


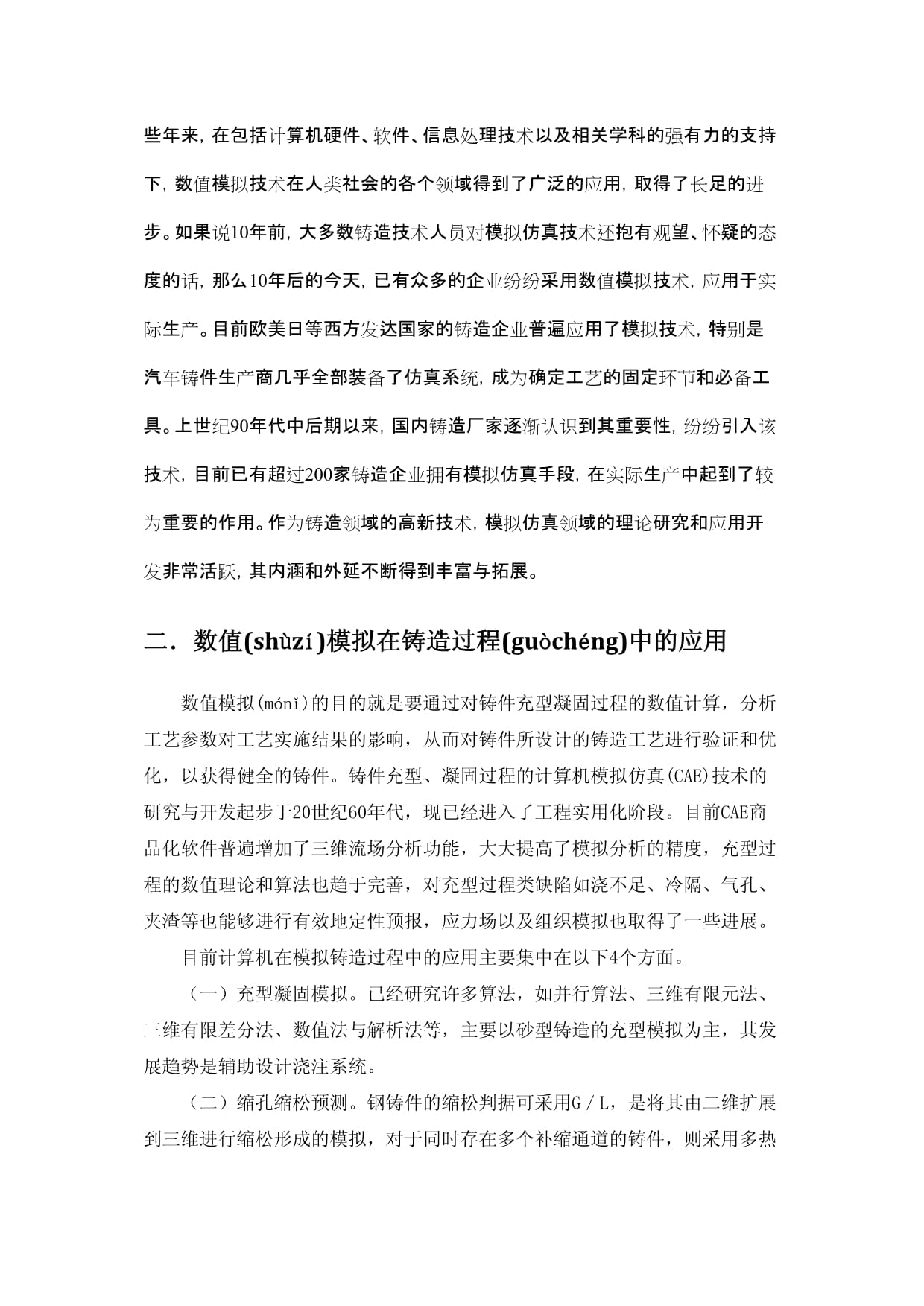

版權(quán)說明:本文檔由用戶提供并上傳,收益歸屬內(nèi)容提供方,若內(nèi)容存在侵權(quán),請進(jìn)行舉報或認(rèn)領(lǐng)
文檔簡介
1、材料(cilio)加工數(shù)值模擬論文(lnwn)專業(yè):材料(cilio)加工姓名:閆禹伯學(xué)號:2013432109目錄(ml)第一章鑄造過程(guchng)的數(shù)值模擬分析傳統(tǒng)鑄件的生產(chǎn)是根據(jù)經(jīng)驗(yàn)確定鑄造工藝,先試澆鑄,檢驗(yàn)試樣是否存在澆鑄缺陷,如有則修改工藝方案,然后重復(fù)上述過程,直至獲得合格鑄件。由于這種方法必須在澆鑄后才能(cinng)對鑄件工藝是否合理進(jìn)行評價,因而該方法存在設(shè)計周期長、生產(chǎn)成本高、效率低等缺點(diǎn);而且得到的往往不是最終鑄造工藝,對于大型或復(fù)雜形狀鑄件該缺點(diǎn)顯得更加突出。鑄造CAE模擬技術(shù)是利用計算機(jī)技術(shù)來改造(gizo)和提升傳統(tǒng)鑄造術(shù),對降低產(chǎn)品的成本、提高鑄造企業(yè)的競爭
2、力有著不可替代的作用。鑄造過程數(shù)值模擬的發(fā)展現(xiàn)狀計算機(jī)技術(shù)的飛速發(fā)展,已使其自電力發(fā)明以來最具生產(chǎn)潛力的工具之一,數(shù)字化時代正一步步向我們走來。計算機(jī)輔助設(shè)計(CAD)、計算機(jī)輔助工程分析(CAM)和計算機(jī)輔助制造(CAE)等技術(shù)在材料科學(xué)領(lǐng)域的應(yīng)用正在不斷擴(kuò)大和深入,已經(jīng)成為材料科學(xué)領(lǐng)域的技術(shù)前沿和十分活躍的研究領(lǐng)域。就鑄造領(lǐng)域而言,鑄造過程數(shù)值模擬已經(jīng)成為計算機(jī)在鑄造研究和生產(chǎn)應(yīng)用中最為核心的內(nèi)容之一,涉及鑄造理論、凝固理論、傳熱學(xué)、工程力學(xué)、數(shù)值分析、計算機(jī)圖形學(xué)等多個學(xué)科1-5,是公認(rèn)的材料科學(xué)的前沿領(lǐng)域。鑄造過程數(shù)值模擬技術(shù)經(jīng)過了四十年的發(fā)展歷程,其間,從簡單到復(fù)雜、從溫度場發(fā)展到流
3、動場、應(yīng)力場,從宏觀模擬深入到微觀領(lǐng)域,從普通的重力鑄造拓展到低壓、壓鑄等特種鑄造,從實(shí)驗(yàn)室研究進(jìn)入到工業(yè)化實(shí)際應(yīng)用。特別是近些年來,在包括計算機(jī)硬件、軟件、信息處理技術(shù)以及相關(guān)學(xué)科的強(qiáng)有力的支持下,數(shù)值模擬技術(shù)在人類社會的各個領(lǐng)域得到了廣泛的應(yīng)用,取得了長足的進(jìn)步。如果說10年前,大多數(shù)鑄造技術(shù)人員對模擬仿真技術(shù)還抱有觀望、懷疑的態(tài)度的話,那么10年后的今天,已有眾多的企業(yè)紛紛采用數(shù)值模擬技術(shù),應(yīng)用于實(shí)際生產(chǎn)。目前歐美日等西方發(fā)達(dá)國家的鑄造企業(yè)普遍應(yīng)用了模擬技術(shù),特別是汽車鑄件生產(chǎn)商幾乎全部裝備了仿真系統(tǒng),成為確定工藝的固定環(huán)節(jié)和必備工具。上世紀(jì)90年代中后期以來,國內(nèi)鑄造廠家逐漸認(rèn)識到其重
4、要性,紛紛引入該技術(shù),目前已有超過200家鑄造企業(yè)擁有模擬仿真手段,在實(shí)際生產(chǎn)中起到了較為重要的作用。作為鑄造領(lǐng)域的高新技術(shù),模擬仿真領(lǐng)域的理論研究和應(yīng)用開發(fā)非?;钴S,其內(nèi)涵和外延不斷得到豐富與拓展。二數(shù)值(shz)模擬在鑄造過程(guchng)中的應(yīng)用數(shù)值模擬(mn)的目的就是要通過對鑄件充型凝固過程的數(shù)值計算,分析工藝參數(shù)對工藝實(shí)施結(jié)果的影響,從而對鑄件所設(shè)計的鑄造工藝進(jìn)行驗(yàn)證和優(yōu)化,以獲得健全的鑄件。鑄件充型、凝固過程的計算機(jī)模擬仿真(CAE)技術(shù)的研究與開發(fā)起步于20世紀(jì)60年代,現(xiàn)已經(jīng)進(jìn)入了工程實(shí)用化階段。目前CAE商品化軟件普遍增加了三維流場分析功能,大大提高了模擬分析的精度,充型
