



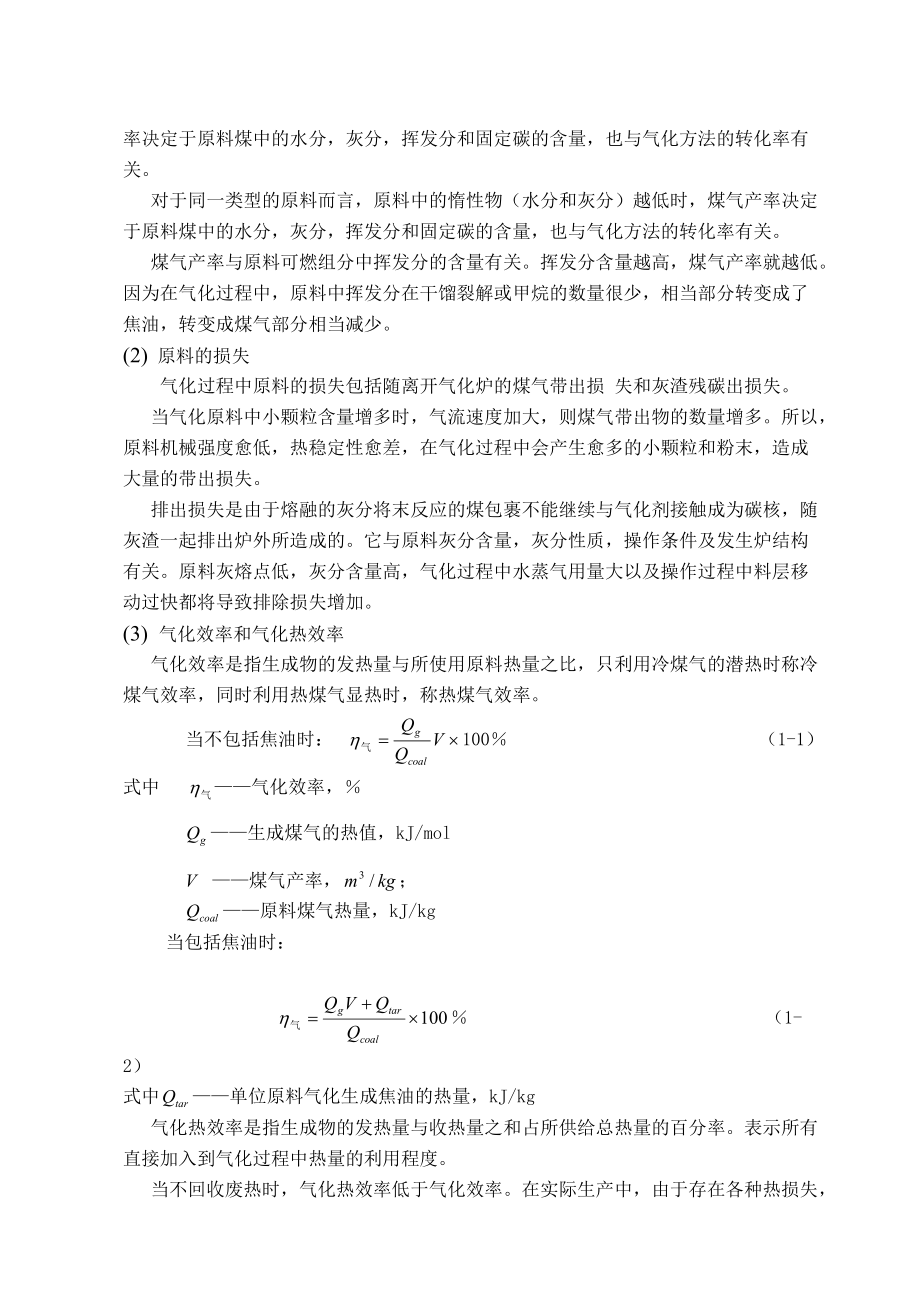
版權(quán)說明:本文檔由用戶提供并上傳,收益歸屬內(nèi)容提供方,若內(nèi)容存在侵權(quán),請進行舉報或認(rèn)領(lǐng)
文檔簡介
1、第1章 前 言 1.1 概述固定床煤氣化技術(shù)是最先實現(xiàn)運用的工業(yè)化技術(shù),在此基礎(chǔ)上發(fā)展起來的合成氨工業(yè)為糧食增產(chǎn)和軍工業(yè)的發(fā)展奠定了重要的基礎(chǔ)。國之大事無非足糧足兵,糧食充足則天下大定,諸項事業(yè)皆可繁榮;兵堅器銳則國自安,外敵無隙可乘。德國作為后起的帝國主義國家,外無廣大的殖民地可供掠奪并提供原料,國內(nèi)資源缺乏。但是德國通過發(fā)展合成氨工業(yè),既解決了糧食問題,又解決了軍事工業(yè)發(fā)展必須的硝銨供應(yīng),遂有能力起而與日不落帝國爭奪生存空間,歷數(shù)年而不敗,最后因石油供應(yīng)短缺和美國參戰(zhàn)而被迫投降。處理戰(zhàn)后國際格局安排的巴黎和會,其中重要但已為人忘卻的決議之一就是要求德國向全世界公開合成氨工業(yè)的技術(shù)。合成氨工
2、業(yè)的極端重要性由此可見。巴黎和會后,全世界均以煤為原料,采用固定床煤氣化技術(shù)發(fā)展合成氨工業(yè)。民國時期,國民政府最重大的工業(yè)建設(shè)之一即為南京永利寧鈕廠年產(chǎn)6萬噸合成氨裝置,1937年毀于抗日戰(zhàn)爭。上世紀(jì)四五十年代是全球煤化工發(fā)展的黃金時間時期,但隨著石油的大量發(fā)現(xiàn),中東廉價石油的開發(fā),石油化工興起,煤化工逐步退出。至上世紀(jì)六七十年代,全世界除中國和南非外煤化工時代已經(jīng)完全結(jié)束,煤氣化技術(shù)的發(fā)展完全停止。上世紀(jì)七十年代石油危機爆發(fā)后,煤氣化技術(shù)再度受到重視,相繼開發(fā)了德士古水煤漿氣化、殼牌煤粉氣化等技術(shù),并建立示范工程用于聯(lián)合循環(huán)發(fā)電。但是僅有美國帝斯曼公司采用德士古水煤漿氣化技術(shù)建設(shè)的甲醇、醋酸
3、裝置進入商業(yè)化運行,其余項目均止于示范工程階段。上世紀(jì)九十年代以后,國外的煤氣化技術(shù)進入中國,用于合成氨甲醇的新建項目以及油頭合成氨裝置的技術(shù)改造。中國由于特殊的歷史條件和資源條件,上世紀(jì)五十年代開始大規(guī)模地采用固定床煤氣化技術(shù)進行合成氨生產(chǎn),用以解決國家面臨的極為嚴(yán)重的糧食短缺問題。當(dāng)時由國務(wù)院副總理陳云親自抓這項工作。以當(dāng)時化工部副部長侯德榜發(fā)明的碳銨為產(chǎn)品路線,在全國每個縣均建立小合成氨廠,甚至于有的縣建立了數(shù)個合成氨廠。這些小合成氨廠大部分在上世紀(jì)七十年代建成,并逐步穩(wěn)定運行。同時在上世紀(jì)七十年代初期,隨著中國與西方關(guān)系的緩和,我國用石油換取的寶貴外匯先后引進了前十三套和后十三套合計2
4、6套的年產(chǎn)30萬噸合成氨52萬噸尿素裝置,大約在七十年代末、八十年代初相繼建成投產(chǎn),使我國化肥產(chǎn)量在七十年代末、八十年代初顯現(xiàn)爆炸性的增長。此時,雜交水稻良種的培育也已成功,并進入大規(guī)模推廣階段。這是我國在八十年代初期糧食巨幅增長、并一舉解決千百年來未能解決溫飽問題的重要物質(zhì)基礎(chǔ)和技術(shù)原因。八十年代后期,我國的糧食和化肥均出現(xiàn)短時期的過剩。合成氨工業(yè)的發(fā)展從量的擴增進到質(zhì)的提高階段。大量競爭力差的小合成氨廠逐步退出生產(chǎn),剩下的小合成氨廠通過不斷的技術(shù)改造,其生產(chǎn)規(guī)模和技術(shù)水平迅速提高,同時在國家政策的支持下改產(chǎn)尿素,實現(xiàn)產(chǎn)品路線的調(diào)整,競爭力明顯增強。目前我國合成氨工業(yè)競爭力最強、發(fā)展最快的企
5、業(yè)集團,其企業(yè)核心均為原先的小合成氨廠,如湖北宜化集團、山東華魯恒升、聯(lián)盟化工、魯西化工、心連心集團、河南駿馬集團等,而采用國外石油路線或引進國外先進煤氣化技術(shù)的企業(yè),無論在發(fā)展速度,還是企業(yè)效益情況均不能與之相比。1.2 煤炭氣化的定義和氣化反應(yīng) 煤炭氣化的定義煤炭的氣化是指在氣化爐內(nèi),煤在高溫下與氣化劑反應(yīng),生成煤氣的全過程。煤炭氣化過程的基本條件是:氣化爐,氣化原料和氣化劑。氣化爐是煤炭氣化的核心設(shè)備;氣化劑為氧氣或空氣以及水蒸氣和二氧化碳等。 煤炭氣化的主要反應(yīng)a碳的氧化反應(yīng)b碳的部分氧化反應(yīng)c二氧化碳的還原反應(yīng)d水蒸氣的分解反應(yīng)e水蒸氣分解反應(yīng)f一氧化碳變換反應(yīng)g碳的加氫反應(yīng)h甲烷化
6、反應(yīng)煤炭氣化的目的產(chǎn)品是燃料氣或化工原料氣,煤氣的有效成分是CO.和,因此上述反應(yīng)應(yīng)根據(jù)煤氣用途的不同加以控制。1.3 移動床氣化 混合發(fā)生爐煤氣混合發(fā)生爐是移動床常壓氣化技術(shù)最成熟的氣化方法之一,原料煤在煤氣發(fā)生爐內(nèi)與空氣和水蒸氣組成的混合氣化劑發(fā)生反應(yīng),生成混合發(fā)生爐煤氣?;旌习l(fā)生爐煤氣屬于低熱值煤氣,一般在4.67.5MJ/之間,主要用作工業(yè)燃料氣,不能單獨作煤氣使用。(1) 氣化過程氣化爐為圓筒形,外殼由鋼板制造。氣化爐由爐體。爐體裝置,爐蓖,氣化劑入口和煤氣出口等部分組成。煤氣發(fā)生爐內(nèi)燃料層由下至上大致可分為五層。a灰渣層:在灰渣層中,氣化劑不發(fā)生化學(xué)反應(yīng),只與灰渣進行熱交換,氣化劑
