上表格可以看出,對煤液化粗油的性質(zhì)作一準(zhǔn)確的描述是比較困難的,但可以概括出一些特性。煤液化粗油的雜原子含量非常高。氮含量范圍為0.2%?2.0%,典型的氮含量在0.9%?1.1%(質(zhì)量分?jǐn)?shù))的范圍內(nèi),是石油氮含量的數(shù)倍至數(shù)十倍,雜原子氮可能以咔唑、氮雜菲、和氮雜螢蕙的形式存在。硫含量范圍從0.05%?2.5%,不過一般為0.3%?0.7%(質(zhì)量分?jǐn)?shù)),低于石油的平均硫含量,大部分以苯并噻吩和二苯并噻吩衍生物的形態(tài)存在。煤液化粗油中的氧含量范圍可以從 1.5%(質(zhì)量分?jǐn)?shù))一直到7%質(zhì)量分?jǐn)?shù))以上,具體取決于煤種和液化工藝,一般在 4%-5%質(zhì)量分?jǐn)?shù))。有在線加氫或離線加氫的液化工藝,由于液化粗油經(jīng)過了一次加氫精制,液化粗油中的雜原子含量大為降低。煤液化粗油中的灰含量取決于固液分離方法,采用旋流分離、離心分離、溶劑萃取沉降分離的液化粗油中含有灰,這些灰在采用催化劑的提質(zhì)加工過程中,會引起嚴(yán)重的問題。采用減壓蒸餾進(jìn)行固液分離的液化粗油中不含灰。液化粗油中的金屬元素種類與含量與煤種和液化催化劑有很大關(guān)系,一般含有鐵、鈦、硅和鋁。煤液化粗油的餾分分布與煤種和液化工藝關(guān)系很大,一般分為輕油 (又可分為輕石腦油:初溜點?82C和重石腦油82?180C,占液化粗油的15%-30%(質(zhì)量分?jǐn)?shù))、中油(180?350E,占50%?60%質(zhì)量分?jǐn)?shù))、重油(350?500E或540E),占10%?20%(質(zhì)量分?jǐn)?shù))。煤液化粗油中的烴類化合物的組成廣泛,含有60%?70%(質(zhì)量分?jǐn)?shù))的芳香族化合物,通常含有1?6環(huán),有較多的氫化芳香烴。飽和烴含量約25%(質(zhì)量分?jǐn)?shù)),一般不超過4個碳的長度。另外還有10%(質(zhì)量分?jǐn)?shù))左右的烯烴。煤液化粗油中的瀝青烯含量,對液化粗油的化學(xué)和物理性質(zhì)有顯著的影響。瀝青烯的分子量范圍為300?1000,含量與液化工藝有很大關(guān)系,如溶劑萃取工藝的液化粗油中的瀝青烯含量高達(dá)25%(質(zhì)墾分?jǐn)?shù))。5.2液化粗油提質(zhì)加工液化粗油是一種十分復(fù)雜的烴類化合物混合體系。液化粗油的復(fù)雜性在對其進(jìn)行提質(zhì)加工生產(chǎn)各種產(chǎn)品時帶來許多間題,往往不能簡單地采用石油加工的方法,需要針對液化粗油的性質(zhì),專門研究開發(fā)適合液化粗油性質(zhì)的工藝,包括催化劑。液化粗油的提質(zhì)加工一般以生產(chǎn)汽油、柴油和化工產(chǎn)品(主要為BTX)為目的。目前液化粗油提質(zhì)加工的研究,大部分都停留在實驗室的研究水平,采用石油系的催化劑。煤液化石腦油餾分的加工煤液化石腦油餾分約占煤液化油的15%?30%,有較高的芳烴潛含量,鏈烷烴僅占20流右,是生產(chǎn)汽油和芳烴(BTX)的合適原料。但煤液化石腦油餾分含有較多的雜原子(尤其是氮原子),必須經(jīng)過十分苛刻的加氫才能脫除,加氫后的石腦油餾分經(jīng)過較緩和的重整即可得到高辛烷值汽油和豐富的芳烴原料。表5-2-1為幾種液化工藝的石腦油餾分加氫和重整結(jié)果。