5、過程的數(shù)值理論和算法也趨于完善,對充型過程類缺陷如澆不足、冷隔、氣孔、夾渣等也能夠進(jìn)行有效地定性預(yù)報,應(yīng)力場以及組織模擬也取得了一些進(jìn)展。目前計算機(jī)在模擬鑄造過程中的應(yīng)用主要集中在以下4個方面。(一)充型凝固模擬。已經(jīng)研究許多算法,如并行算法、三維有限元法、三維有限差分法、數(shù)值法與解析法等,主要以砂型鑄造的充型模擬為主,其發(fā)展趨勢是輔助設(shè)計澆注系統(tǒng)。(二)縮孔縮松預(yù)測。鋼鑄件的縮松判據(jù)可采用GL,是將其由二維擴(kuò)展到三維進(jìn)行縮松形成的模擬,對于同時存在多個補(bǔ)縮通道的鑄件,則采用多熱節(jié)法進(jìn)行縮孔、縮松的預(yù)測。鑄件縮孔與縮松的圖像模擬也在卓有成效地進(jìn)行。(三)凝固過程應(yīng)力模擬。主要針對鑄件殘余應(yīng)力和
6、殘余變形進(jìn)行模擬,而液固共存時應(yīng)力場數(shù)值模擬是應(yīng)力場數(shù)值模擬的核心,許多鑄造缺陷如縮松、縮孔、熱裂等都發(fā)生在此階段。由于液固共存態(tài)力學(xué)性能的測定十分困難,目前還沒有完全建立此階段的力學(xué)模型,因此仍是整個鑄造過程模擬的難點(diǎn)。國內(nèi)外不少數(shù)值模擬軟件已經(jīng)具有應(yīng)力分析的功能?,F(xiàn)階段應(yīng)力場研究大都是在自己的系統(tǒng)中借用現(xiàn)成的大型通用有限元分析軟件如ANSYS、MARC、ADINA等進(jìn)行二次開發(fā),也建立了相應(yīng)的數(shù)學(xué)模型,主要有彈性模型、彈塑性模型、粘塑性模型等。對熱裂的模擬經(jīng)過幾十年的研究,總結(jié)了影響因素和相應(yīng)的判據(jù),也提出了幾種不同的理論,但總的來說這些理論還不能進(jìn)行定量描述,尚需進(jìn)一步研究。近幾十年發(fā)展
7、起來的流變學(xué)為固液兩相區(qū)的力學(xué)行為研究拓展了新的方向,在此基礎(chǔ)上發(fā)展的流變學(xué)模型采用簡單的彈性體、粘性體和塑性體等理想的力學(xué)模型組合來表示材料復(fù)雜的流動及變形規(guī)律,從而能夠準(zhǔn)確地反映流動變形隨時間的變化規(guī)律,因此流變學(xué)的方法適合處理鑄件在凝固過程中尤其是準(zhǔn)固相區(qū)的流動及變形規(guī)律。另一種方法是將有限差分法和有限元法結(jié)合起來,利用有限差分法分析流動和傳熱,用有限元法計算應(yīng)力。(四)凝固過程微觀組織模擬。微觀組織模擬是一個(y )復(fù)雜的過程,比凝固和充型過程(guchng)模擬具有更大的困難。近年來各種微觀組織模擬方法紛紛出現(xiàn),已成為材料科學(xué)的研究熱點(diǎn)之一。這些方法雖能在一定程度上比較準(zhǔn)確地模擬合金
8、(hjn)的凝固組織,但由于實(shí)際的凝固過程比較復(fù)雜,這些方法都作了很多假設(shè),因此離實(shí)際的鑄件凝固組織模擬還有一定距離。目前主要的模擬方法有確定性模擬、隨機(jī)性模擬、相場方法、介觀尺度模擬方法等。場相法是研究直接微觀模擬的熱點(diǎn),主要的模擬模型有三種:MonteCado(MC)方法、元胞自動機(jī)模型、相場模型?,F(xiàn)有研究領(lǐng)域中球鐵的微觀組織模擬仍是主要的研究方向之一;把相圖計算并入宏觀和微觀耦合模擬中,并且同時考慮顯微組織和偏析是進(jìn)行多元合金模擬的必經(jīng)之路。三鑄造過程數(shù)值模擬在生產(chǎn)中的應(yīng)用鑄造CAE技術(shù)是根據(jù)設(shè)計出的鑄造工藝對鑄件進(jìn)行充型和凝固模擬并將模擬結(jié)果進(jìn)行可視化處理,預(yù)測鑄件可能產(chǎn)生的缺陷。目前
9、,凝固過程的溫度場模擬以及縮孔、縮松預(yù)測已經(jīng)應(yīng)用于實(shí)際的生產(chǎn)當(dāng)中。在充型、應(yīng)力分析及微觀組織等方面也取得了很大的進(jìn)展隨著鑄件結(jié)構(gòu)的日趨復(fù)雜化和大型化,對鑄件的外在和內(nèi)在質(zhì)量要求也越來越高。鑄造凝固過程的計算機(jī)模擬經(jīng)過大約40年的發(fā)展,已取得了很大的進(jìn)展,通過數(shù)值模擬和物理模擬相結(jié)合的方法,可實(shí)現(xiàn)計算機(jī)試生產(chǎn)、動態(tài)顯示工藝歷程、預(yù)測缺陷和優(yōu)化工藝。大量的商品化軟件的出現(xiàn)及其在實(shí)際生產(chǎn)中的廣泛應(yīng)用,說明了宏觀場量模擬已逐步完善,如溫度場、流場、應(yīng)力應(yīng)變場等;到目前為止,典型的商品化軟件有Ansys、LSDYN3D、Procast、ViewCast等。鑄造過程仿真模擬可以協(xié)助鑄造工藝師改進(jìn)工藝設(shè)計,