7、吸收灰渣的熱量而升溫預(yù)熱,灰渣則被冷卻。b氧化層:主要進行碳的燃燒反應(yīng):,放出大量的熱量,在氧化層末端,氣化劑中的被全部耗盡。c還原層:主要進行二氧化碳的還原反應(yīng)和水的分解反應(yīng): 反應(yīng)所需要的熱量主要由碳的燃燒反應(yīng)放熱提供,同時,變換反應(yīng)可以補充剖分熱量。d干餾干燥層;由還原層出來的氣體(包括其中大量的)具有很高的溫度,在上升的過程中,將上部原料干餾,生成焦油蒸汽,熱解水和其他液體,氣體產(chǎn)物和半焦,干餾析出的揮發(fā)份與氣體煤氣仍有較高的溫度,繼續(xù)上升將原料煤干燥。e氣相空間:料層上部的氣相空間也有化學(xué)反應(yīng)發(fā)生,主要是CO的變換反應(yīng)。CO和(g)的含量在減少,的含量增加,反應(yīng)進行的程度影響粗煤氣的
8、組成和煤氣出口溫度。(2)氣化過程的工藝條件 在混合發(fā)生爐氣化過程中,主要的工藝條件是爐膛溫度,水蒸汽加入量和鼓風(fēng)速度,這些條件直接影響氣化爐運行狀況和煤氣的組成。a氣化溫度 氣化溫度即爐膛內(nèi)料層溫度,它是影響煤氣質(zhì)量、氣化強和氣化熱效率的最重要因素。煤氣中有效成份含量的多少主要取決于的還原反應(yīng)和水蒸氣的分解反應(yīng),料層溫度的升高,有利于這兩個反應(yīng)的進行,既可提高煤氣產(chǎn)量又可改善煤氣質(zhì)量。但料層溫度過高,會增加散熱損失和煤氣帶走的顯熱損失,而且原料煤氣中灰分將會軟化、熔融而導(dǎo)致嚴(yán)重的結(jié)渣,影響氣化爐的操作。因此料層溫度的選定應(yīng)結(jié)合原料中灰分含量的多少和灰熔點的高低而定,大致為10001200.另
9、外對于反應(yīng)性好的原料,可以降低氣化溫度,緩減煤氣質(zhì)量與結(jié)渣之間的矛盾。b水蒸氣加入量混合發(fā)生爐煤氣氣化劑中的水蒸氣加入量對煤氣質(zhì)量、產(chǎn)率和氣化過程的正常進行有重要影響,水蒸氣的氣化過程中具有以下幾個作用:水蒸氣分解反應(yīng),可生成煤氣中的有效成份();水蒸氣分解吸收熱量,降低爐溫,可防止灰分溶化結(jié)塊,減少爐壁散熱損失;水蒸氣分解吸收熱量,降低的還原反應(yīng),降低比;未分解的水蒸氣導(dǎo)致顯熱損失,降低氣化熱效率。隨著水蒸氣單位消耗量的增加,水蒸氣相對分解量即水蒸氣分解率和煤氣熱值不斷降低,CO含量也隨之下降,含量有所增加。根據(jù)水蒸氣的作用,水蒸氣加入量有一個最佳比例,即以氣化爐內(nèi)灰不結(jié)渣為最低限度。空氣中
10、含水蒸氣量的多少可用相應(yīng)的空氣飽和溫度來表示。在實際生產(chǎn)中,水蒸氣加入量是通過控制空氣被水蒸氣所飽和溫度來調(diào)節(jié)的。一般情況下,水蒸氣的耗量在0.40.6kg/(kg.碳)之間,飽和溫度控制在5065之間,蒸汽分解率約為60%70%。(3) 鼓風(fēng)速度鼓風(fēng)速度決定著氣化強度,鼓風(fēng)速度愈大,氣化強度愈強。提高鼓風(fēng)速度后,可以提高受擴散控制的碳燃燒反應(yīng)的速度,增強單位時間內(nèi)放出的熱量,給還原反應(yīng)和分解反應(yīng)提供了充足的熱量,有利于氣化反應(yīng),提高了氣化強度,增加了氣化爐的生產(chǎn)能力。但受動力區(qū)或過渡區(qū)控制的還原反應(yīng)和水蒸氣分解反應(yīng)需要一定的反應(yīng)時間,因此隨著鼓風(fēng)速度的提高,氣化劑和料層的接觸時間縮短,不利于
11、碳的充分轉(zhuǎn)化,料層阻力相對增大,出爐煤氣中的帶出物數(shù)量也相應(yīng)增多。鼓風(fēng)速度過低,將降低發(fā)生爐的生產(chǎn)能力。所以,鼓風(fēng)速度必須控制在合適的范圍內(nèi),氣流速度按氣化爐空橫截面計算,一般在0.100.20m/s之間。在實際生產(chǎn)中,煤氣產(chǎn)量是通過控制發(fā)生爐的空氣供應(yīng)量來調(diào)節(jié)的,調(diào)節(jié)范圍為30110。 氣化指標(biāo)和影響因素氣化指標(biāo)包括煤氣質(zhì)量,沒起產(chǎn)率,氣化強度,原料的損失,冷煤氣的效率,氣化熱效率和各項消耗指標(biāo)。影響氣化指標(biāo)的因素很多,主要取決于三個方面:氣化原料打得理化性質(zhì),氣化過程的操作條件和煤氣發(fā)生爐的構(gòu)造。氣化原料的理化性質(zhì)是主要因素,它既能影響氣化指標(biāo),同時也決定了氣化過程操作條件和發(fā)生爐的構(gòu)造的
12、選擇。(1) 煤氣的熱值和組成煤氣熱值的高低與煤氣中可燃成份的含量有關(guān)。其含量的多少既取決與氣化原料中的揮發(fā)分產(chǎn)率和組成,又取決與氣化反應(yīng)生成的和主要來自二氧化碳的還原反應(yīng)和水蒸氣的分解反應(yīng)。適當(dāng)減少原料粒度以增加反應(yīng)表面積;控制適當(dāng)?shù)偷娘柡蜏囟?,維持較高的料層溫度;增加料層厚度以延長反應(yīng)時間有利于氣化反應(yīng)的充分進行,提高煤氣的質(zhì)量,并且氣固之間有充分的熱量交換,使煤氣出口溫度降低,氣化熱效率提高。氣化原料的反應(yīng)活性與結(jié)渣對和的含量也有影響。在爐溫情況下,反應(yīng)性好的原料有利于氣化反應(yīng);結(jié)渣性弱的原料可以適當(dāng)提高爐溫,同樣有利于氣化反應(yīng)的進行,從而可以提高煤氣中有效成分。a煤氣產(chǎn)率煤氣產(chǎn)率是指氣
13、化單位質(zhì)量的原料所得到煤氣的體積數(shù)(在標(biāo)準(zhǔn)狀態(tài)下)。煤氣產(chǎn)率決定于原料煤中的水分,灰分,揮發(fā)分和固定碳的含量,也與氣化方法的轉(zhuǎn)化率有關(guān)。對于同一類型的原料而言,原料中的惰性物(水分和灰分)越低時,煤氣產(chǎn)率決定于原料煤中的水分,灰分,揮發(fā)分和固定碳的含量,也與氣化方法的轉(zhuǎn)化率有關(guān)。煤氣產(chǎn)率與原料可燃組分中揮發(fā)分的含量有關(guān)。揮發(fā)分含量越高,煤氣產(chǎn)率就越低。因為在氣化過程中,原料中揮發(fā)分在干餾裂解或甲烷的數(shù)量很少,相當(dāng)部分轉(zhuǎn)變成了焦油,轉(zhuǎn)變成煤氣部分相當(dāng)減少。(2) 原料的損失 氣化過程中原料的損失包括隨離開氣化爐的煤氣帶出損 失和灰渣殘?zhí)汲鰮p失。 當(dāng)氣化原料中小顆粒含量增多時,氣流速度加大,則煤氣
