

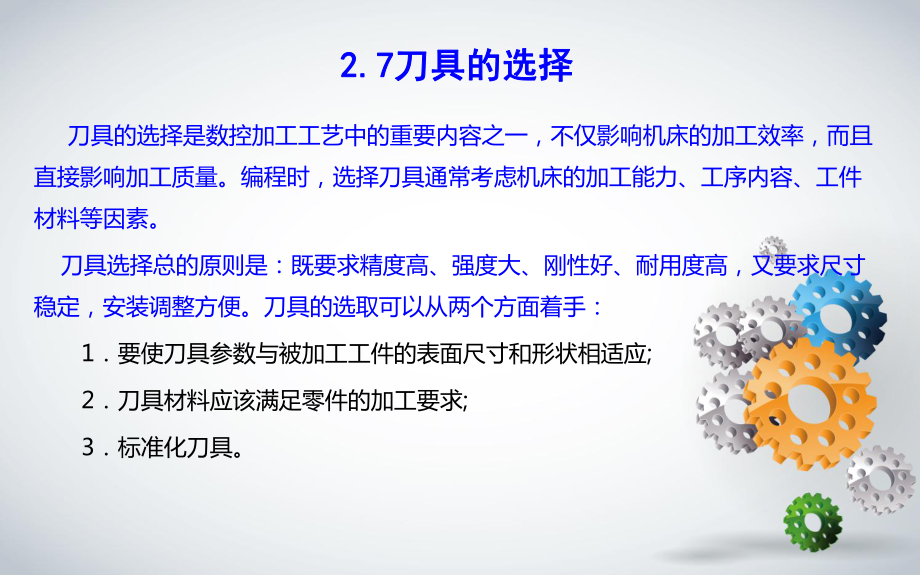


版權(quán)說明:本文檔由用戶提供并上傳,收益歸屬內(nèi)容提供方,若內(nèi)容存在侵權(quán),請進行舉報或認領(lǐng)
文檔簡介
1、現(xiàn)代數(shù)控編程技術(shù)及應(yīng)用2.7刀具的選擇2.8切削用量的確定2.10冷卻液的選擇2.11數(shù)控編程的誤差控制2.12在線測量2.13數(shù)控加工工藝文件2.14計算機輔助工藝設(shè)計2.9順銑與逆銑2.72.7刀具的選擇刀具的選擇 刀具的選擇是數(shù)控加工工藝中的重要內(nèi)容之一,不僅影響機床的加工效率,而且直接影響加工質(zhì)量。編程時,選擇刀具通??紤]機床的加工能力、工序內(nèi)容、工件材料等因素。 刀具選擇總的原則是:既要求精度高、強度大、剛性好、耐用度高,又要求尺寸穩(wěn)定,安裝調(diào)整方便。刀具的選取可以從兩個方面著手: 1要使刀具參數(shù)與被加工工件的表面尺寸和形狀相適應(yīng); 2刀具材料應(yīng)該滿足零件的加工要求; 3標(biāo)準(zhǔn)化刀具。
2、常見的車削刀具常見的車削刀具常見的車削刀具常見的車削刀具端面車刀、切槽車刀、內(nèi)外孔車刀端面車刀、切槽車刀、內(nèi)外孔車刀常見的車削刀具常見的車削刀具常見的車削刀具常見的車削刀具常見的銑削刀具常見的銑削刀具常見的銑削刀具常見的銑削刀具常見的銑削刀具常見的銑削刀具2.8 2.8 切削用量的確定切削用量的確定 合理選擇切削用量的原則是: 粗加工時,一般以提高生產(chǎn)率為主,但也應(yīng)考慮經(jīng)濟性和加工成本,通常選擇較大的背吃刀量和進給量,采用較低的切削速度; 半精加工和精加工時,應(yīng)在保證加工質(zhì)量的前提下,兼顧切削效率、經(jīng)濟性和加工成本,通常選擇較小的背吃刀量和進給量,并選用切削性能高的刀具材料和合理的幾何參數(shù),以
3、盡可能提高切削速度。 1 1主軸轉(zhuǎn)速的確定主軸轉(zhuǎn)速的確定 主軸轉(zhuǎn)速應(yīng)根據(jù)允許的切削速度和工件(或刀具)直徑來選擇。其計算公式為: n=1000 V /D式中:V切削速度,單位為m/min,由刀具的耐用度決定; n主軸轉(zhuǎn)速,單位為 r/min; D工件直徑或刀具直徑,單位為mm。圖圖 超程誤差與控制超程誤差與控制 2進給速度的確定進給速度的確定 進給速度是數(shù)控機床切削用量中的重要參數(shù),主要根據(jù)零件的加工精度和表面粗糙度要求和刀具、工件的材料性質(zhì)選取。最大進給速度受機床剛度和進給系統(tǒng)的性能限制。 在選擇進給速度時,還要注意零件加工中的某些特殊因素。例如在輪廓加工中,當(dāng)零件輪廓有拐角時,刀具容易產(chǎn)生
4、“超程”現(xiàn)象,從而導(dǎo)致加工誤差。如圖所示。 應(yīng)當(dāng)指出,在輪廓加工中,當(dāng)?shù)毒哌\動方向改變時,由于運動的滯后,還會產(chǎn)生“欠程”現(xiàn)象,而導(dǎo)致“欠程誤差”。 3背吃刀量確定背吃刀量確定 背吃刀量根據(jù)機床、工件和刀具的剛度來決定,在剛度允許的條件下,應(yīng)盡可能使背吃刀量等于工件的加工余量,這樣可以減少走刀次數(shù),提高生產(chǎn)效率。為了保證加工表面質(zhì)量,可留少量精加工余量,一般0.20.5mm。 總之,切削用量的具體數(shù)值應(yīng)根據(jù)機床性能、相關(guān)的手冊并結(jié)合實際經(jīng)驗用類比方法確定。同時,使主軸轉(zhuǎn)速、切削深度及進給速度三者能相互適應(yīng),以形成最佳切削。表表1-2 數(shù)控車削用量推薦表數(shù)控車削用量推薦表工件材料工件材料加工方式