10、提高鑄件的質(zhì)量。長期以來鑄造工藝設(shè)計師就有一愿望,即在澆注之前能夠調(diào)試和改進(jìn)工藝,直到(zhdo)所設(shè)計的工藝方法能獲得高質(zhì)量的鑄件再進(jìn)行實(shí)際澆注。凝固模擬技術(shù)就有可能提供給鑄造工藝設(shè)計師這樣一個有力的工具,使其可以根據(jù)凝固模擬所顯示的可能出現(xiàn)的缺陷和位置加以改進(jìn)直至滿意為止。沒有凝固模擬這樣一個有力的工具,鑄造工藝設(shè)計師就只能先試澆,澆注完之后根據(jù)鑄件的具體情況加以改進(jìn)設(shè)計,修改模型。這樣,不僅增加了試制費(fèi)用而且延長了樣件試制周期。如果(rgu)在正常生產(chǎn)線上試制有可能影響正常生產(chǎn)。因此有的鑄造廠專設(shè)了樣件試制部門以保證樣件的質(zhì)量和進(jìn)度,但除了對正常生產(chǎn)影響小以外,試制費(fèi)用和樣件試制周期無顯
11、著改進(jìn),而且還增加投資和費(fèi)用。鑄造過程計算機(jī)模擬及優(yōu)化技術(shù)可以徹底改變鑄造工藝方案制定過程中的不確定性,確保工藝的可行性和鑄件質(zhì)量、縮短產(chǎn)品開發(fā)周期、降低成本、提高市場(shchng)應(yīng)變能力,是改善企業(yè)T(上市時間)、Q(質(zhì)量)、C(成本)、s(服務(wù))的必要手段,對提高鑄造企業(yè)的生產(chǎn)水平和競爭力具有重要的現(xiàn)實(shí)意義。鑄造生產(chǎn)出現(xiàn)的許多缺陷都與金屬凝固過程密切相關(guān),鑄件凝固過程的計算機(jī)仿真模擬,可以形象準(zhǔn)確地描述這一復(fù)雜的變化過程,顯示鑄件凝固過程中所發(fā)生的溫度變化和液固態(tài)變化,并預(yù)測出可能發(fā)生的縮孔、縮松等缺陷。仿真是材料科學(xué)與制造科學(xué)的前沿領(lǐng)域及研究熱點(diǎn)。根據(jù)美國科學(xué)研究院工程技術(shù)委員會的測
12、算,模擬仿真可提高產(chǎn)品質(zhì)量515倍、增加材料出品率25、降低工程技術(shù)成本1330、降低人工成本520、增加投入設(shè)備利用率3060、縮短產(chǎn)品設(shè)計和試制周期3O60等。四鑄造過程的計算機(jī)模擬4.1鑄件充型模擬鑄造充型過程對鑄件的最終質(zhì)量起著決定性的作用,許多鑄造缺陷如澆不足、冷隔、卷氣、氧化夾渣乃至縮松、縮孔等都與鑄造的充型過程密切相關(guān),鑄造過程計算機(jī)模擬能夠較為準(zhǔn)確的反映充型過程和缺陷生成過程,這對于優(yōu)化充型系統(tǒng)設(shè)計,避免鑄造缺陷的形成具有重要的意義。在鑄造工藝設(shè)計中,我們可以直觀地發(fā)現(xiàn)一些不合理的設(shè)計并提出工藝改進(jìn)使鑄件一次澆注成功。4.2鑄件凝固(nngg)模擬鑄造過程中大部分缺陷主要是縮松
13、和縮孔缺陷,而這些缺陷大都是在鑄件凝固(nngg)過程中形成,因而比較精確的再現(xiàn)鑄件的凝固過程對縮松和縮孔缺陷的預(yù)測顯得極為重要。鑄造過程仿真模擬能夠預(yù)測鑄件的縮松和縮孔缺陷。4.3疏松(sh sn)缺陷的預(yù)測Procast采用Niyama判據(jù)預(yù)測疏松即疏松形成的條件為M=ArbGcLd當(dāng)a=1;b=0;c=1;d=-0.5時;M=GL臨界值;判據(jù)中G為溫度梯度,L為冷卻速度,此處臨界值取10,在凝固過程中因枝晶阻礙液體金屬的流動而不能有效地補(bǔ)縮,容易產(chǎn)生疏松缺陷。4.4模擬步驟(基于procast)1、創(chuàng)建模型:可以分別用IDEAS、UG、Pro/E、PATRAN、ANSYS等作為前處理軟件
14、創(chuàng)建模型,輸出ProCAST可接受的模型或網(wǎng)格格式的文件。2、MeshCAST:對輸入的模型或網(wǎng)格文件進(jìn)行剖分,最終產(chǎn)生四面體網(wǎng)格,生成xx.mesh文件,文件中包含節(jié)點(diǎn)數(shù)量、單元數(shù)量、材料數(shù)量等信息。3、PreCAST:分配材料、設(shè)定界面條件、邊界條件、初始條件、模擬參數(shù),生成xxd.dat文件和xxp.dat文件。4、DataCAST:檢查模型及Precast中對模型的定義是否有錯誤,輸出錯誤信息,如無錯誤,將所有模型的信息轉(zhuǎn)化為二進(jìn)制,生成xx.unf文件。5、ProCAST:對鑄造過程模擬分析計算,生成xx.unf文件。6、ViewCAST:顯示鑄造過程模擬分析結(jié)果。7、PostCAS
15、T:對鑄造過程模擬分析結(jié)果進(jìn)行后處理。第二章鍛壓過程的數(shù)值(shz)模擬數(shù)值模擬技術(shù)在金屬塑性加工中的作用有兩個方面:第一,在工藝(gngy)設(shè)計和模具設(shè)計階段可以對設(shè)計進(jìn)行試運(yùn)行,并找出設(shè)計中的錯誤,將實(shí)際生產(chǎn)中的工藝修定(xi dn)和模具修改降低到最小程度;第二,在產(chǎn)品制作中可以大幅度降低制作成本。數(shù)值模擬技術(shù)可以將看不見的研究對象進(jìn)行可視化處理,因此是金屬塑性加工設(shè)計和研究的有力工具,其作用非常之大?;谟邢拊椒ǖ臄?shù)值模擬技術(shù)由于其獨(dú)特的優(yōu)勢,如適合于各種復(fù)雜的邊界以及非線性問題等,在塑性加工領(lǐng)域獲得了最廣泛的應(yīng)用。其主要目的是用來優(yōu)化工藝過程、提高質(zhì)量、縮減產(chǎn)品的研發(fā)周期以降低成本