采用石油系Ni-Mo、Co-Mo、Ni-W型催化劑和比石油加氫苛刻得多的條件下,可6以將煤液化石腦油餾分中的氮含量降至106以下,但帶來的嚴(yán)重問題是催化劑的壽命和反應(yīng)器的結(jié)焦間題。由于煤液化石腦油餾分中氮含量高,有些煤液化石腦油餾分中6氮含量高達(dá)5000?800010,研究開發(fā)耐高氮加氫催化劑是十分必要的,另外對煤液化石腦油餾分脫酚和在加氫反應(yīng)器前增加裝有特殊形狀填料的保護(hù)段來延長催化劑壽命也是有效的方法。煤液化重油的加工煤液化重油餾分的產(chǎn)率與液化工藝有很大關(guān)系,一般占液化粗油的 10%?20%。寫(質(zhì)量分?jǐn)?shù)),有的液化工藝這部分餾分很少。煤液化重油餾分由于雜原子、瀝青烯含量較高,加工較為困難。研究的一般加工路線是與中油餾分混合共同作為加氫裂化的原料和與中油餾分混合作為FCO?料。除此以外,主要用途只能作為鍋爐燃料。煤液化中油和重油混合經(jīng)加氫裂化可以制取汽油。加氫裂化催化劑對原料中的雜原子含量及金屬鹽含量較為敏感。因此,在加氫裂化前必須進(jìn)行深度加氫來除去這些催化劑的敏感物。煤液化中油和重油混合加氫裂化采用的工藝路線為2個加氫系統(tǒng):第一個系統(tǒng)為原料的預(yù)加氫脫雜原子和金屬元素,反應(yīng)條件較為緩和,催化劑為UOP-DC酈二個加氫系統(tǒng)為加氫裂化,采用2個反應(yīng)器串聯(lián),進(jìn)行深度加氫裂化,裂化產(chǎn)物中>190C的餾分油在第二個加氫系統(tǒng)中循環(huán),最終產(chǎn)物全部為<1900的汽油。表5-3-1為預(yù)加氫和加氫裂化的條件和結(jié)果。煤液化中油和重油混合后采用催化裂化(FCC)的方法也可制取汽油。美國在研究煤液化中油餾分的催化裂化時發(fā)現(xiàn):煤液化中油和液化重油混合物作為FCC原料,在工藝上要實現(xiàn)與石油原料一樣的積炭率,必須要對液化原料進(jìn)行預(yù)加氫,要求 FCC原料中的氫含量必須高于11%(質(zhì)量分?jǐn)?shù))。這樣,對煤液化中油和液化重油混合物的加氫成為必不可少,而且要有一定的深度,即使這樣,煤液化中油和液化重油混合物的催化裂化的汽油收率還只有50%(體積分?jǐn)?shù))以下,低于石油重油催化裂化的汽油收率70%(體積分?jǐn)?shù))。5.3液化粗油提質(zhì)加工工藝液化粗油提質(zhì)加工的研究工作除日本以外,目前大部分停留在實驗室的研究階段,距工業(yè)化應(yīng)用還有一定距離。日本的液化粗油提質(zhì)加工工藝日本政府從1973年開始實施陽光計劃,開始煤炭直接液化技術(shù)的系統(tǒng)研究開發(fā)。在新能源產(chǎn)業(yè)技術(shù)綜合開發(fā)機構(gòu)(NEDO的主持下,成功開發(fā)了煙煤液化工藝(NEDOL工藝,150t/dPP裝置規(guī)模)和褐煤液化工藝(BCL工藝,50t/dPP裝置規(guī)模),同時把液化粗油的提質(zhì)加工工藝研究列人計劃。1990年在完成了實驗室基礎(chǔ)研究的同時,開始設(shè)計建設(shè)50桶/d規(guī)模的液化粗油提質(zhì)加工中試裝置。目前該裝置已在日本的秋田縣建成,以煙煤液化工藝(NEDQL工藝,150t/dPP裝置規(guī)模)和褐煤液化工藝(BCL工藝,50t/dPP裝置規(guī)模)的液化粗油為原料,正在進(jìn)行液化粗油提質(zhì)加工的運轉(zhuǎn)研究,預(yù)計2002年3月研究結(jié)束。