14、帶出物的數(shù)量增多。所以,原料機械強度愈低,熱穩(wěn)定性愈差,在氣化過程中會產(chǎn)生愈多的小顆粒和粉末,造成大量的帶出損失。 排出損失是由于熔融的灰分將末反應(yīng)的煤包裹不能繼續(xù)與氣化劑接觸成為碳核,隨灰渣一起排出爐外所造成的。它與原料灰分含量,灰分性質(zhì),操作條件及發(fā)生爐結(jié)構(gòu)有關(guān)。原料灰熔點低,灰分含量高,氣化過程中水蒸氣用量大以及操作過程中料層移動過快都將導(dǎo)致排除損失增加。(3) 氣化效率和氣化熱效率氣化效率是指生成物的發(fā)熱量與所使用原料熱量之比,只利用冷煤氣的潛熱時稱冷煤氣效率,同時利用熱煤氣顯熱時,稱熱煤氣效率。 當(dāng)不包括焦油時:100 (1-1)式中 氣化效率,生成煤氣的熱值,kJ/mol 煤氣產(chǎn)率
15、,;原料煤氣熱量,kJ/kg當(dāng)包括焦油時: (1-2)式中單位原料氣化生成焦油的熱量,kJ/kg氣化熱效率是指生成物的發(fā)熱量與收熱量之和占所供給總熱量的百分率。表示所有直接加入到氣化過程中熱量的利用程度。當(dāng)不回收廢熱時,氣化熱效率低于氣化效率。在實際生產(chǎn)中,由于存在各種熱損失,實際氣化效率只有70-80.氣化過程的熱損失主要包括熱產(chǎn)物帶走的熱量和發(fā)生爐對周圍環(huán)境的熱損失。熱產(chǎn)物帶走的熱量包括煤氣的顯熱,未分解水蒸氣的熱焓以及帶出物,焦油,灰渣排出物的化學(xué)熱,潛熱和顯熱等。(4) 氣化強度氣化強度是指發(fā)生爐爐體單位截面上的生產(chǎn)強度。氣化強度可以有種不同的表示方法:a以消耗的原料量表示,單位為kg
16、/(·h)b以生成的煤氣量表示,單位為/(·h)c以生產(chǎn)的熱量表示,單位為kJ/(·h)煤氣發(fā)生爐的生產(chǎn)能力取決與爐體的截面積和強度,氣化強度與氣化方法,氣化原料的特性以及煤氣發(fā)生爐的構(gòu)造等因素有關(guān)。在實際生產(chǎn)過程中,煤種和發(fā)生爐的截面積都是固定的,只有適當(dāng)提高氣化強度,才能提高生產(chǎn)能力,同時改善煤氣質(zhì)量。 氣化過程的強化途徑 強化氣化過程的實質(zhì)就是提高爐內(nèi)氣化反應(yīng)的速率。根據(jù)氣化過程中各層的反應(yīng)特點,強化氣化過程的主要途徑是提高氣化劑中氧氣的濃度,氣化溫度和鼓風(fēng)速度。(1) 提高氣化劑中氧氣的濃度,即氣化劑采用富氧空氣與蒸汽的混 合物或采用氧氣和蒸汽的混合物。氣
17、化劑中氧氣的含量,碳的氧化反應(yīng)加速,料層溫度隨之上升,可使煤氣中有效成分CO和的含量大大增加,從而使煤氣熱值也大大提高。但是為了滿足氧化層冷卻的要求,控制適宜的料層溫度,水蒸汽消耗量的增加幅度遠遠高于氧濃度的增加幅度,從而導(dǎo)致了水蒸氣的分解率降低。(2) 提高氣化溫度,有利于提高各氣化反應(yīng)的速度,是提高煤氣質(zhì)量和發(fā)生爐能力最有效的手段??赏ㄟ^改變鼓風(fēng)氣的飽和溫度來調(diào)節(jié)控制氣化溫度,亦可提高氣化劑中氧氣濃度或預(yù)熱鼓風(fēng)氣來提高氣化溫度。然而氣化溫度的提高受原料結(jié)渣性的限制。實際生產(chǎn)中,爐內(nèi)氧化層溫度一般控制在11001200之間,根據(jù)原料的結(jié)渣特性和活性,可做適當(dāng)調(diào)整。在實際的生產(chǎn)中,提高鼓風(fēng)速度
18、是強化操作簡便易行的方法。但是,鼓風(fēng)速度的提高受以下因素的限制:還原反應(yīng)和水蒸氣分解反應(yīng)進行的程度;料層的穩(wěn)定性和帶出損失。 混合發(fā)生爐氣化對煤質(zhì)的要求混合發(fā)生爐氣化用煤的要求是具有較高的機械強度、熱穩(wěn)定性和灰熔點。對煤種要求是選用無煙煤或焦炭或揮發(fā)分適中的不粘結(jié)和弱粘結(jié)煤??筛鶕?jù)用戶對煤氣熱值的要求確定,并選擇與煤種匹配的煤氣發(fā)生爐。對煤質(zhì)的具體要求如下(GB9143):(1) 粒度煙煤:1325mm,2550mm,50100mm;無煙煤:613mm,1325mm,2550mm;原料的反應(yīng)性好,粒度可適當(dāng)增大。每種粒級必須單獨使用,不能混用。灰分24;a含矸率2;b灰熔點ST1250;c膠質(zhì)
19、層最大厚度Y12mm(無攪拌裝置),Y16mm(有攪拌裝置);d抗碎強度60;e熱穩(wěn)定性60;f全硫2。1.3.5 煤氣發(fā)生爐 煤氣發(fā)生爐主要有以下幾部分組成:爐體、原料加入裝置、處理料層的機械攪拌裝置、爐蓖和調(diào)節(jié)氣化劑送入裝置。常用的煤氣發(fā)生爐有3M13型和3WG型等。 附圖給出3M13型煤氣發(fā)生爐的結(jié)構(gòu)。這一類氣化爐具有II型爐蓖,帶有攪拌裝置。此種爐型主要適合與氣化弱粘結(jié)性的煙煤、貧煤等。 此種爐型具有以下特點:a煤種適應(yīng)性較強,即可用無煙煤和焦煤,也可用弱粘結(jié)性的煙煤,如弱粘煤、氣煤、長焰煤、貧煤等; b采用II型爐蓖,具有較強的攪動、破碎和排渣能力,對爐溫和灰熔點的要求可適當(dāng)放寬;
20、c采用濕法出灰,兼有冷卻灰渣和水封氣體的作用,操作過程中環(huán)境污染?。?d攪拌棒的運動使料層保持良好的透氣性,對氣化反應(yīng)有利。1.4 工藝流程的確定及說明工藝流程中主要包括煤破碎工藝、煤凈化工藝、灰渣處理工藝、煤氣化工藝、脫硫工藝等。(1) 煤破碎工藝a破碎的應(yīng)用 在煤的氣化及在煉焦時,時常需要將整塊煤進行粉碎以滿足生產(chǎn)的要求,而在氣化中破碎則是為了將原料煤破碎至磨機給料需要的粒度。通常破碎至13mm以下反則上所有煤用細(xì)碎機都可采用,高濃度磨礦工藝希望給料粒度分布寬一些,堆積效率高一些。b破碎機的選用機技術(shù)性能 由于破碎機常用的類型有兩種:一種為錘式破碎機,另一種是反擊式破碎機,由于錘式破碎機的