16、及提高生產(chǎn)率。一研究背景鍛造成形是現(xiàn)代制造業(yè)中的重要加工方法之一。鍛造成形的制件有著其他加工方法難以達(dá)到的良好的力學(xué)性能。隨著科技發(fā)展, 鍛造成形工藝面臨著巨大的挑戰(zhàn),各行業(yè)對鍛件質(zhì)量和精度的要求越來越高, 生產(chǎn)成本要求越來越低。這就要求設(shè)計人員在盡可能短的時間內(nèi)設(shè)計出可行的工藝方案和模具結(jié)構(gòu)。但目前鍛造工藝和模具設(shè)計, 大多仍然采用實(shí)驗(yàn)和類比的傳統(tǒng)方法, 不僅費(fèi)時而且鍛件的質(zhì)量和精度很難提高。隨著有限元理論的成熟和計算機(jī)技術(shù)的飛速發(fā)展, 運(yùn)用有限元法數(shù)值模擬進(jìn)行鍛壓成形分析, 在盡可能少或無需物理實(shí)驗(yàn)的情況下, 得到成形中的金屬流動規(guī)律、應(yīng)力場、應(yīng)變場等信息, 并據(jù)此設(shè)計工藝和模具, 已成為
17、一種行之有效的手段。鍛造成形大多屬于三維非穩(wěn)態(tài)塑性成形, 一般不能簡化為平面或軸對稱等簡單問題來近似處理。在成形過程中, 既存在材料非線性, 又有幾何非線性, 同時還存在邊界條件非線性, 變形機(jī)制十分復(fù)雜, 并且接觸邊界和摩擦邊界也難以描述。應(yīng)用剛粘塑性有限元法進(jìn)行三維單元數(shù)值模擬, 是目前國際公認(rèn)的解決此類問題的最好方法之一。隨著有限元理論(lln)的廣泛應(yīng)用和計算機(jī)技術(shù)的快速發(fā)展,運(yùn)用有限元法數(shù)值模擬對鍛壓成形(chn xn)進(jìn)行分析, 在盡可能少或無需(wx)物理實(shí)驗(yàn)的情況下, 得到成形中的金屬流動規(guī)律、應(yīng)力場、應(yīng)變場等信息, 并據(jù)此設(shè)計成形工藝和模具, 成為提高金屬成形效率和生產(chǎn)率的行
18、之有效的手段。由于鍛造成形的制件大多屬于三維非穩(wěn)態(tài)塑性成形過程, 在成形過程中, 既存在材料非線性和幾何非線性, 同時還存在邊界條件非線性, 接觸邊界和摩擦邊界也難于描述, 因此變形機(jī)制十分復(fù)雜。應(yīng)用剛( 粘) 塑性有限元法進(jìn)行三維單元數(shù)值模擬分析是目前公認(rèn)的解決此類問題的最好方法之一。數(shù)學(xué)模型、邊界條件等是三維單元數(shù)值模擬的關(guān)鍵技術(shù)問題, 成為制約模擬結(jié)果優(yōu)劣的決定性因素, 所以研究解決這些關(guān)鍵技術(shù)成為數(shù)值模擬研究領(lǐng)域的熱點(diǎn)課題。經(jīng)過數(shù)十年的發(fā)展, 在某些方面形成了一些較成熟的方法, 但有些方面還不完善, 還需要進(jìn)一步的研究探討, 尋找更有效的解決措施。首先介紹了剛(粘) 塑性有限元法基本理
19、論基礎(chǔ), 并在此基礎(chǔ)上重點(diǎn)總結(jié)了鍛造成形數(shù)值模擬中的關(guān)鍵技術(shù), 通過列舉現(xiàn)有應(yīng)用實(shí)例, 對這些關(guān)鍵技術(shù)研究的現(xiàn)狀及存在問題作了系統(tǒng)深入分析。二鍛壓過程的數(shù)值模擬現(xiàn)狀在塑性成形中使用有限元技術(shù)進(jìn)行工藝工程數(shù)值模擬已有三十多年的歷史。在發(fā)展的初期只能實(shí)現(xiàn)一些二維的簡單模擬,而且耗時長,精度也很不如人意。三維有限元模擬在上世紀(jì)九十年代中期才興起并由于計算機(jī)技術(shù)及各種有限元求解算法的快速發(fā)展而迅速得到廣泛應(yīng)用。各種各樣的商業(yè)有限元軟件的出現(xiàn)使得在金屬塑性成形中的工藝設(shè)計及優(yōu)化領(lǐng)域達(dá)到一個前所未有的水平,是傳統(tǒng)的理論和實(shí)驗(yàn)方法所不能取得的。汽車制造領(lǐng)域最能體現(xiàn)有限元模擬技術(shù)的發(fā)展,在美國, 福特公司早于
20、1970年就采用有限元模擬技術(shù);歐洲的一些大牌汽車廠商如奔馳、雷諾、富豪等也在上世紀(jì)八十年代開始廣泛應(yīng)用有限元法;隨后日本的馬自達(dá)、豐田、尼桑等公司也開始使用。當(dāng)前有限元數(shù)值模擬技術(shù)的應(yīng)用范圍已由二維擴(kuò)展到三維,可以進(jìn)行自適應(yīng)網(wǎng)格重劃,可以分析形狀及受力非常復(fù)雜的三維幾何模型;從原來(yunli)典型的簡單工藝模擬擴(kuò)展到各種復(fù)雜的工藝模擬,可以對工藝參數(shù)和幾何參數(shù)進(jìn)行優(yōu)化計算;從宏觀分析發(fā)展到微觀分析,可以預(yù)測彈性回復(fù)、殘余應(yīng)力、加工硬化,預(yù)測工件在變形過程中的微觀組織,模擬退火、正火、淬火、回火等熱處理過程中的材料組織變化;并且還能分析一些較復(fù)雜的耦合問題(如考慮包括塑性變形功和摩擦功的熱效