5、加工方式背吃刀量背吃刀量/ /mm切削速度切削速度/ /(m/min)進給量進給量/(mm/r)刀具材料刀具材料碳素鋼碳素鋼 s sb600 MPa粗加工粗加工 57 6080 0.20.4YT類類粗加工粗加工 23 80120 0.20.4精加工精加工 0.20.3 120150 0.10.2車螺紋車螺紋 70100導(dǎo)程導(dǎo)程鉆中心孔鉆中心孔 500800 r/min W18Cr4V鉆鉆 孔孔 30 0.10.2切斷切斷( (寬度寬度 5 mm) 70110 0.10.2YT類類合金鋼合金鋼s sb=1470 MPa粗加工粗加工23 5080 0.20.4YT類類精加工精加工0.10.15 6
6、0100 0.10.2切斷切斷( (寬度寬度 5 mm) 4070 0.10.2 鑄鑄 鐵鐵 200 HBS 以以 下下粗加工粗加工23 5070 0.20.4YG類類精加工精加工0.10.15 70100 0.10.2切斷切斷( (寬度寬度 5 mm) 5070 0.10.2鋁鋁粗加工粗加工23 6001000 0.20.4YG類類精加工精加工0.20.3 8001200 0.10.2切斷切斷( (寬度寬度 5 mm) 6001000 0.10.2黃銅黃銅粗加工粗加工24 400500 0.20.4YG類類精加工精加工0.10.15 450600 0.10.2切斷切斷( (寬度寬度 5 mm
7、) 400500 0.10.2表表1-2 數(shù)控車削用量推薦表數(shù)控車削用量推薦表 表表1-3 銑刀的切削速度銑刀的切削速度 (m/min)工件材料工件材料銑銑 刀刀 材材 料料碳素鋼碳素鋼高速鋼高速鋼超高速鋼超高速鋼StelliteYTYG鋁鋁75150150300 240460 300600黃銅黃銅12252050 4575 100180青銅青銅( (硬硬) )10202040 3050 60130青銅青銅( (最硬最硬) ) 10151520 4060鑄鐵鑄鐵( (軟軟) )1012152518352840 75100鑄鐵鑄鐵( (硬硬) ) 101510201828 4560鑄鐵鑄鐵( (
8、冷硬冷硬) ) 10151228 3060可鍛鑄鐵可鍛鑄鐵1015203025403545 75110銅銅( (軟軟) )101418282030 4575 銅銅( (中中) )101515251828 4060 銅銅( (硬硬) ) 10151220 3045表表1-3 銑刀的切削速度銑刀的切削速度 工件材料工件材料圓柱銑刀圓柱銑刀面銑刀面銑刀立銑刀立銑刀桿銑刀桿銑刀成形銑刀成形銑刀高速鋼嵌高速鋼嵌齒銑刀齒銑刀硬質(zhì)合金嵌硬質(zhì)合金嵌齒銑刀齒銑刀鑄鐵鑄鐵0.20.20.070.050.040.30.1軟軟(中硬中硬)鋼鋼0.20.20.070.050.040.30.09硬鋼硬鋼0.150.150