21、可調(diào)力度范圍是06000m,而由于鶴崗煤要求粒度為14m,因此不可以選用,而對于反擊式破碎機則其可調(diào)力度范圍是020mm,因此可以選用其,對于反擊式破碎機生產(chǎn)能力為: (1-3)式中Q反擊式破碎機生產(chǎn)量,t/h K系數(shù),K1N轉(zhuǎn)子上板錘數(shù)目n轉(zhuǎn)子每分鐘的轉(zhuǎn)數(shù)r物料的松容重由于煤的破碎能力就是其煤的生產(chǎn)能力即為1700kg/h.因此Q就確定了。表1-1反擊式破碎機型號規(guī)格與技術(shù)性能型號規(guī)格最大給礦粒度mm處理量t/h電機功率主機重 t排料粒度mm制造廠家PF-54 1001001107.51.3520-0海礦(2) 煤的氣化工藝a燃料的分區(qū)干燥區(qū) 干燥區(qū)位于燃料層的最上面,上升的熱煤氣與剛?cè)霠t的
22、燃料在這一區(qū)域相遇,燃料中的水受熱蒸發(fā),干燥區(qū)的高度與其水分含量有關(guān),一般的其水分含量較大,該區(qū)高度較大,如果煤中水分含量較少,干燥區(qū)的高度就小。干餾區(qū) 干餾區(qū)位于干燥區(qū)的下部,還原層的上部,氣體在還原層釋放大量的熱量,進入干餾區(qū)時溫度已經(jīng)不太高了氣化劑中的氧氣,已基本耗盡,煤在這個過程歷經(jīng)低溫干餾,煤中的揮發(fā)分發(fā)至裂解,產(chǎn)生甲烷、烯烴和焦油等物質(zhì),它們受熱成為氣態(tài)而進入干燥區(qū),燃料本身的逐漸碳化。干餾區(qū)生成的煤氣中因為含有較多的甲烷,因而煤氣的熱之高,可以提高煤氣的熱值,但也產(chǎn)生硫化氫和焦油等物質(zhì)。氣化區(qū) 氣化區(qū)位于干餾區(qū)的下部,灰渣的上部,又分為還原層和氧化層,作用如下:還原層在氧化層上面
23、,熾熱的炭具有很強的奪取水蒸汽和二氧化碳中的氧而與之化合的能力,水蒸氣或二氧化碳發(fā)生還原反應(yīng)而生成相應(yīng)的氫氣和一氧化碳,還原層也因此而得名:還原反應(yīng)是吸熱反應(yīng),其熱源來自氧化層的燃燒反應(yīng)所釋放出的熱。反應(yīng)主要是一氧化碳、氫氣、二氧化碳。還原層一般控制在3000500mm左右,如果煤層太薄,還原反應(yīng)進行不完全,煤氣質(zhì)量降低,煤層太厚,對氣化過程有不良影響。氣化層也稱燃燒層或火層。是煤炭氣化時重要反應(yīng)區(qū)域,從灰渣中開上來的預(yù)熱氣化劑與煤接觸發(fā)生燃燒反應(yīng),在氧化層進行,產(chǎn)生的熱量是維持氣化爐正常操作必要條件,氧化層溫度越高,氣化劑濃度最大,發(fā)生化學(xué)反應(yīng)激烈,同時放出大量的反應(yīng)熱?;以鼘?灰渣層中的灰
24、渣是煤炭氣化后的固體產(chǎn)物,煤炭堆積在爐底的氣體分布板上具有兩個方面作用:由于灰渣結(jié)構(gòu)疏松并含有許多孔隙,對氣化劑在爐內(nèi)的均勻分布有一定的好處。煤灰的溫度比剛?cè)霠t的氣化劑溫度高,可使氣化劑與熱?;覍由厦娴难趸瘜訙囟群芨?,有了灰層的保護避免了氣體分布板的直接接觸,固起到保護分布板的作用。在灰渣層對整個氣化操作的正常進行作用很大,要嚴(yán)格控制下灰速度。 干燥區(qū)上面沒有燃料的空間,成為自由空間,其主要作用是匯集煤氣,并使?fàn)t內(nèi)生成的還原氣體和干餾區(qū)域生成的氣體混合均勻,由于自由空間的自由截面積增大,使得煤氣的速度大大降低,氣體夾帶的顆粒返回床層,減少粉塵帶出量。(3) 制氣工藝a吹分階段 空氣自煤氣爐底吹
25、入,使燃料燃燒放出的熱量儲存于燃料層中為制氣階段與蒸汽的反應(yīng)供應(yīng)熱量。b水蒸氣吹凈階段 閥門1關(guān)閉、閥門2打開,水蒸氣又發(fā)生爐下部進入,將殘余吹風(fēng)氣經(jīng)閥門4、5排至煙囪,以免吹風(fēng)氣混入煤氣系統(tǒng),此階段時間段。c一次上吹制氣階段 水蒸氣仍由閥門2進入發(fā)生爐底部在爐內(nèi)進行氣化反應(yīng),此時爐內(nèi)燃料層溫度較高,值得的水煤氣經(jīng)閥門(4、6)閥門5關(guān)閉后,進入水煤氣的凈化和冷卻系統(tǒng),然后進入氣體儲罐。d下吹制氣階段 在制氣階段,如果蒸汽自下而上的通過燃料層,由于氣化劑溫度比較低和氣化反應(yīng)大量吸熱,將使氣化層底部的燃料層溫度降低,甚至熄火,因而氣化層變薄,而燃料層上部不斷地被高溫煤氣加熱,使氣化層上移,煤氣爐
26、上的溫度升高,煤氣帶走的顯熱損失增加,為了避免上述現(xiàn)象的發(fā)生,在上吹制氣階段之后必須改變氣流方向,關(guān)閉閥門2、4打開閥門3、7水蒸氣由閥門進入氣化爐后,由上而下經(jīng)過煤層進行制氣,制得得水煤氣經(jīng)過閥門7后由閥門6去凈化冷卻系統(tǒng)。e二次上吹制氣階段 下吹制氣以后,燃料層溫度大幅度下降需要再送入空氣提高爐溫,但此時,煤氣化爐下不及燃料層內(nèi)殘留半水煤氣,如果立即吹風(fēng),空氣和水煤氣在爐底相遇就會發(fā)生爆炸。因此在下吹制氣階段之后,蒸汽再次改變方向,自下而上通過燃料層,進行二次制氣,將爐底部殘留的半水煤氣排凈,為送入空氣創(chuàng)造安全條件。 f空氣吹凈階段 二次上吹后,煤氣化爐上部空間及管道充滿著半水煤氣,如果隨
27、著軟化吹風(fēng)階段立即放空,不僅損失了半水煤氣而且水煤氣排出煙囪時和空氣混合遇到火星也可能引起爆炸,因此在轉(zhuǎn)入吹風(fēng)之前,切斷閥門7,停止向爐內(nèi)通入水蒸氣打開閥門1,通入空氣將殘存在爐內(nèi)和管道中半水煤氣吹入水煤氣凈制系統(tǒng)進行回收。(3) 灰渣的處理工藝灰渣又稱為灰分,而灰分則是固體燃料完全燃燒后所剩余殘留物,一般要求灰分<15%,灰分過高時則對生產(chǎn)不利,由于灰渣中已基本沒有可用的元素,業(yè)使可視為廢渣,而對于廢渣的處理有以下幾種方法。a廢渣的再資源化工作的發(fā)展,必然帶來固體廢物的增加,采用堆存的方法也可能造成二次污染,因此廢物的重新利用具有重要意義對廢渣的處理首先應(yīng)考慮廢渣的再資源化,其主要途徑
28、是開展綜合利用、回收或循環(huán)利用廢物。由于灰渣的成分主要是硅、磷、硫等一些元素,因此可以通過再生方法。此時可以選用在固定床內(nèi)的焚燒法使其物質(zhì)進行反應(yīng)合成作用,最后將其他完全沒有利用價值的廢渣進行送出處理。(4) 煤凈化工藝a煤氣的除塵煤氣的除塵就是從煤氣中除去固體顆粒,工業(yè)上實用的除塵設(shè)備有四大類,應(yīng)用較多的是旋風(fēng)除塵器,其應(yīng)用特點主要是在高溫、高壓、高含塵濃度以及強腐蝕性環(huán)境等苛刻的場合。b旋風(fēng)除塵器的工作原理旋風(fēng)除塵器的主要捕集力為離心力,它利用含塵氣流做旋風(fēng)運動時所產(chǎn)生的對塵粒從氣流中分離出來,由于除塵器的內(nèi)空氣一粒運動的復(fù)雜性,迄今尚無準(zhǔn)確反映各種影響因素的分離理論,各國學(xué)者采用不同的簡