21、應(yīng)在內(nèi)的熱力耦合以及考慮變形(bin xng)和相變在內(nèi)的材料組織性能演化的耦合分析等)。第三章焊接數(shù)值模擬技術(shù)的發(fā)展(fzhn)現(xiàn)狀焊接是一個涉及電弧物理(wl)、傳質(zhì)傳熱、冶金和力學(xué)的復(fù)雜過程,單純(dnchn)采用理論方法,很難準(zhǔn)確解決生產(chǎn)實(shí)際問題,而要得到一個高質(zhì)量的焊接結(jié)構(gòu),必須要控制這些因素。近20年來,隨著計算機(jī)技術(shù)的飛速發(fā)展,國內(nèi)外研究者開始用計算機(jī)對焊接進(jìn)行數(shù)值模擬研究,以此來準(zhǔn)確分析焊接中的一些現(xiàn)象。焊接數(shù)值模擬技術(shù)的發(fā)展使焊接技術(shù)有了突破性的發(fā)展。一.焊接接頭微觀組織的數(shù)值模擬在焊接過程中,快速加熱和快速冷卻都會使焊接接頭的微觀組織發(fā)生很大的變化,影響焊接接頭的性能,而這
22、些又很難用傳統(tǒng)的實(shí)驗(yàn)法和數(shù)學(xué)模型來分析。因此,人們開始應(yīng)用數(shù)值模擬技術(shù)對焊接接頭的微觀組織進(jìn)行數(shù)值模擬。焊接過程冶金分析包括焊接熔池中的化學(xué)反應(yīng)和氣體吸收、焊縫金屬的結(jié)晶、溶質(zhì)的再分配和顯微偏析、氣孔、夾渣和熱裂紋的形成、熱影響區(qū)在焊接熱循環(huán)作用下發(fā)生的相變和組織性能變化,以及氫擴(kuò)散和冷裂紋等的預(yù)測。目前用于焊接接頭微觀組織模擬的方法主要有基于概率模型的MonteCarlo(MC)方法、CellularAutomaton(CA)方法及相場法。1.1MonteCarlo(MC)方法MC方法的實(shí)質(zhì)就是采用隨機(jī)抽樣的方法來解釋物理模型。1983年,Anderson首先提出了將MC方法應(yīng)用于晶粒生長后
23、尺寸分布等方面的研究,之后Radhakrishnan和Zacharia提出了修整MC的方法,把時間引入到模擬當(dāng)中,于是,這種方法開始逐步用于焊接接頭的微觀組織模擬。最初(zuch)的MC方法(fngf),只能在等溫下模擬(mn)晶粒的成長過程。LIMY等人應(yīng)用二維MC方法模擬鎳板在激光焊過程中所形成的熱影響區(qū)的組織,發(fā)現(xiàn)在加熱、冷卻過程中,晶粒正常生長機(jī)制占很重要的地位。YANGZ等人通過變溫條件下的三維MC方法模擬工業(yè)純鈦在焊接過程中的晶粒成長情況時發(fā)現(xiàn),熱影響區(qū)表面的散熱要快很多,導(dǎo)致晶粒從表面到根部逐漸增大。最后將以前的二維模擬進(jìn)行了修正。1.2CellularAutomaton(CA)
24、方法CA法最早是由VonNeumann和Ulam作為一種可能的理想模型而提出的,是物理體的一種理想化,可以說是一種建立模型的基本方法。元胞自動機(jī)在剛剛提出的時候并未引起人們的足夠重視,直到SWolfram較為詳細(xì)地給出了元胞自動機(jī)的一些數(shù)學(xué)理論基礎(chǔ),才激發(fā)了人們對它的研究。Guillemot將CA模型與有限元(FE)模型結(jié)合,建立了一個模擬晶粒生長過程的宏觀偏析模型,模擬晶粒在無過冷時的生長情況。在我國,夏維國通過研究二維晶粒的生長動力學(xué)曲線,并分析對其生長的影響,利用CA模型模擬了晶粒的成長過程。CA法已經(jīng)普遍應(yīng)用于相變微觀組織的轉(zhuǎn)變過程中,并得到了很好的效果。1.3相場法相場法是近年來比較
25、新的一種模擬方法。研究者可以在支晶尺度上真實(shí)地模擬微觀組織的形成,并引入了新變量-相場。相場是一個序參量,表示系統(tǒng)在時間和空間上的物理狀態(tài)。例如=3代表固相區(qū),=6代表液相區(qū),在固液界面上U的值在36之間連續(xù)變化。DMarcus等人建立了三維相場模型,模擬了定向凝固過程中的晶粒生長等情況。MAZ等人應(yīng)用相場法模擬發(fā)現(xiàn),在晶粒生長過程中因素對晶體結(jié)構(gòu)變化的影響最為顯著。相場理論是建立在統(tǒng)計學(xué)基礎(chǔ)上的,相場方程的解可以很好地描述金屬系統(tǒng)固液界面的各種形態(tài)。二焊接溫度場的數(shù)值(shz)模擬焊接(hnji)過程中會產(chǎn)生溫度場,對其數(shù)值模擬的研究已廣泛應(yīng)用到焊接領(lǐng)域。焊接構(gòu)件時會出現(xiàn)(chxin)很多情