9、.060.040.030.20.08鎳鉻鋼鎳鉻鋼0.10.10.050.020.020.150.06高鎳鉻鋼高鎳鉻鋼0.10.10.040.020.020.10.05可鍛鑄鐵可鍛鑄鐵0.20.150.070.050.040.30.09鑄鐵鑄鐵0.150.10.070.050.040.20.08青銅青銅0.150.150.070.050.040.30.1黃銅黃銅0.20.20.070.050.040.30.21鋁鋁0.10.10.070.050.040.20.1Al-Si合金合金0.10.10.070.050.040.180.08Mg-Al-Zn合金合金0.10.10.070.040.030.1
10、50.08Al-Cu-Mg合金合金Al-Cu-Si合金合金0.150.10.070.050.040.20.1表表1-4 銑刀進給量銑刀進給量 表表1-5 高速鋼鉆頭的切削用量高速鋼鉆頭的切削用量 (v:m/mm,f:mm/r)工件材料工件材料s sb(MPa) )鉆頭直徑鉆頭直徑 ( (mm) )25611121819252650vfvfvfvfvf鋼鋼49020250.120250.230350.230350.325300.449068620250.120250.220250.225300.2250.268688215180.0515180.115180.218220.315200.3588
11、2107810140.0510140.112180.1516200.214160.3鑄鐵鑄鐵11817625300.130400.225300.35200.6201.017629415180.114180.1516200.2160.316180.4黃銅黃銅軟軟500.05500.15500.3500.4550青銅青銅軟軟350.05350.1350.2350.35352.9 順銑與逆銑順銑與逆銑 沿著刀具的進給方向看,如果工件位于銑刀進給方向的右側(cè),那么進給方向稱為順時針。反之,當(dāng)工件位于銑刀進給方向的左側(cè)時,進給方向定義為逆時針。如果銑刀旋轉(zhuǎn)方向與工件進給方向相同,稱為順銑;銑刀旋轉(zhuǎn)方向與工
12、件進給方向相反,稱為逆銑。 逆銑時,切削由薄變厚,刀齒從已加工表面切入,對銑刀的使用有利。順銑時,刀齒開始和工件接觸時切削厚度最大,且從表面硬質(zhì)層開始切入,刀齒受很大的沖擊負荷,銑刀變鈍較快,但刀齒切入過程中沒有滑移現(xiàn)象。 順銑的功率消耗要比逆銑時小,在同等切削條件下,順銑功率消耗要低5%15%,同時順銑也更加有利于排屑。一般應(yīng)盡量采用順銑法加工,以提高被加工零件表面的光潔度(降低粗糙度),保證尺寸精度。但是在切削面上有硬質(zhì)層、積渣、工件表面凹凸不平較顯著時,如加工鍛造毛坯,應(yīng)采用逆銑法。逆銑.avi順銑.avi2.10 冷卻液選擇冷卻液選擇 在切削加工中加注冷卻液,為降低切削溫度,斷屑與排屑
13、起到了很好的作用,但也存在著許多弊端。例如,維持一個大型的冷卻液系統(tǒng)需花費很多資金。它需要定期添加防腐劑,更換冷卻液等,并花去許多輔助時間。加之由于冷卻液中的有害物質(zhì),對工人的健康造成危害,也使冷卻液使用受到限制。干切削加工就是要在沒有切削液的條件下創(chuàng)造具有與濕切相同或相近的切削條件。用于干切削的刀具須合理選擇刀具材料及涂層,設(shè)計合理的刀具幾何參數(shù),大部分可轉(zhuǎn)換刀具均可使用干切削。冷卻液開關(guān)在數(shù)控編程中可以自動設(shè)定,對自動換刀的數(shù)控加工中心,可以按需要開啟冷卻液。對于一般的數(shù)控銑或者使用人工換刀進行加工的,應(yīng)該關(guān)閉冷卻液開關(guān)。因為通常在程序初始階段,程序錯誤或者校調(diào)錯誤等會暴露出來,加工有一定