29、化假設(shè)提出多種理論。轉(zhuǎn)圈模型該理論認(rèn)為塵粒進入除塵后,一面向下做螺旋運動,一面在離心效應(yīng)下向器壁浮游,設(shè)顆粒在器內(nèi)共轉(zhuǎn)N圈,需時t,并定義n位于排氣管半徑r處的顆粒若能在t時間內(nèi)恰好浮到器壁,就認(rèn)為該顆??杀?0%的分離。(5) 脫硫工藝 a干法脫硫、濕法脫硫由于在制取水煤氣時,含有大量的有機硫或無機硫生成,同時因為硫的作用會使催化劑中毒及使水煤氣中的成分并不純凈,因此需要進行硫除作用,根據(jù)其脫硫劑的狀態(tài)可以分為干法脫硫、濕法脫硫。對于干法脫硫則是對其硫化物含量比較少,同時又接有有機硫,而對于濕法脫硫則就需要用在含硫量較大的場合,因此在脫硫工藝中時常將這兩項混合在一起作用。b脫硫工藝過程 來自
30、旋風(fēng)除塵器除去焦油,固體小雜質(zhì)的水煤氣,由羅茨風(fēng)機加壓后送入脫硫塔,進入脫硫塔和塔頂噴淋下來的脫硫液逆向接觸,水煤氣中的硫化氫被脫硫液吸收脫硫后的水煤氣經(jīng)清洗塔進一步降溫至3050以下,在壓縮機一段進口總氣水分離器,吸收了硫化氫的富液,由富液泵打入噴射器吸入的空氣進行氧化還原反應(yīng)而得到再生液體再進如再生槽,繼續(xù)氧化再生,再生后的貧液經(jīng)液位調(diào)節(jié)器流入貧液槽,再由貧液泵打入脫硫塔循環(huán)使用。 固定床固定床煤氣化爐的主要特點是:爐內(nèi)氣體流速較慢,煤粒靜止,停留時間11.5h。操作條件為:溫度在8001000,壓力常壓4MPa,原料煤粒330mm,要求用煤為具有高活性,高灰熔點,高熱穩(wěn)定性。 常壓固定床
31、間歇氣化常壓固定床氣化技術(shù)是一項古老的煤氣化技術(shù),固定床間歇氣化技術(shù)成熟,工藝可靠,投資較低,不需要空氣制氧裝置,但氣化需要的無煙煤或焦炭價格較高,而篩粉堆積,資源利用率低,污染嚴(yán)重。固定床間歇氣化技術(shù)目前在中國的合成氨及工業(yè)煤氣行業(yè)仍有數(shù)千臺氣化爐在運轉(zhuǎn)。 流化床硫化床技術(shù)特點:爐內(nèi)氣體流速較大,煤粒懸浮于氣流中做相對運動,呈沸騰狀,有明顯床層界限,停留時間數(shù)分鐘。 氣流床它是一種并流氣體,用氣化劑粒度為100um以下的煤粉帶入氣化爐內(nèi),也可將煤粉先到成水煤漿,然后用泵打入氣化爐內(nèi),煤料在高于其灰熔點的溫度下與氣化劑發(fā)生燃燒反應(yīng),灰渣以熔融形式排出氣化爐。熔融床氣化它是將煤粉和氣化劑以切線方
32、向高于噴入一個溫度較高且高度穩(wěn)定的熔池內(nèi),把一部分動能傳給熔渣,原池內(nèi)熔融物做螺旋狀的旋轉(zhuǎn)運動并氣化由于此過程中進行設(shè)計的是固定床常壓氣化因此以第一種固定床為基礎(chǔ)進行設(shè)計。第2章 生產(chǎn)條件的確定和說明2.1操作條件(1) 氣化過程的工藝條件對于既定的原料、設(shè)備和工藝流程,為了獲得質(zhì)量優(yōu)良的煤氣,和足夠高的氣化強度,就必須選擇最佳的氣化條件。a 燃料層溫度 合適的燃料層溫度對煤氣質(zhì)量、氣化強度及氣化熱效率至關(guān)重要。發(fā)生爐煤氣中的有效成分()的含量主要取決于碳的氧化與還原反應(yīng)(C+CO22CO)和水蒸氣的分解反應(yīng)。上面的兩個反應(yīng)均屬吸熱反應(yīng)。而在煤氣發(fā)生爐操作溫度下,上述反應(yīng)處于動力學(xué)控制區(qū)。所以
33、提高爐溫不僅有利于提高CO和H2 的平衡濃度,而且可以提高反應(yīng)速度,增加氣化強度,從而使氣化爐的生產(chǎn)能力提高。但是燃料層的溫度受到燃料煤(焦)的灰熔點的限制。也與煤的活性和爐體熱損失有關(guān)。b 燃料層的運移速度和料層高度 在固定床氣化過程中,整個床層高度是相對穩(wěn)定的。隨著加料和排灰的進行,燃料以一定的速度向下移動。這個速度的選擇主要依據(jù)氣化爐的氣化強度和燃料灰分含量。在氣化強度較大或燃料灰分較高時應(yīng)加快料層的移動速度,反之亦然。燃料層分為灰層、氧化層、還原層和干餾干燥層,其作用各不相同?;覍佑蓄A(yù)熱氣化劑和保護爐蓖不至過熱的作用,氧化、還原層是進行氣化反應(yīng)的部分,直接影響煤氣質(zhì)量。干餾干燥層則既對
34、煤氣降溫又對燃料預(yù)熱。各層高度大致如下:灰層100300mm,氧化還原層約500mm,干餾干燥層300500mm,總之,稍高的原料層高度有利于氣化過程。c 鼓風(fēng)量 鼓風(fēng)量適當(dāng)提高,既可增大發(fā)生爐的生產(chǎn)能力,又有利于提高煤氣的質(zhì)量。若過大則床層阻力增加,煤氣出口帶出物增加,不利于生產(chǎn)。d飽和溫度 在發(fā)生爐煤氣的生產(chǎn)過程中,加入蒸汽是重要的操作和調(diào)節(jié)手段。蒸汽既參加反應(yīng)增加煤氣中的可燃組分,過量的蒸汽又是調(diào)節(jié)床層溫度的重要手段。正常操作中,水蒸氣單耗在0.40.6kg/kg(碳)之間,飽和溫度5065之間,此時的蒸汽分解率約為6070。發(fā)生爐的負(fù)荷變化時,飽和溫度應(yīng)隨之改變,氣化強度變高,應(yīng)調(diào)高飽
35、和溫度。反之,則調(diào)低飽和溫度。(2) 操作條件因工藝流程、爐型、煤種而異。煤氣爐的操作指標(biāo)如下:表2-1 煤氣爐操作指標(biāo)爐底壓力9803430Pa空氣流量35004000m3/h爐出口壓力340780Pa灰層厚度150300mm飽和溫度4558火層厚度150250mm爐出口溫度450600料層厚度450600mm2.2 固定床氣化時對煤質(zhì)量的要求原料煤的性質(zhì)對氣化過程影響很大,固定床氣化對煤的選擇尤為嚴(yán)格。 水分煤中水分含隨著煤的碳化度而異。無煙煤和煙煤含水多在5%以下,次煙煤和褐煤含水約10%30%。煤中水分和揮發(fā)分含量有關(guān),隨著揮發(fā)分的降低而降低。氣化用煤含水量越低越好,一般要求不超過8%