26、況,例如裂紋、凝固等。對不均勻溫度場的數(shù)值模擬,可以更好地研究其產(chǎn)生的原因及對其他性能的影響。在焊接過程中,焊接熱輸入和熱傳導(dǎo)對冶金過程、固態(tài)相變、組織性能和應(yīng)力應(yīng)變等都有著重要的影響。焊接是一個局部快速加熱到高溫,隨后快速冷卻的過程。隨著熱源的移動,整個焊件的溫度隨時間和空間急劇變化,材料的熱物理性能也隨溫度劇烈變化,同時還存在熔化和相變潛熱的現(xiàn)象。因此,焊接溫度場分析屬于典型的非線性瞬態(tài)熱傳導(dǎo)問題,焊接溫度場的數(shù)學(xué)模型基于傅里葉熱傳導(dǎo)方程。準(zhǔn)確模擬焊接溫度場的關(guān)鍵在于提供準(zhǔn)確的材料屬性、熱源模型與實(shí)際熱源的擬合程度、邊界條件是否設(shè)置恰當(dāng)以及網(wǎng)格劃分等。2.1模型的建立和方法的實(shí)施首先,建立
27、含有沿焊縫移動電弧熱的二維焊接溫度場的計算模型,考慮熱源的熱輸入和上下表面的輻射散熱,但忽略板邊的輻射熱損失和邊界條件。對TIG焊,一般都將電弧看成輻射狀對稱并呈高斯分布的二維熱流作用于工件表面。其次,熔池內(nèi)流體流動由于增加了熱傳導(dǎo)速度,對焊接過程的溫度場也有著重要的影響。近年來,熔池內(nèi)流體傳熱和流動成了研究的熱點(diǎn)并取得了很大的進(jìn)展。在焊接過程的數(shù)值模擬研究中,提出了一系列熱源模型,常用的有Rosenthal解析模型、高斯熱源模型、半球狀熱源模型、橢球形熱源模型和雙橢球形熱源模型等。Rosenthal解析模型基于以下假設(shè):熱源為點(diǎn)熱源、線熱源或面熱源;材料為固態(tài),無相變發(fā)生;材料的熱物理性能不
28、隨溫度變化;焊接構(gòu)件為無限體或半無限體。這些假設(shè)與焊接實(shí)際情況有很大出入,因此模擬結(jié)果會出現(xiàn)較大偏差。隨著對電弧物理的深入研究,焊接熱源模型不斷得到完善。Eagar和Tsai提出了將焊接加熱斑點(diǎn)上熱流密度的分布近似地用高斯數(shù)學(xué)模型來描述的方法,這種熱源分布函數(shù)在早期使用有限元方法計算焊接溫度場時應(yīng)用較多,在二維導(dǎo)熱方程計算時常將縱向熱流忽略。在電弧挺度較小、對熔池沖擊力較小的情況下,高斯分布的熱源應(yīng)用模式較準(zhǔn)確,但對高能束焊接如激光焊、電子束焊,高斯分布函數(shù)沒有考慮電弧的穿透作用,在這種情況下,AGoldak提出更為實(shí)際的一種熱源模式半球狀熱源分布函數(shù)。這種分布函數(shù)也有一定局限性,因?yàn)閷?shí)踐中熔
29、池在激光焊等情況下不是球?qū)ΨQ的,為了改進(jìn)這種模式,AGoldak提出了橢球形熱源模型。在用橢球形熱源分布函數(shù)計算時,發(fā)現(xiàn)在橢球前半部分溫度梯度不像實(shí)際中那樣陡變,而橢球的后半部分溫度梯度分布較緩。為克服這個缺點(diǎn),AGoldak提出了雙橢球熱源模型,將焊接熔池的前半部分作為一個14橢球,后半部分作為一個14橢球,焊接不同材質(zhì)時,也可將雙橢球分成4個18的橢球瓣。上述所有(suyu)熱源模型的共同點(diǎn)是忽略在焊接熔池中的復(fù)雜過程,特別是熔化和結(jié)晶過程中的熔合區(qū)移動和借助對流和熱輻射的傳熱;焊接熔池中復(fù)雜的熱過程(guchng)用導(dǎo)熱連續(xù)體中的焊接熱源加以近似。對于通常(tngchng)的焊接方法如焊
30、條電弧焊、鎢極氬弧焊,采用高斯分布的函數(shù)可以得到較滿意的結(jié)果。對于電弧沖力效應(yīng)較大的焊接方法,如等離子焊、熔化極氬弧焊和激光焊接,常采用雙橢球形熱源分布函數(shù)。為求準(zhǔn)確,還可將熱源分成兩部分,采用高斯分布的熱源函數(shù)作為表面熱源,焊件熔池部分采用雙橢球形熱源分布函數(shù)作為內(nèi)熱源。對于一些大型實(shí)際構(gòu)件因計算規(guī)模和計算量大、收斂困難,導(dǎo)致模擬仿真時出現(xiàn)各種問題。針對這種情況,清華大學(xué)的蔡志鵬等人提出了分段移動熱源和串熱源模型,從而大幅提高了計算效率。金屬材料的物理性能參數(shù)如比熱容、導(dǎo)熱系數(shù)、彈性模量、屈服應(yīng)力等一般都隨溫度的變化而變化。當(dāng)溫度變化范圍不大時,可采用材料物理性能參數(shù)的平均值進(jìn)行計算。但焊接
31、過程中,焊件局部加熱到很高的溫度,整個焊件的溫度變化十分劇烈,如果不考慮材料的物理性能參數(shù)隨溫度的變化,計算結(jié)果一定會有很大偏差。所以在焊接溫度場和應(yīng)力場的模擬計算中一定要給定材料的各項(xiàng)物理性能參數(shù)隨溫度的變化值。用有限元法對所建立的模型進(jìn)行計算,可分為3步:1.確定材料的熱物理參數(shù);2.落實(shí)邊界條件;3.區(qū)域離散化。假定采用的材料是各向同性且均勻的,其熱物理參數(shù)隨溫度而變化。為了處理可能比較大的溫度梯度,在焊縫及其附近可采用較密的網(wǎng)格。2.2溫度場的計算結(jié)果和影響不同(b tn)的潛熱處理方式對溫度場的影響很大。與假定潛熱在固液相線間以恒定速率釋放的計算結(jié)果相比,實(shí)測(sh c)方法計算出的