14、的危險性,需要機床操作人員觀察以確保安全,同時保持機床及周邊環(huán)境整潔。冷卻液開關(guān)由機床操作人員確認程序沒錯誤,可以正常加工時,打開機床控制面板上的冷卻液開關(guān)。2.10 冷卻液選擇冷卻液選擇2.11數(shù)控編程的誤差控制數(shù)控編程的誤差控制 程序編制中的誤差主要有以下三部分組成。 1逼近誤差 2插補誤差 3圓整化誤差 零件圖上給出的公差,允許分配給程編誤差的只能占一小部分。還有其他很多誤差,如機床誤差、控制系統(tǒng)誤差、拖動系統(tǒng)誤差、零件定位逞羞、對刀誤差、刀具磨損誤差、工件變形誤差等等。其中拖動系統(tǒng)誤差和定位誤差常常是加工誤差的主要來源,因此程編誤差一般應(yīng)控制在零件公差的1020以內(nèi)。2.12 在線測量
15、在線測量 機床加工過程按預(yù)先編制好的零件加工程序自動進行,不隨實際加工狀況變化而變化,但在實際加工現(xiàn)場,通常存在許多變量直接或間接影響加工效果,如工件毛坯余量及其誤差等。由于這類變量事先難以預(yù)測,所以只能憑經(jīng)驗數(shù)據(jù)編制加工程序,難以同實際加工狀況相吻合,而不能實現(xiàn)最佳切削過程。 隨著計算機技術(shù)的發(fā)展,現(xiàn)代CNC系統(tǒng)功能已日益完善,目前,已發(fā)展到不僅能對加工的實際工藝狀況進行在線檢測,而且還能根據(jù)切削條件選擇最佳切削用量,自動調(diào)整并保持最優(yōu)加工狀況,以彌補編程的不足,使數(shù)控機床的功能得到充分發(fā)揮,保證加工出合格零件,實現(xiàn)高效,低成本生產(chǎn)。如數(shù)控車床常用的數(shù)控系統(tǒng)SINUMERIK 810TE。
16、2.13 數(shù)控加工工藝文件數(shù)控加工工藝文件 數(shù)控加工工藝文件不僅是進行數(shù)控加工和產(chǎn)品驗收的依據(jù),也是操作者遵守和執(zhí)行的規(guī)程,同時還為產(chǎn)品零件重復(fù)生產(chǎn)積累了必要的工藝資料,完成了技術(shù)儲備。文件包括了編程任務(wù)書、數(shù)控加工工序卡、數(shù)控刀具卡片、數(shù)控加工程序單等。 1數(shù)控加工編程任務(wù)書數(shù)控加工編程任務(wù)書(見表見表3-1) 工藝處工藝處數(shù)控編程任務(wù)書數(shù)控編程任務(wù)書產(chǎn)品零件圖號產(chǎn)品零件圖號任務(wù)書編號任務(wù)書編號零件名稱零件名稱適用數(shù)控設(shè)備適用數(shù)控設(shè)備共共 頁第頁第 頁頁主要工序說明及技術(shù)要求:主要工序說明及技術(shù)要求:編程收到日期編程收到日期月月 日日經(jīng)手經(jīng)手人人編制編制審核審核編程編程審核審核批準(zhǔn)批準(zhǔn)表表3
17、-13-1 數(shù)控加工編程任務(wù)書數(shù)控加工編程任務(wù)書 2數(shù)控加工工序卡數(shù)控加工工序卡(見表見表3-2) 表表3-23-2 數(shù)控加工工序卡數(shù)控加工工序卡單位單位數(shù)控加工工序卡片數(shù)控加工工序卡片產(chǎn)品名稱或代號產(chǎn)品名稱或代號零件名稱零件名稱零件圖號零件圖號工序簡圖工序簡圖車車 間間設(shè)用設(shè)備設(shè)用設(shè)備工藝序號工藝序號程序編號程序編號夾具名稱夾具名稱夾具編號夾具編號工步號工步號工步作業(yè)內(nèi)容工步作業(yè)內(nèi)容加加工工面面刀具刀具號號刀補刀補量量主軸主軸轉(zhuǎn)速轉(zhuǎn)速進給進給速度速度背吃背吃刀量刀量備注備注編制編制審審核核批準(zhǔn)批準(zhǔn)年年 月月 日日共共 頁頁第第 頁頁 如果工序加工內(nèi)容比較簡單,也可采用表3-3數(shù)控加工工藝卡片