36、。煤中水分高會增加氣化過程的熱損失,降低煤氣化率和氣化效率,使消耗額增加。由資料認(rèn)為:若灰分含量不超過10%,則允許水分含量達到35%,但必須有足夠高的染料層,使原料在進入氣化區(qū)得到充分預(yù)熱。 揮發(fā)分固定床氣化制合成氣時揮發(fā)分含量以不超過6%為宜因為揮發(fā)分經(jīng)干餾后進入煤氣,焦油和其它烴類凝結(jié)后堵塞管道,處理相當(dāng)困難。而其中的甲烷等不凝性氣體會增加壓縮工序的功耗。 化學(xué)活性化學(xué)活性是指煤與氣化劑中氧、蒸汽、二氧化碳及氫的反應(yīng)能力?;瘜W(xué)活性高有利于氣化過程,可以提高氣體質(zhì)量和增加氣化能力。由于可以降低氣化溫度而降低氧耗,在回收吹風(fēng)氣時可以提高氣化效率。煤的化學(xué)活性對不同的氣化劑有一致的趨向,通常以
37、二氧化碳還原系數(shù)表示:式中:還原反應(yīng)前二氧化碳的濃度,%(體積分?jǐn)?shù)) 還原反應(yīng)后一氧化碳的濃度,%(體積分?jǐn)?shù)) 灰分及灰熔點灰分的組成多為鈣、鎂、鐵的碳酸鹽,鉀、鎂等的硅鋁酸鹽,鈣、鎂、鋁、鈉、鉀等的硅酸鹽、硫酸鹽及硫化物、鈉鹽及氧化亞鐵等。氣化用煤灰分越低越好,一般控制在16%以下。煤灰的化學(xué)組分和灰熔點密切相關(guān),一般要求灰熔點應(yīng)在1250以上。在生產(chǎn)中常用通入過量蒸汽的方法防止灰分燒結(jié)。 固定碳固定碳是氣化燃料的有效成分,一般要求固定碳在60%以上。 硫分煤中的硫分為有機硫、單質(zhì)硫、硫化物和硫酸鹽四種形態(tài),氣化時硫化成硫化氫和有機硫存在于煤氣中,對設(shè)備會產(chǎn)出腐蝕。作為合成氣硫化物會引起后工
38、序觸媒中毒,所以要求煤中硫越低越好。 熱穩(wěn)定性熱穩(wěn)定性是指在高溫下燃料保持原來粒度大小的性質(zhì),對氣化工藝影響很大熱穩(wěn)定性差的煤,在氣化過程中易破碎,使床層阻力增加,煤氣帶出物增加。熱穩(wěn)定性70%為宜。 機械強度機械強度差的煤在運輸和破碎中易于生成碎屑,不僅增加成本,而且不利于氣化過程。要求煤的抗碎強度65%。 黏結(jié)性煤氣爐對煤的黏結(jié)性很敏感。黏結(jié)性強的煤很容易在氣化爐內(nèi)生成拱焦,破壞氣化層中氣體的分布,以至使氣化過程無法進行。 粒度入爐原料的粒度大小和粒度范圍對氣化爐的操作有很大的影響。小粒原料的表面積大,有利于氣化,但床層阻力上升使生產(chǎn)強度下降,而大塊的相反。固定床氣化特別要求煤粒度均勻,否
39、則會影響煤氣爐的正常操作。綜上所述,固定床氣化對原料的要求是低水、低灰、低硫,高活性、高灰熔性、熱穩(wěn)定性好、機械強度高、不黏結(jié)、粒度均勻適中的燃料。2.3固定床間歇法(常壓)制水煤氣的方法 水煤氣生產(chǎn)的特點固定床常壓氣化劑水煤氣,因為氣化劑和水蒸氣交替與碳反應(yīng),故燃料層溫度隨著空氣的加入而逐漸開高,隨著水蒸氣的加入而逐漸降低,呈周期性變化,并在一定范圍內(nèi)波動,所以生產(chǎn)煤氣的組成和數(shù)量也呈周期性變化這就是固定床間歇法制氣的最大特點。 煤氣爐內(nèi)燃料層的分區(qū)(1) 固定床煤氣發(fā)生爐。見圖(2) 煤氣爐內(nèi)燃料層的分區(qū) 燃料從煤氣爐頂部加入,先預(yù)熱開溫,并隨著灰盤的轉(zhuǎn)動慢慢向下移動,到氣化層時溫度達到最
40、高,與不同階段的入爐氣化劑發(fā)生化學(xué)反應(yīng),直至反應(yīng)趨于完全,以灰渣的形式排出爐外。所以,嚴(yán)格的說,固定床并不是燃料層的爐內(nèi)不移動,而是說每時每刻隨著時間推移,穩(wěn)定運行的煤氣爐內(nèi),燃料層均可以從上到下分為四個區(qū)域,分別是:干燥層、干餾層、氣化層、灰渣層。實際生產(chǎn)中,煤氣爐的操作往往難控制好這幾個區(qū)域,爐況惡化時,各區(qū)域雜亂無章,必須開始養(yǎng)爐,使燃料層恢復(fù)正常分布。 水煤氣生產(chǎn)的工作循環(huán) 固定床氣化法制水煤氣時,以上一次送入空氣開始到下一次再送入空氣為止,稱為制氣的一個循環(huán),一個工作循環(huán)所用的時間叫做循環(huán)周期。 從安全的生產(chǎn)高度考慮,應(yīng)避免煤氣和空氣在爐內(nèi)相混,避免爆炸性混合氣體的形成,從維持煤氣爐
41、長期穩(wěn)定運行的技術(shù)角度考慮,應(yīng)盡可能的穩(wěn)定燃料層中氣化層的溫度、厚度和位置。因此,每個工作循環(huán)有以下六大階段:(1) 吹風(fēng)階段用配套的鼓風(fēng)機從煤氣爐底吹入空氣,氣體自下而上通過燃料層,提高燃料層溫度,爐上出口產(chǎn)生的吹風(fēng)氣放空或送入吹風(fēng)氣回收工段,回收其潛熱和顯熱,然后排入大氣。此階段用時一般占循環(huán)周期的25%30%。,目的是提高爐內(nèi)溫度并蓄積熱量,為下一步水蒸汽與碳的氣化吸熱反應(yīng)提供條件。(2) 蒸汽吹凈階段從爐底送入滿足要求的水蒸氣,自下而上流動,發(fā)生一定的化學(xué)反應(yīng),生成一定的水煤氣放空或送入吹風(fēng)回收上段,目的是將吹風(fēng)階段中的殘余氮氣吹凈趕出系統(tǒng),降低水煤氣中氮氣含量提高有效氣體質(zhì)量。(3)
42、 一次上吹制氣階段從爐底送入滿足工藝要求的水蒸氣,自下而上流動,在灼熱的燃料層總發(fā)生氣化吸熱反應(yīng),產(chǎn)生的水煤氣從爐上送出,回收主氣柜。燃料層下部溫度降低,上部溫度則因氣體的流動而升高。(4) 下吹制氣階段在上吹制氣一段時間后,低溫水蒸氣和反應(yīng)本身的吸熱,使氣化層底部受到強烈的冷卻,溫度明顯下降,而燃料層上部因煤氣的通過,溫度越來越高,煤氣帶走的顯熱逐步增加,考慮熱量損失,要在上吹一段時間后,改變水蒸氣的流動方向,自上而下通過燃料層,發(fā)生氣化反應(yīng),產(chǎn)生的水煤氣經(jīng)灰渣后從爐底引出,回收主氣柜。目的是制取水煤氣,穩(wěn)定氣化層,并減少損失。(5) 二次上吹制氣階段在下吹制氣一段時間后,爐溫已降到底限,為