32、熔池尺寸相對較窄,但對低溫處的溫度影響不大。熔池內(nèi)的對流傳熱加快(ji kui)了傳熱速度,因此對焊接溫度場也有很大的影響。當(dāng)考慮了熔池內(nèi)的對流傳熱影響時,計算出的熔池尺寸及其附近溫度場等溫線比不考慮時也變寬了,而對遠(yuǎn)離熔池的溫度場影響不大。如果只是焊接線能量相同,焊接參數(shù)改變時,等溫線的形狀和尺寸也會發(fā)生很大變化。大電流快速焊情況下焊接熔池及溫度場變得很狹窄,反之會很寬。焊接導(dǎo)熱問題的常見邊界條件可歸納為以下三類:給定了邊界上的溫度值,稱為第一類邊界條件;給定了邊界上的熱流密度值,稱為第二類邊界條件;給定了邊界上物體與周圍介質(zhì)間的換熱系數(shù)及周圍介質(zhì)的溫度,稱為第三類邊界條件。對于無限大的物體
33、,邊界條件所產(chǎn)生的影響可以忽略。焊件的邊界由于與外界存在溫度差而與周圍介質(zhì)換熱,其中包括對流換熱和輻射換熱。在焊接時熱能的損失主要是通過輻射換熱,而對流換熱作用相對較小,溫度越高則輻射換熱作用越強(qiáng)烈。一般輻射與對流換熱計算方式不同,為了計算方便,應(yīng)考慮總的換熱系數(shù)。嚴(yán)格地說,對流換熱系數(shù)還與焊件的部位有關(guān),因?yàn)橹車鷼怏w流動特性不一樣,但要測出不同部位的對流換熱系數(shù)是很困難的,所以一般不予考慮。此外,與材料的其他物理性能參數(shù)一樣,換熱系數(shù)也隨溫度的變化而變化。在計算時,必須給定隨溫度變化的表面換熱系數(shù)值。在劃分網(wǎng)格時,考慮到焊縫處的溫度梯度變化較大,一般采用在焊縫及其附近部位加密網(wǎng)格;在遠(yuǎn)離焊縫
34、的區(qū)域,溫度分布梯度變化相對較小,劃分較為稀疏的網(wǎng)格??傊诒3志鹊耐瑫r減少網(wǎng)格的數(shù)量,為更好的提高效率和精度,還應(yīng)進(jìn)一步優(yōu)化網(wǎng)格。薛勇、張建勛等在劃分網(wǎng)格時采用彈塑性非線性區(qū)與線彈性區(qū)分開計算的迭代子結(jié)構(gòu)技術(shù),將局部區(qū)域的單元凝聚為超單元以便在求解中節(jié)省機(jī)時。ShiQingyu等開發(fā)了動態(tài)可逆的自適應(yīng)網(wǎng)格劃分技術(shù),不僅比普通方法節(jié)省了13的計算時間,而且溫度場和變形與實(shí)際情況符合,雖然應(yīng)力分布略有不同,但整體趨勢一致。三.焊接(hnji)應(yīng)力-應(yīng)變的數(shù)值(shz)模擬焊接過程(guchng)溫度分布是不平衡的,焊接區(qū)周圍的材料也會有不同的膨脹率和收縮率,最終形成三維殘余應(yīng)力狀態(tài)。焊接應(yīng)力
35、-應(yīng)變的數(shù)值模擬分析,包括動應(yīng)力-應(yīng)變過程、焊接殘余應(yīng)力、殘余變形和消除應(yīng)力等,會很好地提高焊接接頭的性能。3.1理論的建立和發(fā)展之前人們通過試驗(yàn)得到了很多與焊接應(yīng)力-應(yīng)變有關(guān)的經(jīng)驗(yàn)公式,但那些只能解決一些很簡單的問題。隨著焊接熱力模擬理論、有限元技術(shù)和計算機(jī)技術(shù)的發(fā)展,極大地促進(jìn)了焊接應(yīng)力-應(yīng)變數(shù)值模擬技術(shù)的研究。在一維解析式中,分析了一維條件下焊接過程中的殘余應(yīng)力與應(yīng)變過程,然后對多道焊、角焊和圓周型壓力容器焊接的應(yīng)力變形進(jìn)行了三維熱彈塑性有限元分析,得到了較理想的結(jié)果。最后應(yīng)用二維和三維焊接殘余應(yīng)力與應(yīng)變進(jìn)行了預(yù)測和測量。最近,ABachorski等人提出了收縮體積法的焊接變形有限元預(yù)測
36、理論,這是一種線彈性有限元模擬技術(shù),現(xiàn)在被用來預(yù)測焊接變形。20世紀(jì)90年代以來,人們開始用連續(xù)統(tǒng)力學(xué)的理論研究焊接問題。連續(xù)統(tǒng)力學(xué)是一套嚴(yán)密而完整的力學(xué)體系,它研究整個系統(tǒng)的平衡狀態(tài),考慮物質(zhì)的各種形態(tài),主要包括質(zhì)量與動量守恒定律以及材料的本構(gòu)關(guān)系。通過計算,連續(xù)統(tǒng)力學(xué)可以直接解決一些線性、對稱和確定的問題。3.2焊接力學(xué)模型在焊接熔池中,材料經(jīng)歷了快速加熱、凝固和快速冷卻過程。通過對一個簡單的一維問題的分析,就可以表明材料應(yīng)力-應(yīng)變的演化過程。假設(shè)在加熱和冷卻的過程中,溫度都是線性變化,那么可以計算相應(yīng)熱應(yīng)力的變化過程。冷卻時,塑性應(yīng)變可以通過從總的熱應(yīng)變中減去彈性應(yīng)變而得到。計算效率是焊