日本液化粗油提質(zhì)加工工藝流程描述。日本液化粗油提質(zhì)加工工藝流程由液化粗油全餾分一次加氫部分、一次加氫油中煤、柴油餾分的二次加氫部分、一次加氫油中石腦油餾分的二次加氫部分、二次加氫石腦油餾分的催化重整部分等4個部分構(gòu)成。在一次加氫部分,將全餾分液化粗油,通過加料泵升壓, _與以氫氣為主的循環(huán)氣體混合,在加熱爐內(nèi)預(yù)熱后,送人一次加氫反應(yīng)器。一次加氫反應(yīng)器為固定床反應(yīng)器,采用Ni/W系催化劑進(jìn)行加氫反應(yīng)。加氫后的液化粗油經(jīng)氣液分離后,
溫馨提示
- 1. 本站所有資源如無特殊說明,都需要本地電腦安裝OFFICE2007和PDF閱讀器。圖紙軟件為CAD,CAXA,PROE,UG,SolidWorks等.壓縮文件請下載最新的WinRAR軟件解壓。
- 2. 本站的文檔不包含任何第三方提供的附件圖紙等,如果需要附件,請聯(lián)系上傳者。文件的所有權(quán)益歸上傳用戶所有。
- 3. 本站RAR壓縮包中若帶圖紙,網(wǎng)頁內(nèi)容里面會有圖紙預(yù)覽,若沒有圖紙預(yù)覽就沒有圖紙。
- 4. 未經(jīng)權(quán)益所有人同意不得將文件中的內(nèi)容挪作商業(yè)或盈利用途。
- 5. 人人文庫網(wǎng)僅提供信息存儲空間,僅對用戶上傳內(nèi)容的表現(xiàn)方式做保護(hù)處理,對用戶上傳分享的文檔內(nèi)容本身不做任何修改或編輯,并不能對任何下載內(nèi)容負(fù)責(zé)。
- 6. 下載文件中如有侵權(quán)或不適當(dāng)內(nèi)容,請與我們聯(lián)系,我們立即糾正。
- 7. 本站不保證下載資源的準(zhǔn)確性、安全性和完整性, 同時也不承擔(dān)用戶因使用這些下載資源對自己和他人造成任何形式的傷害或損失。
最新文檔
- 個人蔬菜采購合同范本
- 2025年晴綸棉項目可行性研究報告
- 2025年度智能家居系統(tǒng)授權(quán)及售后服務(wù)合同
- 瓦楞紙箱項目建議書寫作參考范文
- (技術(shù)規(guī)范標(biāo)準(zhǔn))高標(biāo)準(zhǔn)農(nóng)田建設(shè)項目技術(shù)標(biāo)
- 烏魯木齊外貿(mào)合同范本
- 2025年度智慧社區(qū)建設(shè)合同終止書
- 企業(yè)股權(quán)服務(wù)合同范本
- 2025年度廣告素材制作采購合同
- 2025年度汽車銷售區(qū)域代理合同
- 商業(yè)綜合體市場調(diào)研報告
- 少兒素描課件
- 天津市部分區(qū)2023-2024學(xué)年高二上學(xué)期期末考試 生物 含解析
- 《對私外匯業(yè)務(wù)從業(yè)資格》開放式測試答案
- 《保險法解讀》課件
- 非煤礦山復(fù)工復(fù)產(chǎn)安全培訓(xùn)
- 變壓器投標(biāo)書-技術(shù)部分
- 《我國跨境電子商務(wù)消費者權(quán)益保護(hù)問題研究》
- 2024九省聯(lián)考適應(yīng)性考試【甘肅省】歷史試卷及答案解析
- 四年級語文下冊第六單元【集體備課】(教材解讀+教學(xué)設(shè)計)
- 蘇教版小學(xué)信息技術(shù)五年級下冊五年級下冊教案全集
評論
0/150
提交評論