18、的形式。 表表3-3 3-3 數(shù)控加工工藝卡片數(shù)控加工工藝卡片單位名稱單位名稱產(chǎn)品名稱或代號產(chǎn)品名稱或代號零件名稱零件名稱零件圖號零件圖號工序號工序號程序編號程序編號夾具名稱夾具名稱適用設(shè)備適用設(shè)備車間車間工步號工步號工步內(nèi)容工步內(nèi)容刀具號刀具號刀具刀具規(guī)格規(guī)格主軸主軸轉(zhuǎn)速轉(zhuǎn)速進給進給速度速度背吃刀量背吃刀量備注備注編制編制審核審核批準(zhǔn)批準(zhǔn)年年 月月 日日共共 頁頁第第 頁頁 3 3數(shù)控刀具卡片(見表數(shù)控刀具卡片(見表3-43-4)表表3-4 3-4 數(shù)控刀具卡片數(shù)控刀具卡片產(chǎn)品名稱或代號產(chǎn)品名稱或代號零件名稱零件名稱零件圖號零件圖號刀具號刀具號刀具規(guī)格名稱刀具規(guī)格名稱數(shù)量數(shù)量加工表面加工表面
19、備注備注編制編制審核審核批準(zhǔn)批準(zhǔn)共共 頁頁第第 頁頁 4 4數(shù)控加工程序單(見表數(shù)控加工程序單(見表3-53-5)表表3-5 3-5 數(shù)控加工程序單數(shù)控加工程序單零件號零件號零件名稱零件名稱編制編制審核審核程序號程序號日期日期日期日期NGX(U)Z(W)FSTMCR備注備注座架零件圖樣座架零件圖樣1551038162-1 46-62240721515AB50現(xiàn)以圖所示零件加工為例作簡單介紹,以供參考。 1 1數(shù)控加工工件安裝和零點設(shè)定卡片(機床調(diào)整單)數(shù)控加工工件安裝和零點設(shè)定卡片(機床調(diào)整單) 它應(yīng)表示出數(shù)控加工零件定位方法和夾緊方法,并應(yīng)標(biāo)明工件零點設(shè)定位置和坐標(biāo)方向、使用的夾具名稱和編號
20、等。假設(shè)上圖座架零件的下臺階面已在其他機床上加工出,現(xiàn)需要在數(shù)控機床上一次裝夾后加工剩下的表面和各個孔,采用通用臺鉗作為夾具,其工件裝夾和零點設(shè)定卡如表1-6所示。表表1-6 1-6 工件安裝和零點設(shè)定卡片工件安裝和零點設(shè)定卡片 上述座架零件在數(shù)控機床上的加工安排是:先用端面銑刀銑出上表面,再用立銑刀銑四周側(cè)面及A、B工作面,最后用鉆頭分別鉆6個小孔和兩個大孔。填寫工序卡如表1-7所示。1551038162 -1 46 -62 24 07 21515AB50表表1-7 1-7 數(shù)控加工工序卡片數(shù)控加工工序卡片產(chǎn) 品 名 稱 代 號 零 件 名 稱 零 件 圖 號 xxx 廠 數(shù) 控 加 工 工