37、接力學(xué)模擬中的關(guān)鍵,人們在這一領(lǐng)域進(jìn)行了許多研究,提出了很多方法。蔡志鵬等人通過分析焊接熱源的特征,在高斯熱源的基礎(chǔ)上,根據(jù)輸入熱功率相當(dāng)提出了段熱源模型,并進(jìn)一步提出了更為實(shí)用的串熱源模型,對其進(jìn)行了比較分析,得到了非常相似的結(jié)果,這是在研究中比較靈活、方便的焊接模擬。焊接變形的預(yù)測方面以熱彈塑性有限元法和固有應(yīng)變法應(yīng)用最為廣泛。此外,還有線彈性體積收縮法、相似理論、人工神經(jīng)網(wǎng)絡(luò)等焊接變形預(yù)測的方法與理論。線彈性體積收縮法將復(fù)雜(fz)的非線性和彈塑性變形轉(zhuǎn)化為線彈性變形,假定線性熱膨脹是變形的主要驅(qū)動力,可以精確地預(yù)測大型復(fù)雜焊接結(jié)構(gòu)的變形問題,其精確性依賴于焊縫處收縮體積的計算精度。對于坡口角度小于50的焊接結(jié)構(gòu)則存在較大誤差,另外該法也不適用于預(yù)
溫馨提示
- 1. 本站所有資源如無特殊說明,都需要本地電腦安裝OFFICE2007和PDF閱讀器。圖紙軟件為CAD,CAXA,PROE,UG,SolidWorks等.壓縮文件請下載最新的WinRAR軟件解壓。
- 2. 本站的文檔不包含任何第三方提供的附件圖紙等,如果需要附件,請聯(lián)系上傳者。文件的所有權(quán)益歸上傳用戶所有。
- 3. 本站RAR壓縮包中若帶圖紙,網(wǎng)頁內(nèi)容里面會有圖紙預(yù)覽,若沒有圖紙預(yù)覽就沒有圖紙。
- 4. 未經(jīng)權(quán)益所有人同意不得將文件中的內(nèi)容挪作商業(yè)或盈利用途。
- 5. 人人文庫網(wǎng)僅提供信息存儲空間,僅對用戶上傳內(nèi)容的表現(xiàn)方式做保護(hù)處理,對用戶上傳分享的文檔內(nèi)容本身不做任何修改或編輯,并不能對任何下載內(nèi)容負(fù)責(zé)。
- 6. 下載文件中如有侵權(quán)或不適當(dāng)內(nèi)容,請與我們聯(lián)系,我們立即糾正。
- 7. 本站不保證下載資源的準(zhǔn)確性、安全性和完整性, 同時也不承擔(dān)用戶因使用這些下載資源對自己和他人造成任何形式的傷害或損失。
最新文檔
- 廣東科學(xué)技術(shù)職業(yè)學(xué)院《民航英語》2023-2024學(xué)年第一學(xué)期期末試卷
- 廣東酒店管理職業(yè)技術(shù)學(xué)院《現(xiàn)場總線控制技術(shù)》2023-2024學(xué)年第一學(xué)期期末試卷
- 廣東金融學(xué)院《家用電器設(shè)計》2023-2024學(xué)年第一學(xué)期期末試卷
- 廣東工業(yè)大學(xué)《反應(yīng)工程概論》2023-2024學(xué)年第一學(xué)期期末試卷
- 廣東東軟學(xué)院《技術(shù)經(jīng)濟(jì)分析與生產(chǎn)管理》2023-2024學(xué)年第一學(xué)期期末試卷
- 廣東創(chuàng)新科技職業(yè)學(xué)院《第二外語日語(二)》2023-2024學(xué)年第一學(xué)期期末試卷
- 廣東白云學(xué)院《科學(xué)技術(shù)與工程倫理》2023-2024學(xué)年第一學(xué)期期末試卷
- 贛南師范大學(xué)科技學(xué)院《中國當(dāng)代文學(xué)(2)》2023-2024學(xué)年第一學(xué)期期末試卷
- 贛州師范高等專科學(xué)?!队袡C(jī)寶石學(xué)》2023-2024學(xué)年第一學(xué)期期末試卷
- 甘孜職業(yè)學(xué)院《生物技術(shù)綜合性實(shí)驗(yàn)?zāi)K》2023-2024學(xué)年第一學(xué)期期末試卷
- 【物理】浙江省寧波市九校2022-2023學(xué)年高二上學(xué)期1月期末考試試題(解析版)
- 建筑用木料及加工木材組件相關(guān)項(xiàng)目實(shí)施方案
- 職業(yè)健康管理與法律法規(guī)培訓(xùn)
- 廣東省深圳市寶安區(qū)2023-2024學(xué)年六年級上學(xué)期期中數(shù)學(xué)試卷
- 初三九年級英語英語英語語法填空附答案附解析
- 圖紙會審設(shè)計交底記錄表格
- 叉車月度檢查記錄表
- 犯罪學(xué)學(xué)習(xí)通超星課后章節(jié)答案期末考試題庫2023年
- 法律職業(yè)倫理考試題庫匯總含答案
- 呆滯品管理制度范本(3篇)
- 海底撈-新員工培訓(xùn)
評論
0/150
提交評論