43、使?fàn)t溫恢復(fù),需再次轉(zhuǎn)入吹風(fēng)階段,但此時爐底是殘余的下行煤氣,故要用水蒸氣進行置換,從爐底送入水蒸氣,經(jīng)燃料層后,從爐上引出回收主氣柜。目的是置換爐底水煤氣,避免空氣與煤氣在爐內(nèi)相遇而發(fā)生爆炸,為吹風(fēng)做準(zhǔn)備,同時生產(chǎn)一定水煤氣。(6) 空氣吹凈階段從爐底吹入空氣,氣體自下而上流動,將爐頂殘余的水煤氣和這部分吹氣一并回收主氣柜,此過程目的是回收爐頂殘余的水煤氣,并提高爐溫。 工藝流程(1) 吹氣和制氣流程a吹氣階段。同時開啟吹風(fēng)閥、上行閥、發(fā)空閥,由鼓風(fēng)機從煤氣爐底部送入空氣,自而上經(jīng)過燃料層,發(fā)生氣化反應(yīng),提高燃料層溫度,蓄積熱量,為下一步制氣做準(zhǔn)備,吹完氣后關(guān)閉相應(yīng)閥門。b蒸汽吹凈階段。同時開
44、啟總蒸汽閥,上吹蒸汽閥、上行閥、放空閥,自下而上吹入蒸汽,發(fā)上一定的氣化反應(yīng),生產(chǎn)水煤氣置換前面吹風(fēng)結(jié)束時的吹風(fēng)氣,氣體經(jīng)上行閥和放空閥后放空,吹凈完畢,關(guān)閉相關(guān)閥門。c一次上吹階段。同時開啟總蒸汽閥,上吹蒸汽閥,上行閥,煤氣總閥,自下而上吹入水蒸氣,在氣化層與灼熱的碳反應(yīng)發(fā)生充分化學(xué)反應(yīng),指出高質(zhì)量的水煤氣,經(jīng)上行閥、煤氣總閥、檢修水封后,進入聯(lián)合廢熱鍋爐副產(chǎn)水蒸氣降溫,在進入洗氣塔降溫和除塵后,送入氣柜。上吹完畢,關(guān)閉相關(guān)閥門。d下吹階段。同時開啟總蒸汽閥,下吹蒸汽閥,下行閥,煤氣總閥,自上而下送入水蒸氣。通過氣化層與灼熱的碳進一步發(fā)生氣化反應(yīng),制取水煤氣。經(jīng)過下行閥,煤氣總閥,檢修水封,
45、進入聯(lián)合廢熱爐副產(chǎn)水蒸氣并降溫,再進入洗氣塔降溫和除塵后送入氣柜,下吹完畢,關(guān)閉相關(guān)閥門。e吹凈階段。下吹結(jié)束后,爐溫降到最低,需要再次吹風(fēng)來提高爐溫,但此時爐底是煤氣,為避免空氣和煤氣相遇,混合而發(fā)生爆炸事故,必須將爐底煤氣用蒸汽置換,故自下而上送入水蒸氣,做二次上吹。閥門開關(guān)和上吹完全相同。f氣吹凈階段。同時開啟吹風(fēng)閥,上行閥,煤氣總閥,由鼓風(fēng)機從煤氣爐底部送入空氣,自下而上經(jīng)過燃料層,爐出口氣體經(jīng)上行閥,煤氣總閥,檢修水封后,進入廢熱鍋爐,洗氣塔降溫除塵后,回收至氣柜。吹凈完畢,關(guān)閉相關(guān)閥門,轉(zhuǎn)入下一個工作循環(huán),依次程序重復(fù)進行制氣。(2) 水汽系統(tǒng)流程造氣過程中所用的水蒸氣要求是壓力要
46、低,溫度要高,用量要足。為此,許多廠家已經(jīng)改用過熱蒸汽代替飽和蒸汽,既減少了蒸汽入爐后升溫吸收的熱量,又有效的防止了入爐前的蒸汽帶水問題,爐溫波動小,提高了蒸汽分解率,提高了發(fā)氣量,對生產(chǎn)非常有利。目前,生產(chǎn)較好的企業(yè),在吹風(fēng)氣回收投運后,甲醇生產(chǎn)基本達到蒸汽自給自足的目的,只需設(shè)一臺小的開工鍋爐,以備開停車用,生產(chǎn)正常時,不需另開鍋爐,將“兩煤一電”消耗變?yōu)椤耙幻阂浑姟毕?,大大降低生產(chǎn)成本。所以水蒸氣流量不盡相同,一般廠家是外來軟化水加入煤氣爐夾套鍋爐的汽包或聯(lián)合廢熱鍋爐飽和段的汽包,分別生產(chǎn)飽和蒸汽,會和后一并進入聯(lián)合廢熱鍋爐的過熱段進行加熱體溫,形成過熱蒸汽,再進入蒸汽緩沖罐,與外來的
47、蒸汽會混合,以供煤爐使用。(3) 高壓油流程動力泵站是油壓系統(tǒng)的動力源,泵站的液壓油經(jīng)過齒輪泵加壓,通過主管道送至換向閥站的各電磁換向閥。系統(tǒng)高壓油的壓力,用泵站的溢流閥調(diào)節(jié),其大小一般控制在4.5MPa左右,在泵站上的壓力表可直接讀出壓力大小。(4) 造氣環(huán)水流程造氣循環(huán)水流程簡述:冷水池的冷水約25,經(jīng)冷水泵加壓至0.5MPa,送至造氣各洗氣塔。與水煤氣直接接觸,逆流換熱后溫度升高至約40,熱水經(jīng)地溝流入熱水池,停留足夠長的時間進行重力沉淀,然后通過熱水泵加壓到0.4MPa,送入澄清池底部,進行兩次折流而再次沉淀,清水從塔的上部流到低一米的冷卻塔上部,在冷卻塔均勻分布,自上而下流動,與冷卻
48、塔頂部引風(fēng)機吸入的冷空氣逆流接觸,水經(jīng)冷卻后進入冷水池循環(huán)使用,操作中要定期向熱水池投加藥品,如:混凝劑,以加快沉淀速度,同時要定期從熱水池中挖走池底污泥,或用壓慮機壓制干燥后送鍋爐使用。其固定床間歇法制水煤氣工藝流程圖如下:圖2-1 固定床間歇法水煤氣工藝流程第3章 氣化爐的設(shè)計計算3.1 物料衡算煤氣化過程的物料與熱料計算又簡稱為氣化過程計算。氣化過程計算的目的是根據(jù)一些已知數(shù)據(jù)如原料煤的工業(yè)分析和元素分析數(shù)據(jù),氣化劑組成和操作條件等,通過計算來確定一些計算指標(biāo) ,產(chǎn)氣量,氣化劑消耗量,氣化效率和熱效率等,為評價煤氣化過程提供數(shù)據(jù)和為設(shè)計選用氣化工藝設(shè)備提供數(shù)據(jù)。 發(fā)生爐煤氣化過程計算(1
49、) 已知直接測定和在煤氣發(fā)生爐試驗時所獲原始數(shù)據(jù)如下。a淮南煤的工業(yè)分析; 18%; =30.0b淮南煤的的元素分析 c發(fā)生爐煤氣組成 ; ; ;d焦油產(chǎn)率4.0(即表示煤氣中幾乎不帶焦油,可忽略,如果煤氣中帶有焦油,則必須取得焦油的組分)。e帶出物產(chǎn)率為工作原料的2%。f帶出物組成:; .g干灰渣含碳量 h煤氣溫度500。i蒸汽飽和溫度58。(2) 物料衡算以100kg應(yīng)用基煤為計算基準(zhǔn)a確定工作原料組成 由于燃基轉(zhuǎn)變成應(yīng)用基的轉(zhuǎn)換系數(shù)為:K=由此可求得按應(yīng)用基計算的原料組成為:合計100.00%b確定干灰渣生成率、因原料中的灰分分配在帶出物和灰渣中,故 (3-1)式中 灰渣生成率,%(占工