21、 序 卡 片 座 架 WD?9901 工 藝 序 號 程 序 編 號 夾 具 名 稱 夾 具 編 號 使 用 設(shè) 備 車 間 臺 鉗 ZJK7532?1 數(shù) 控 工 步 號 工 步 作 業(yè) 內(nèi) 容 加 工 面 刀 具 號 刀 具 規(guī) 格 主 軸 轉(zhuǎn) 速 進 給 速 度 切 削 深 度 備 注 1 50 面 銑 刀 銑 上 表 面 上 表 面 T01 50 面 銑 刀 1000 200 +15 2 20 立 銑 刀 銑 四 周 側(cè) 面 四 側(cè) 面 T02 20 立 銑 刀 1000 200 ?11 3 20 立 銑 刀 銑 A、B 臺 階 面 A、 B 面 T02 20 立 銑 刀 1000 2
22、00 0 4 6 鉆 頭 鉆 6 個 小 孔 小 孔 6 T03 6 鉆 頭 800 100 ?22 5 14 鉆 頭 鉆 2 個 大 孔 大 孔 2 T04 14 鉆 頭 500 80 ?22 編 制 審 核 批 準(zhǔn) 年 月 日 共 頁 第 頁 3數(shù)控刀具調(diào)整單數(shù)控刀具調(diào)整單 數(shù)控刀具調(diào)整單主要包括數(shù)控刀具卡片和數(shù)控刀具明細表(簡稱刀具表)兩部分。 數(shù)控加工時,對刀具的要求十分嚴格,一般要在機外對刀儀上,事先調(diào)整好刀具直徑和長度。刀具卡主要反映刀具編號、刀具結(jié)構(gòu)、尾柄規(guī)格、組合件名稱代號、刀片型號和材料等,它是組裝刀具和調(diào)整刀具的依據(jù)。其格式如表1-8所示。表表1-10 數(shù)控刀具卡片數(shù)控刀具
23、卡片零 件 圖 號 WD?9901 使 用 設(shè) 備 刀 具 名 稱 立 銑 刀 數(shù) 控 刀 具 卡 片 ZJK7532?1 刀 具 編 號 T02 換 刀 方 式 手 動 程 序 編 號 序 號 編 號 刀 具 名 稱 規(guī) 格 數(shù) 量 備 注 1 vfd.17550 4 拉 釘 2 GB 1106?85 刀 柄 3 銑 刀 20 80 1 切 削 液 : 柴 油 刀 具 組 成 4 13D2 備 注 編 制 審 核 批 準(zhǔn) 共 頁 第 頁 表表1-9 數(shù)控刀具明細表數(shù)控刀具明細表 零 件 圖 號 零 件 名 稱 材 料 數(shù) 控 刀 具 程 序 編 號 車 間 使 用 設(shè) 備 WD?9901 座
24、 架 20# 明 細 表 數(shù) 控 ZJK7532?1 刀 具 刀 補 換 刀 直 徑 (mm) 長 度 地 址 方 式 刀 號 刀 位 號 刀 具 名 稱 刀 具 圖 號 設(shè) 定 補 償 設(shè) 定 直 徑 長 度 自 動 /手 動 加 工 部 位 T01 面 銑 刀 50 40 H01 手 動 T02 立 銑 刀 20 20 75 D02 H02 手 動 T03 鉆 頭 6 95 H03 手 動 T04 鉆 頭 14 130 H04 手 動 編 制 審 核 批 準(zhǔn) 年 月 日 共 頁 第 頁 2.132.13計算機輔助工藝設(shè)計計算機輔助工藝設(shè)計 1工藝設(shè)計自動化的重要意義 生產(chǎn)的零件品種數(shù)和工藝
25、規(guī)程數(shù)并不存在一一對應(yīng)的關(guān)系。目前工藝規(guī)程設(shè)計中存在的重復(fù)性和多樣性,不僅本身是一種浪費,而且還影響到工裝設(shè)備的制造和使用。 計算機輔助工藝規(guī)程設(shè)計(Computer Aided Process Planning),簡稱CAPP,不僅能實現(xiàn)工藝設(shè)計自動化,還能把生產(chǎn)實踐中行之有效的若干工藝設(shè)計原則與方法,轉(zhuǎn)換成工藝設(shè)計決策模型,建立科學(xué)的決策邏輯,把長期從事工藝設(shè)計工作者的經(jīng)驗傳授給初參加工作者,編制出最優(yōu)的制造方案。另外,CAPP也是把CAD和CAM的信息連接起來,實現(xiàn)CADCAM一體化,建立集盤制造系統(tǒng)的關(guān)鍵性中間環(huán)節(jié)。 2 2CAPPCAPP的發(fā)展概況的發(fā)展概況 在機械制造領(lǐng)域內(nèi)工藝設(shè)計自動化是發(fā)展最遲的部分。 1952年,美國麻省理工學(xué)院就已研制成功數(shù)控機床; 1963年又發(fā)表了CAD的研究成果; 1961年開始,世界上最早進行工藝設(shè)計自動化研究的國家是挪威; 1969年正式發(fā)表了AUTOPROS系統(tǒng)。這是世界上第一個CAPP系統(tǒng)。 我國進行這項研究工作的是上海同濟
溫馨提示
- 1. 本站所有資源如無特殊說明,都需要本地電腦安裝OFFICE2007和PDF閱讀器。圖紙軟件為CAD,CAXA,PROE,UG,SolidWorks等.壓縮文件請下載最新的WinRAR軟件解壓。
- 2. 本站的文檔不包含任何第三方提供的附件圖紙等,如果需要附件,請聯(lián)系上傳者。文件的所有權(quán)益歸上傳用戶所有。
- 3. 本站RAR壓縮包中若帶圖紙,網(wǎng)頁內(nèi)容里面會有圖紙預(yù)覽,若沒有圖紙預(yù)覽就沒有圖紙。
- 4. 未經(jīng)權(quán)益所有人同意不得將文件中的內(nèi)容挪作商業(yè)或盈利用途。
- 5. 人人文庫網(wǎng)僅提供信息存儲空間,僅對用戶上傳內(nèi)容的表現(xiàn)方式做保護處理,對用戶上傳分享的文檔內(nèi)容本身不做任何修改或編輯,并不能對任何下載內(nèi)容負責(zé)。
- 6. 下載文件中如有侵權(quán)或不適當(dāng)內(nèi)容,請與我們聯(lián)系,我們立即糾正。
- 7. 本站不保證下載資源的準(zhǔn)確性、安全性和完整性, 同時也不承擔(dān)用戶因使用這些下載資源對自己和他人造成任何形式的傷害或損失。
最新文檔
- 解讀蘇教版課件的聲音奧秘
- 蘇教版小學(xué)科學(xué)教材教學(xué)應(yīng)用案例
- 人教版九年級政治會考試卷解析版
- 初中生物蘇教版復(fù)習(xí)點撥
- 人教版四年級下科學(xué)復(fù)習(xí)要點
- 中考化學(xué)人教版試卷練習(xí)與解析
- 北師大版四年級電子書全文
- 蘇教版三年級下冊數(shù)學(xué)期末知識點題
- 蘇教版四年級科學(xué)下冊課件培養(yǎng)探究精神
- 蘇教版八年級生物上冊課件深度解析
- 2022年9月17日陜西省直遴選筆試真題及解析
- 2024年個人信用報告(個人簡版)樣本(帶水印-可編輯)
- 16J914-1 公用建筑衛(wèi)生間
- 初一英語自我介紹通用PPT課件
- IELTS雅思答題卡(全套清晰版)
- SYNTEC M新代銑床程序說明書
- 外科主任崗位說明書
- 脾胃病科-膽脹慢性膽囊炎中醫(yī)臨床路徑試行版匯編
- 搪瓷工藝的參數(shù)
- 在現(xiàn)代物流業(yè)高質(zhì)量發(fā)展座談會上的講話
- 無壓力管道嚴密性試驗記錄自動計算表
評論
0/150
提交評論