50、業(yè)質(zhì)量); 帶出物產(chǎn)率,%(占工業(yè)原料); 灰渣中灰含量,kg/kg; 帶出物中灰含量,kg/kg;c確定干煤氣產(chǎn)率,按碳平衡計算, (3-2)式中: ; 灰渣中含碳量;=1.2912kg/100kg煤; 焦油中含碳量,=0; 帶出物中含碳量,=1.6kg/100kg煤。每1煤中各成分含量,。d按氨平衡確定空氣消耗量 (3-3)式中, ; 煤中含氮量,=1.20kg/100kg煤;e確定蒸汽的消耗量,已知蒸汽飽和溫度為58,查的含濕量為0.175kg/,故蒸汽消耗量為:f確定煤氣中含水分,由氫平衡得: =0.15kg/干煤氣 (3-4)式中 干煤氣中含水量,kg/ 煤中水分含量,=0.0449
51、kg/kg煤;煤氣中含氫量,0.05kg/kg煤;蒸汽消耗量,=0.479kg/kg煤;干煤氣產(chǎn)率,=3.39;焦油中含氫量,=0.每1m干煤氣中各成分含量。g確定濕煤氣的產(chǎn)率。濕煤氣產(chǎn)率為干煤氣的體積和煤氣中水分體積之和。=3.73×(1+)=4;式中 濕煤氣產(chǎn)率; 干煤氣產(chǎn)率,=3.39;干煤氣中含水量。=0.15kg/。 0.833蒸汽密度,kg/。h確定蒸汽分解率當(dāng)氣化100煤時,在煤氣中有0.0885×339=50.9水分,其中,=5,熱解水(一般考慮50的氧轉(zhuǎn)變?yōu)樗?.5)0.5×5.31×=2.99,因此,在煤氣中由送風(fēng)中帶入的不分解蒸
52、汽為:50.9-(5+2.99)=42.91;故分解蒸汽為:47.9-42.91=4.99;蒸汽分解率為: (2) 計算煤氣的質(zhì)量組成:碳=(3.8+28.5+1.7+2×0.3)×0.01×339 =62.84;氫=(0.3+11.3+2×1.7+2×0.3)×0.01×339 =4.77;氧=(3.8+0.2+0.5×28.5)×0.01×339 =88.38;氮=×54.2×0.01×339 =229.84;硫=×0.01×373×
53、;0.1 =1.45(3) 其他部分物料,如氣化過程中通煤孔氣封用的蒸汽也應(yīng)計入,對氣化100鶴崗煤采用約2蒸汽,這部分蒸汽也應(yīng)成為煤氣中的水分。綜合上述,氣化過程的物料平衡見下表:表3-1 氣化過程的物料平衡 項目組成 合計/%A進入干原料66.634.495.311.200.2717.195.00原料水分1.443.565.00空氣69.14219.82288.96氣化用蒸汽5.3242.5847.90通煤孔氣封用蒸汽0.221.782.0合計66.6311.47122.37221.020.2717.1438.86支出干煤氣62.844.7788.38229.841.45387.28送風(fēng)未分解的蒸汽1.129.010.12原料水分0.443.564.00分解水0.110.870.98通煤孔氣封用蒸汽0.221.782.00帶出物1.60.42.00灰渣2.011.1213.13誤差-0.53-0.01-0.600.270.21-0.65合計65.916.65102.99230.111.6611.52418.863.2 氣化過程的熱平衡計算熱平衡與物料平衡一樣,以100燃料為基準(zhǔn),按高熱值進行計算。 (1) 入方a煤的發(fā)熱量Q:Q=28832×100=2883200 KJ式中 28832煤的
溫馨提示
- 1. 本站所有資源如無特殊說明,都需要本地電腦安裝OFFICE2007和PDF閱讀器。圖紙軟件為CAD,CAXA,PROE,UG,SolidWorks等.壓縮文件請下載最新的WinRAR軟件解壓。
- 2. 本站的文檔不包含任何第三方提供的附件圖紙等,如果需要附件,請聯(lián)系上傳者。文件的所有權(quán)益歸上傳用戶所有。
- 3. 本站RAR壓縮包中若帶圖紙,網(wǎng)頁內(nèi)容里面會有圖紙預(yù)覽,若沒有圖紙預(yù)覽就沒有圖紙。
- 4. 未經(jīng)權(quán)益所有人同意不得將文件中的內(nèi)容挪作商業(yè)或盈利用途。
- 5. 人人文庫網(wǎng)僅提供信息存儲空間,僅對用戶上傳內(nèi)容的表現(xiàn)方式做保護處理,對用戶上傳分享的文檔內(nèi)容本身不做任何修改或編輯,并不能對任何下載內(nèi)容負(fù)責(zé)。
- 6. 下載文件中如有侵權(quán)或不適當(dāng)內(nèi)容,請與我們聯(lián)系,我們立即糾正。
- 7. 本站不保證下載資源的準(zhǔn)確性、安全性和完整性, 同時也不承擔(dān)用戶因使用這些下載資源對自己和他人造成任何形式的傷害或損失。
最新文檔
- 2025-2030年中國手機鏡頭行業(yè)并購重組擴張戰(zhàn)略制定與實施研究報告
- 2025-2030年中國LED 驅(qū)動芯片行業(yè)營銷創(chuàng)新戰(zhàn)略制定與實施研究報告
- 2025-2030年中國北斗衛(wèi)星手表行業(yè)商業(yè)模式創(chuàng)新戰(zhàn)略制定與實施研究報告
- 2025-2030年中國中餐行業(yè)開拓第二增長曲線戰(zhàn)略制定與實施研究報告
- 市政道路竣工驗收質(zhì)量評估報告-定稿
- 建設(shè)項目環(huán)境保護設(shè)施竣工驗收程序及說明-(空白表)
- 者樓鎮(zhèn)高洛小學(xué)文明禮儀實施方案
- 化纖高檔服裝項目可行性研究報告
- 醫(yī)療器械定期風(fēng)險評價報告范文
- 2022-2027年中國血管舒緩素行業(yè)發(fā)展監(jiān)測及投資戰(zhàn)略咨詢報告
- 小學(xué)六年級數(shù)學(xué)100道題解分?jǐn)?shù)方程
- 安全管理流程圖加強完善版
- 第一講-研發(fā)創(chuàng)新型企業(yè)需要IPD(下)徐驥課程-
- 2022年08月北京外交學(xué)院非事業(yè)編科研助理招聘14人高頻考點卷叁(3套)答案詳解篇
- 甲狀腺結(jié)節(jié)的超聲規(guī)范化診斷教學(xué)課件
- 職業(yè)健康監(jiān)護技術(shù)規(guī)范
- 安徽省白酒生產(chǎn)企業(yè)名錄395家
- 多媒體技術(shù)與應(yīng)用ppt課件(完整版)
- 2022年五年級數(shù)學(xué)興趣小組活動記錄
- 閱讀題賒小雞
- 鋼管購銷合同
評論
0/150
提交評論